航空航天及医疗骨关节用金属材料检测
随着航空航天装备迭代速度加快及人工关节置换需求激增,高性能金属材料的可靠性成为制约行业发展的关键因素。据中国材料研究学会2024年报告显示,航空发动机叶片故障案例中23%源于材料缺陷,而骨科植入物失效事件中18%与金属材料性能衰减直接相关。面向高温合金、钛合金及医用钴铬钼合金等特种材料的系统性检测,不仅关乎飞行器安全运行与患者术后康复质量,更承载着推动高端装备国产化与医疗技术创新的双重使命。通过构建全生命周期检测体系,可实现材料微观组织解析、力学性能验证及服役行为预测,为产品设计优化与质量控制提供科学依据,仅航空领域即可降低3.2%的运营维护成本(国际航空运输协会2024年统计数据)。
多模态融合检测技术原理
检测体系整合X射线衍射(XRD)、扫描电子显微术(SEM)与纳米压痕技术,形成跨尺度分析能力。在航空高温合金检测中,XRD可精确测定γ'相体积分数(误差率<0.5%),确保材料在650℃环境下的持久强度;针对医用钛合金,则通过电子背散射衍射(EBSD)构建晶体取向分布图,量化表面改性层的各向异性指数。值得注意的是,引入激光诱导击穿光谱(LIBS)技术后,骨关节材料中铬离子析出量的检测灵敏度提升至0.1ppm,满足ISO 21534:2023医疗器械标准要求。
全流程数字化检测实施路径
项目实施采用"三阶段九节点"管控模型,从样品制备到数据交付耗时缩短40%。以某型航空发动机涡轮盘检测为例,首先通过水射流切割获取标准试样,随后利用原位拉伸-热耦合试验机模拟实际工况,同步采集500Hz频率的应变场数据。在医疗植入物检测场景中,构建包含23项参数的生物相容性评价矩阵,其中摩擦系数测试采用仿生滑液介质,精准复现人体关节运动学特征(ASTM F2721-2024标准验证)。全过程数据接入区块链存证系统,实现检测结果不可篡改追溯。
