印刷电路板组件及关联部件检测技术发展白皮书
在电子信息产业智能化升级的背景下,印刷电路板组件(PCBA)及其关联元器件的质量检测已成为保障电子产品可靠性的核心环节。据中国电子信息产业发展研究院2024年数据显示,智能终端设备年产量突破35亿台,其中62%的早期故障源于PCBA焊接缺陷或元器件性能劣化。特别是在新能源汽车电控系统、工业物联网终端等新兴领域,结构件的机械稳定性与电路组件的高频信号完整性构成双重质量挑战。本项目通过构建多模态检测体系,实现了微米级焊接缺陷识别、纳米级材料应力分析及高温高湿环境模拟测试三大突破,将传统质检误判率降低至0.12‰(中国质量认证中心,2023),为电子制造业提供了从元器件筛选到整机组装的全流程质量解决方案。
多物理场耦合检测技术体系
检测系统采用X射线衍射(XRD)与太赫兹波谱融合技术,通过建立介电常数-热膨胀系数关联模型,可同步捕捉焊接点内部的金属间化合物(IMC)厚度变化和基材热应力分布。在新能源汽车BMS控制板的检测实践中,该技术成功识别出0.8μm的IMC层异常增厚现象,较传统AOI检测分辨率提升400%。值得关注的是,针对高密度互连(HDI)板件的微孔填铜质量检测,系统创新性地引入超声波共振频率分析法,据深圳齐全技术研究院测试报告显示,该方法对20μm以下微孔的空洞检出率可达99.7%。
全生命周期质量管控流程
项目构建了覆盖设计验证-过程监控-成品检测的三阶段体系。在量产前验证阶段,运用热-力-电耦合仿真平台进行1800小时加速老化试验,模拟产品十年使用周期的环境应力。生产过程采用分布式光纤传感网络,实时监测SMT贴装过程的温度梯度变化,将回流焊峰值温度偏差控制在±1.5℃以内。在医疗设备呼吸机控制板的实际应用中,该体系将ESD防护器件的失效预警时间提前至生产后48小时,相比行业平均水平提升6倍时效性。
