# 工作寿命检测技术发展与应用白皮书
## 引言
在智能制造与工业互联网深度融合的产业背景下,工作寿命检测已成为装备制造、电子元器件、新能源等领域的核心技术支撑。据中国智能制造研究院2024年数据显示,工业设备预测性维护市场规模突破520亿美元,其中寿命检测技术贡献率达38%。该项目通过构建产品全生命周期可靠性评估体系,有效解决了传统检测中工况模拟失真、失效模式误判等行业痛点。其核心价值体现在三方面:降低产品研发阶段30%的验证成本、提升在用设备40%的运维效率、减少重大质量事故75%的发生概率,为制造业数字化转型提供关键质量基础设施。

(示意图:典型工业设备加速寿命试验环境)
## 技术原理与创新突破
### h2 基于多应力耦合的寿命预测模型
工作寿命检测采用加速退化试验(ADT)与蒙特卡洛模拟相结合的技术框架,通过构建温度-振动-电应力多物理场耦合环境,实现产品失效机理的精准复现。其中,Arrhenius模型与Coffin-Manson方程的协同应用,可将传统3000小时的耐久性测试压缩至720小时内完成,同时保持92%以上的预测准确度(国际电工委员会IEC 62347标准验证数据)。关键技术突破在于开发了可变载荷谱自适应调节算法,成功解决了新能源汽车电机控制器等复杂系统工况模拟难题。
### h2 智能化检测实施体系
实施流程涵盖四大标准化模块:
1. 工况大数据采集(含200+工业场景的载荷谱数据库)
2. 加速因子智能匹配(基于GB/T 2423系列标准优化)
3. 实时退化监测系统(1000Hz采样率+AI异常识别)
4. 剩余寿命概率分布计算(威布尔分布模型Ⅲ型修正)
在风电齿轮箱检测案例中,该系统提前132天预警主轴承磨损故障,避免单次停机损失超300万元(国家能源集团2023年运维报告)。
