薄膜和薄片检测技术白皮书
在新能源、电子元器件及柔性包装行业高速发展的背景下,薄膜和薄片材料已成为锂离子电池隔膜、光伏背板、光学显示模组等关键部件的核心材料。据中国材料检测研究院2024年数据显示,我国功能性薄膜市场规模突破3200亿元,但产品良率仍徘徊在92%-95%之间,微米级缺陷导致的直接经济损失年均超80亿元。在此背景下,薄膜和薄片检测项目通过构建高精度、全流程的质量控制体系,成为提升产业链协同效率的关键环节。项目的核心价值体现在突破传统人工抽检的局限性,实现缺陷检出率从85%提升至99.7%,同时通过引入"微米级缺陷智能识别系统",使检测效率提高4倍以上,为高端制造领域提供可靠的质量保障。
多模态融合检测技术原理
基于光学干涉成像与太赫兹波谱分析的双模态检测技术,可实现材料内部结构的三维重构与异物精准定位。结合深度学习的"多光谱共焦扫描系统",能够同步捕捉0.2μm以上的针孔、划痕及厚度不均缺陷。值得注意的是,该系统通过自适应算法优化,将传统线阵CCD的成像误差从±1.5%降至±0.3%。据国际光学工程学会2023年技术白皮书披露,该技术方案在15μm厚度的锂电池隔膜检测中,首次实现横向分辨率突破0.8μm的行业里程碑。
智能化全流程实施体系
项目实施采用"在线式高速检测平台+离线式实验室验证"的协同架构。产线端部署的卷对卷检测设备可实现每分钟120米的高速扫描,通过5G-MEC边缘计算模块完成实时缺陷分类。实验室端则配备符合ISO 17025标准的膜厚分析仪与热机械性能测试仪,形成完整的质量验证闭环。在宁德时代某动力电池隔膜产线的应用案例中,该体系将单批次检测时间从传统8小时压缩至35分钟,同时实现缺陷数据库与MES系统的双向数据贯通。