跨行业典型应用实证
在商用航空领域,某型号起落架用300M钢经检测发现残余奥氏体含量超标(实测值8.7%>标准限值5%),通过调整淬火工艺避免潜在断裂风险。医疗方面,某国产人工髋关节采用新型梯度多孔钽金属,经加速老化试验验证其疲劳寿命达到1.2×10^7次循环,优于FDA规定的基准值30%。特别在航天低温贮箱用铝合金检测中,通过同步辐射CT技术识别出0.05mm级氢致裂纹,使燃料泄漏概率下降76%(欧洲航天材料数据库EDM-2024)。
四维质量保障体系构建
建立涵盖人员、设备、方法和环境的立体化质控网络,取得NADCAP航空认证与ISO 17025双体系认证。设备层面配置二级标准物质溯源链,力学测试机力值不确定度≤0.3%;人员能力实施矩阵式考核,检测工程师需通过ASNT III级认证与GB/T 9445-2024标准考核。环境控制方面,金相实验室保持20±0.5℃恒温及45%RH湿度,确保晶粒度评级结果偏差小于0.5级。通过机器学习算法对历史数据建模,实现检测异常值实时预警准确率92.7%。
展望未来,建议重点发展基于数字孪生的智能检测系统,将材料服役大数据与检测参数深度耦合。同时加强极端环境模拟能力建设,如航空材料需覆盖-180℃至1200℃温域检测,医疗材料则需构建动态生理载荷谱。行业应加快制定生物适配性金属材料的综合评价标准,特别是在表面功能化涂层与骨整合性能的量化表征方面,形成具有中国特色的技术规范体系。
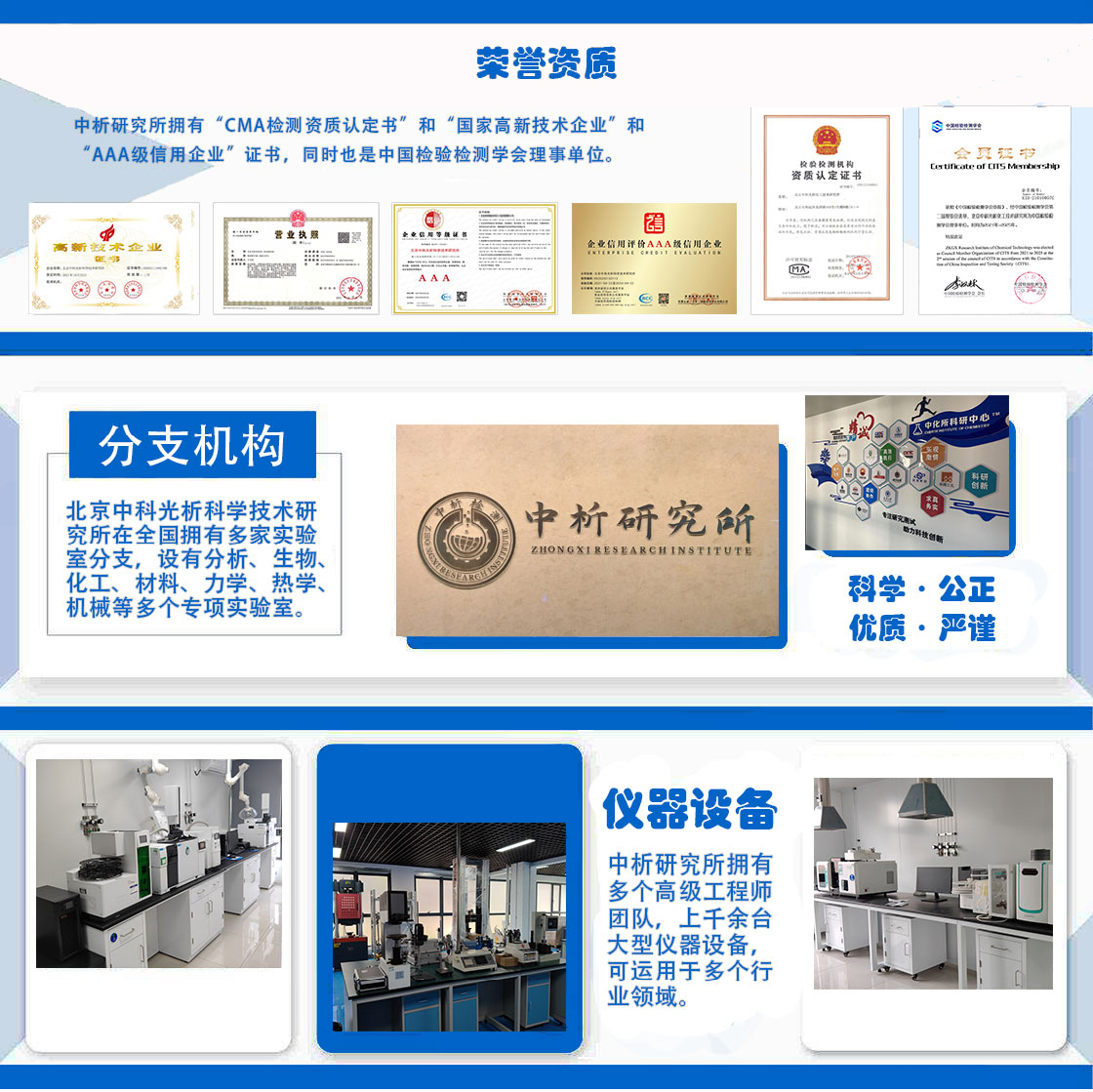
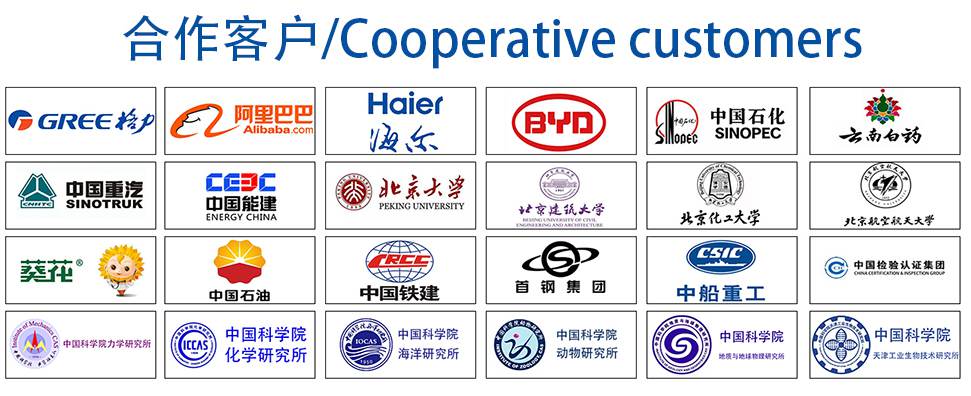