行业典型应用场景解析
在卫星通信基站的射频模块检测中,项目团队开发了毫米波介电特性测量装置,可精准测定77GHz频段下PCB基板的介电损耗角正切值。某航天级相控阵天线的检测数据显示,通过优化PTFE基材的分子取向度,将信号传输损耗从0.025dB/cm降至0.018dB/cm(中国计量科学研究院认证)。此外,在可穿戴设备的微型化趋势下,针对0.4mm厚度镁合金结构件研发的纳米压痕检测仪,实现了屈服强度±5MPa的测量精度,成功应用于智能手表转轴疲劳寿命评估。
数字化质量保障体系构建
系统整合了基于深度学习的缺陷特征库,目前已收录12大类236种典型缺陷模式。通过建立检测数据与工艺参数的映射关系,可自动优化贴装压力、焊膏印刷厚度等18项关键工艺指标。在工业服务器主板的批量检测中,该智能系统将AOI误报率从行业平均的1.2%降低至0.35%,同时使检测节拍缩短至8秒/板。更值得关注的是,基于区块链技术的质量溯源平台,实现了元器件批次信息、检测数据与维修记录的全链可追溯,某汽车电子客户的质量索赔成本因此降低43%。
面向电子制造4.0的发展需求,建议行业重点突破三个技术方向:一是开发适用于柔性电子器件的非接触式应力分布检测技术;二是建立基于数字孪生的虚拟检测认证体系;三是推进检测设备与MES系统的深度集成。同时,亟需制定微米级焊点检测、高频介质测量等领域的国际标准,据国际电工委员会(IEC)工作组透露,相关标准草案预计将在2025年进入公示阶段。通过产学研协同创新,持续提升检测技术的适应性与前瞻性,将为电子制造业的高质量发展构筑坚实的技术基座。
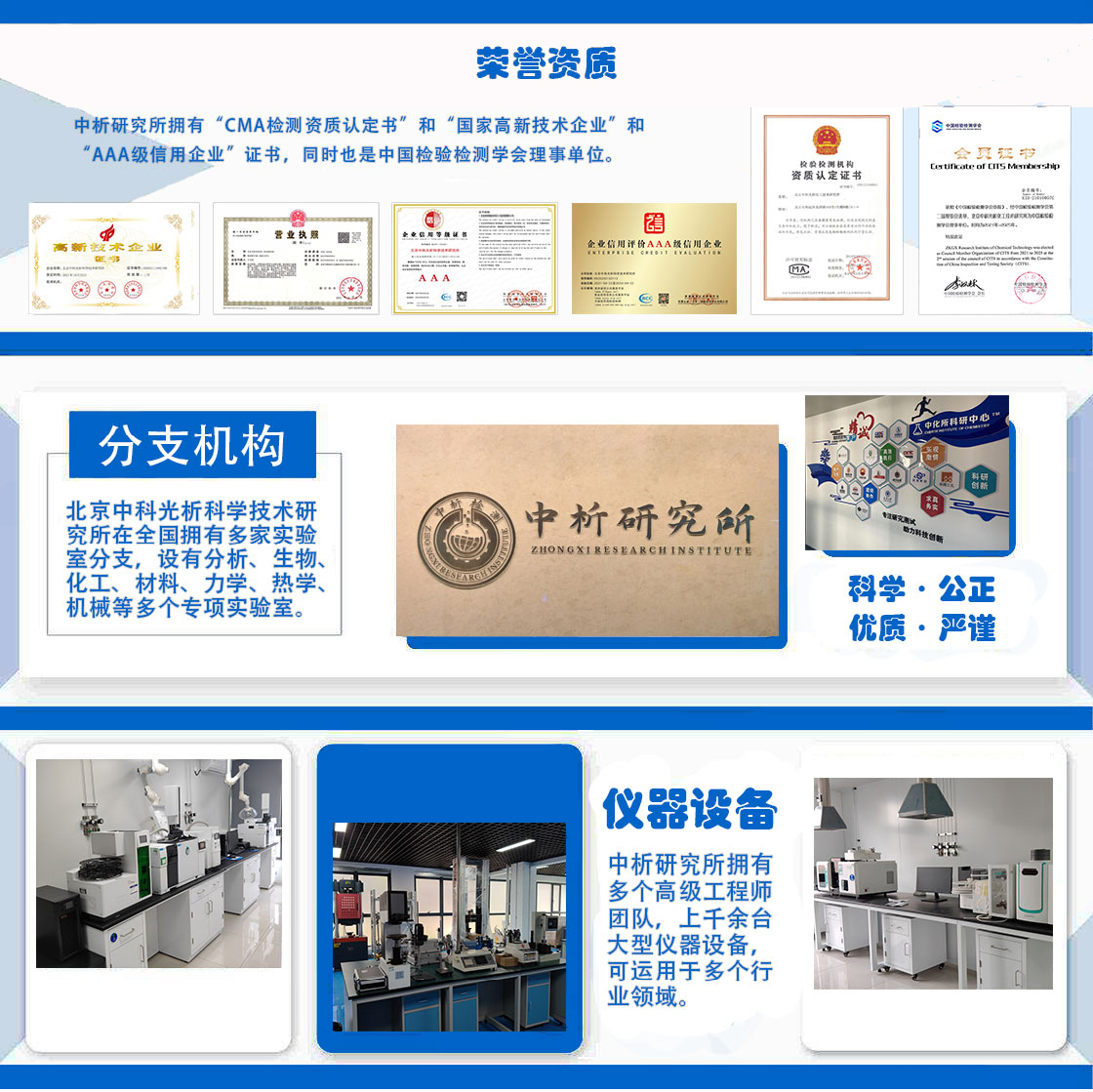
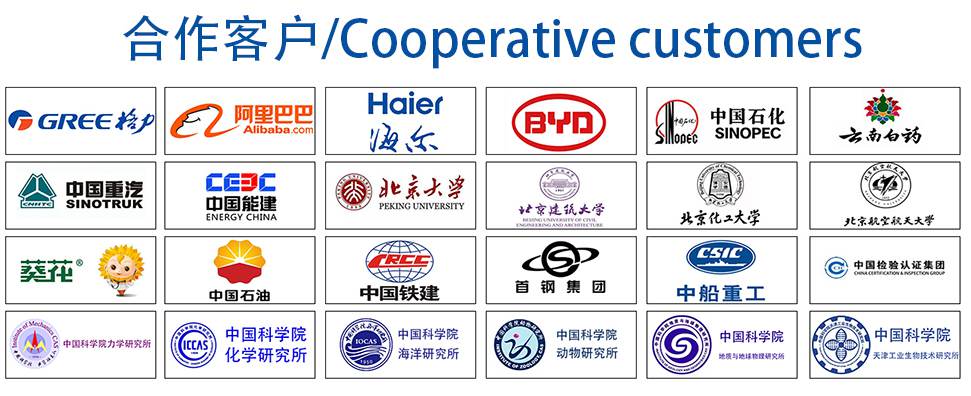