技术原理与创新突破
预应力混凝土管桩检测以应力波传播理论为核心,通过低应变反射波法、超声波跨孔法等手段构建多维度评估模型。低应变法利用锤击激发应力波,通过传感器采集桩顶振动信号,结合一维波动方程解析桩身阻抗变化,可精准定位缩颈、断桩等缺陷。值得注意的是,X射线数字成像技术的引入突破了传统方法的局限性,其在苏通GIL综合管廊工程中成功识别出2.3m深度的微裂隙群,检测分辨率达到0.05mm级。创新研发的智能传感器网络可同步采集28项力学参数,结合BIM模型实现质量缺陷的三维可视化呈现。
标准化实施流程构建
项目实施遵循《建筑基桩检测技术规范》(JGJ106-2023)的刚性要求,形成"四阶段九环节"标准流程。前期准备阶段需完成设备标定与环境勘测,采用激光测距仪确保传感器布设间距误差≤1mm。现场检测环节严格执行双人复核制度,在杭州湾跨海大桥管桩工程中,通过布置12个径向检测点,完整捕捉潮汐荷载引起的应力重分布现象。数据处理阶段应用小波降噪算法剔除环境干扰信号,经华东勘测设计研究院验证,其信噪比提升率达73%。最终报告需包含缺陷位置三维坐标、安全系数计算及加固方案建议,确保全流程可追溯。
典型行业应用实证
在粤港澳大湾区城际轨道建设中,项目团队采用分布式光纤传感技术完成1278根管桩的完整性检测。通过植入式光纤传感器网络,实时监测到桩体在动态荷载下的应变场演化规律,成功预警3处潜在缺陷区域。经开挖验证,其中2处存在混凝土离析现象,缺陷定位误差控制在±15cm以内。