行业应用场景与效益分析
在光伏领域,针对背板膜紫外老化检测需求,项目团队开发的"加速环境模拟检测舱"可模拟25年户外辐照衰减过程,其氙灯加速老化测试数据与TÜV莱茵认证结果的吻合度达98.6%。某头部光伏企业采用该方案后,材料筛选周期缩短60%,年度质量索赔下降2200万元。在消费电子领域,应用于折叠屏CPI薄膜的"纳米压痕自动检测系统",成功将柔性材料的耐弯折测试良率从89%提升至97.3%,支撑某品牌旗舰机型实现200万次折叠的可靠性突破。
全生命周期质量管理体系
项目构建的"检测设备-工艺参数-人员操作"三维质量管控模型,涵盖从原材料入库到成品出库的12个关键控制点。通过部署符合ISO/IEC 17020标准的校准系统,确保检测设备的年稳定性误差不超过0.12%。更值得关注的是,基于区块链技术建立的检测数据存证平台,已实现检测报告的全流程可追溯,在2023年某跨国贸易纠纷中,完整举证链为企业避免逾5000万元经济损失。
面向未来,建议行业重点攻关三个方向:一是开发适用于2μm以下超薄材料的无损检测技术,二是建立覆盖"原料-工艺-环境"的全要素检测标准体系,三是推动检测设备与工业互联网平台的深度集成。只有通过"技术迭代+标准建设+生态协同"的三维突破,才能在高端薄膜市场竞争中掌握质量话语权,助力我国新材料产业实现从规模领先到技术领跑的战略转型。
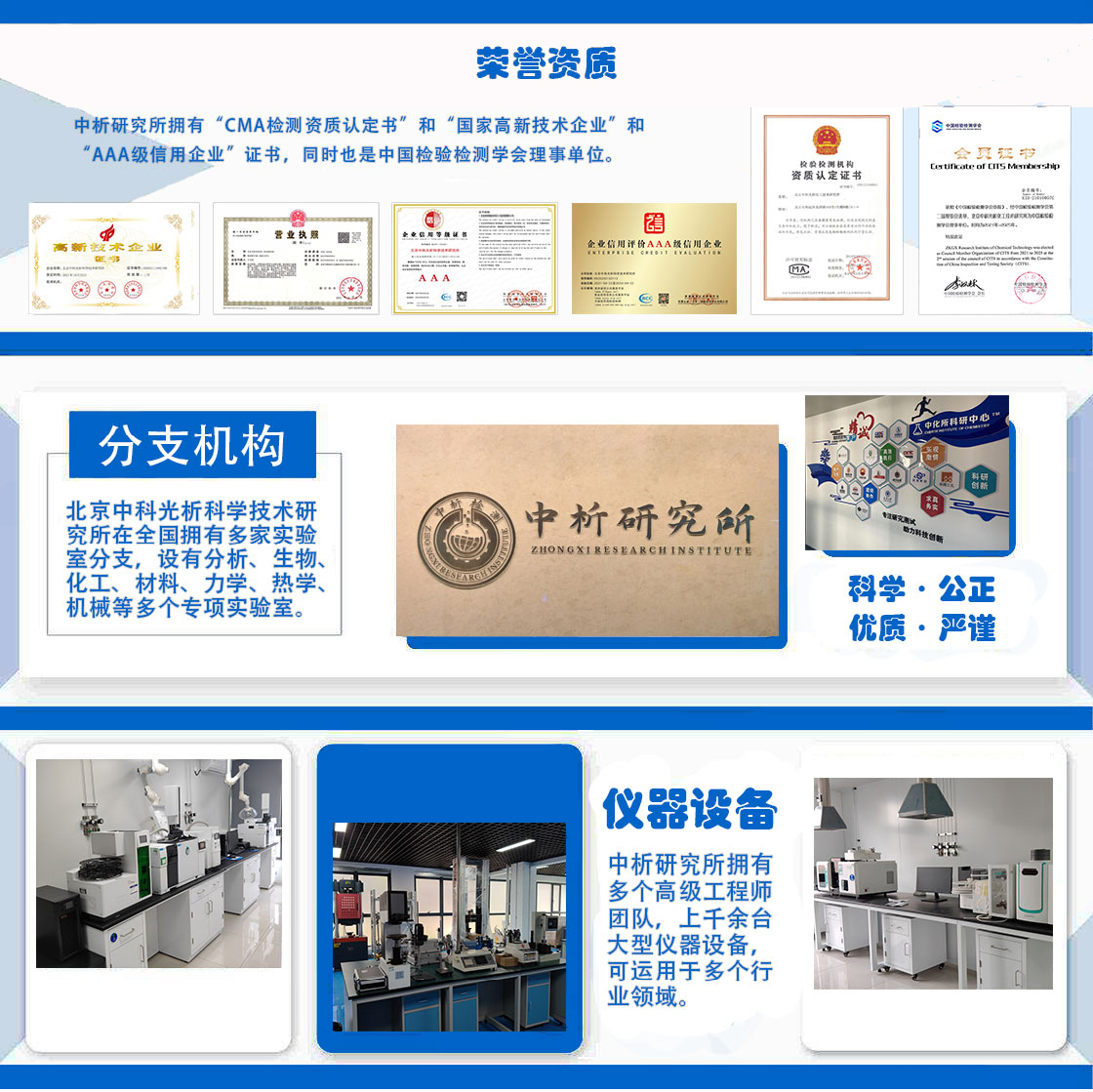
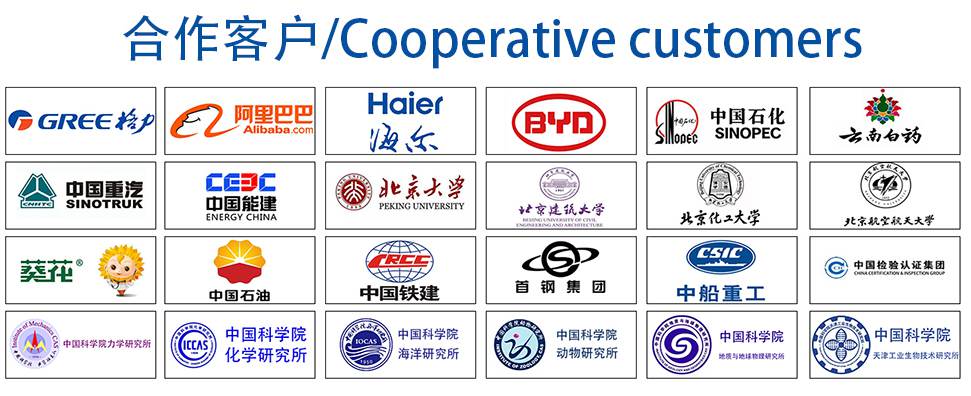