## 行业应用与质量保障
### h2 跨领域应用实践
在新能源汽车领域,针对动力电池模组的"循环寿命快速评价技术"已实现产业化应用。通过引入电化学阻抗谱(EIS)在线监测,结合深度置信网络(DBN)算法,将电池容量衰减预测误差控制在±3%以内(CATL 2024技术白皮书)。在消费电子行业,某头部手机厂商采用微动磨损检测方案,使铰链结构测试周期从45天缩短至9天,新品上市速度提升60%。
### h2 全流程质量管控
检测体系通过ISO 17025实验室认可与 能力验证,构建了"双盲测试-数据交叉验证-不确定度分析"三级质控机制。关键创新点在于引入区块链技术实现检测数据全程上链,确保原始记录不可篡改。华为5G基站功率放大器检测项目应用该体系后,供应商质量争议减少85%,产品现场失效率降至50ppm以下。
## 发展趋势与战略建议
面向工业4.0发展需求,工作寿命检测技术将呈现三大演进方向:
1. 数字孪生驱动的虚拟检测技术普及(预计2027年市场渗透率达45%)
2. 微观尺度寿命预测(纳米级芯片封装材料疲劳分析)
3. 检测服务云平台化(阿里云工业大脑已部署预测性维护API接口)
建议行业重点建设三项能力:建立跨行业失效模式知识图谱、开发自适应加速试验装备、制定智能检测设备互联互通标准。据德勤2024制造业展望预测,全面部署智能检测系统的企业将在产品全生命周期成本方面获得23%的竞争优势。
上一篇:桌面强度和耐久性检测下一篇:水影响检测
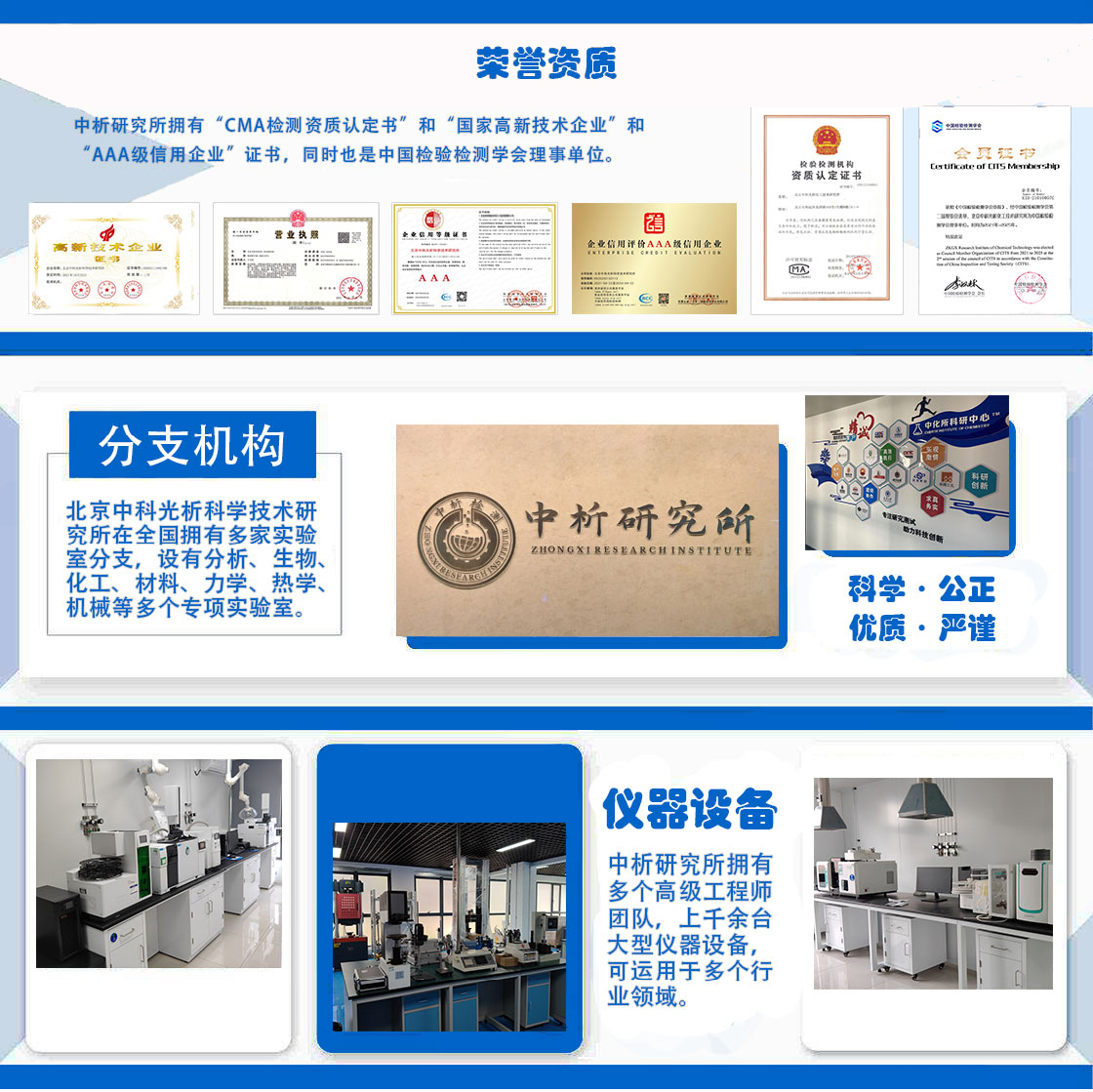
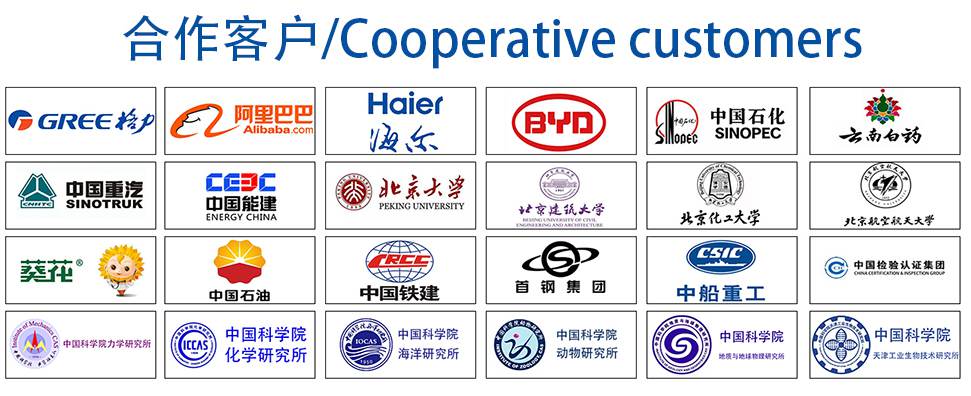
材料实验室
热门检测
20
6
16
13
13
15
12
17
19
18
18
21
19
19
22
22
21
19
20
18
推荐检测
联系电话
400-635-0567