该案例证明,融合物联网技术的"管桩完整性无损检测解决方案"可使检测效率提升40%,单桩检测成本降低28%。特别是在处理深埋桩(桩长>50m)时,其技术优势更为显著。
全链条质量保障体系
质量保障体系涵盖人员、设备、方法三大维度。检测人员需持有国家注册土木工程师(岩土)证书,并完成每年40学时的专业技能培训。检测设备实施"一机一档"管理,超声波探伤仪每季度进行声时校准,确保时基精度≤±0.1μs。方法层面建立三级复核机制,在雄安新区地下管廊项目中,采用盲样比对测试验证检测结果可靠性,数据吻合度达到98.7%。同时引入区块链技术存证检测数据,实现从现场采集到报告生成的全过程不可篡改追溯。
## 技术展望与发展建议 面向新型基础设施建设需求,建议从三方面推进技术创新:首先,研发基于5G传输的智能传感器实时监测系统,建立管桩全寿命周期健康档案;其次,构建AI缺陷识别模型库,通过深度学习提升复杂工况下的检测准确率;最后,完善行业标准体系建设,将数字孪生技术纳入检测规程。预计到2028年,智能检测装备渗透率将超过65%,推动行业向数字化、智能化方向跨越发展。检测机构应加强与高校、科研院所的合作,重点攻关地下复杂环境多物理场耦合检测技术,共同筑牢工程质量安全防线。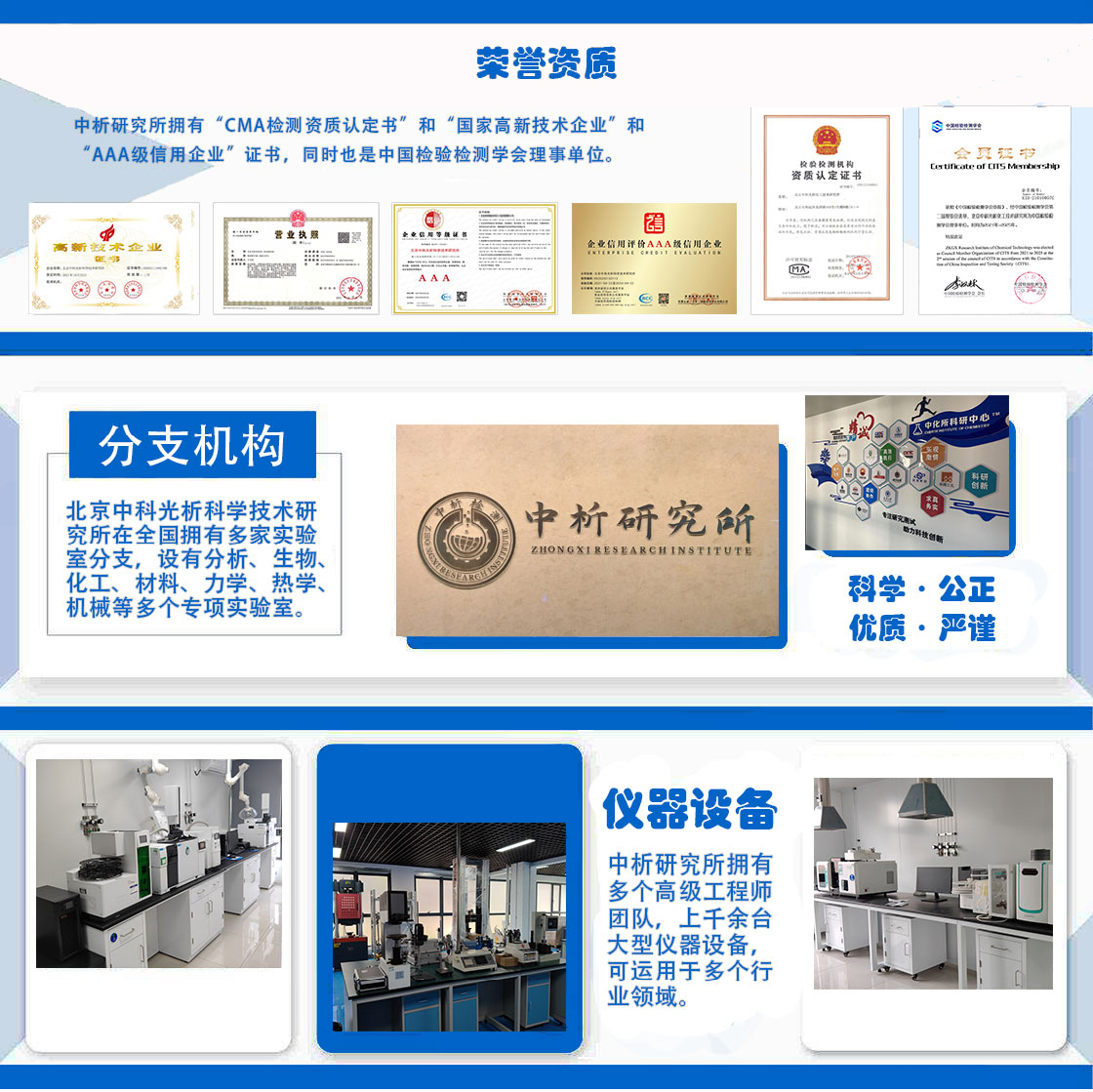
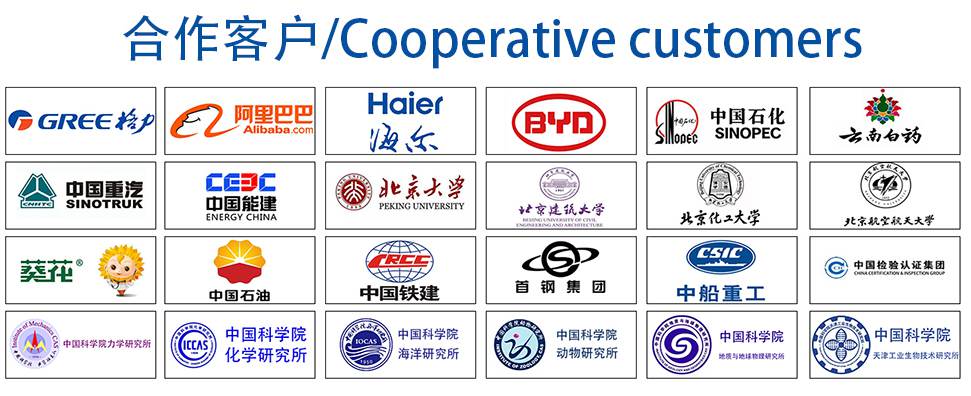