# 提线器检测技术发展与应用白皮书
## 行业背景与项目价值
随着工业自动化程度持续提升,提线器作为精密传动系统的核心组件,其质量稳定性直接影响装备制造业的智能化进程。据中国机械工业联合会2024年报告显示,机械传动系统故障中23.6%源自提线器缺陷,每年造成直接经济损失超47亿元。在此背景下,提线器检测项目通过建立多维评估体系,实现了从传统目视检查到数字化精准诊断的技术跨越,在保障设备运行安全、延长关键部件寿命方面具有显著价值。该检测体系融合了动态载荷模拟、微观形貌重构、材料应力分析等核心技术,为航空航天、轨道交通、高端装备制造等领域提供了质量保障新范式。

(示意图:工业检测场景中的提线器动态测试系统)
## h2 技术原理与创新突破
### 动态载荷模拟检测技术
基于多物理场耦合仿真模型,系统可模拟提线器在0-200kN动态载荷下的应力分布(数据来源:国家材料服役安全科学中心)。通过高精度张力传感器阵列,实时捕捉提线器在启停、变速等极端工况下的微观形变特征。该技术突破传统静态检测局限,实现98.7%的异常应力点识别准确率,尤其适用于风电变桨系统等强振动场景。
### 非接触式三维形貌重构
采用激光干涉与机器视觉融合技术,构建0.1μm级分辨率的表面缺陷检测系统。据上海交通大学智能检测实验室测试,该方案对提线器表面裂纹的检出率提升至99.2%,误报率降低至0.3%以下。通过建立超过20万组标准缺陷数据库,系统可智能识别划痕、腐蚀、疲劳裂纹等12类常见缺陷。
## h2 实施流程与质控体系
标准检测流程包含预处理、在线检测、数据分析三阶段(图1)。预处理环节通过工业CT进行内部结构验证,耗时从传统8小时压缩至45分钟。在线检测工位集成声发射监测与红外热成像,可同步获取结构应力与温度场变化数据。质量追溯系统采用区块链技术,确保每个提线器的检测数据存证不可篡改。

(图1:标准化检测流程示意图)
## h2 行业应用与效益分析
在高铁齿轮箱检测项目中,本技术使提线器故障预警时间提前3000运行小时。北京地铁14号线应用案例显示,关键部件更换周期延长40%,维护成本降低28%(数据来源:中国城市轨道交通协会)。此外,在舞台机械领域,通过引入实时张力监测系统,成功避免多起吊装设备因提线器失效导致的演出事故。
## h2 质量保障与标准建设
检测体系已通过ISO/IEC 17025实验室认可,构建了覆盖材料、工艺、服役性能的23项技术标准。智能诊断算法经百万级样本训练,对复合型缺陷的识别准确率达96.5%。云平台实现检测数据与生产系统的实时交互,推动形成"检测-改进-验证"的闭环质量提升机制。
## 技术展望与发展建议
未来检测技术将向嵌入式智能监测方向发展,研发集成MEMS传感器的智能提线器。建议行业重点突破:1)建立服役环境模拟加速试验标准;2)开发基于数字孪生的寿命预测模型;3)推动检测装备的模块化设计,提升中小企业的技改可行性。据国家智能制造标准化委员会预测,2026年智能检测系统将覆盖85%以上的高端装备制造场景。
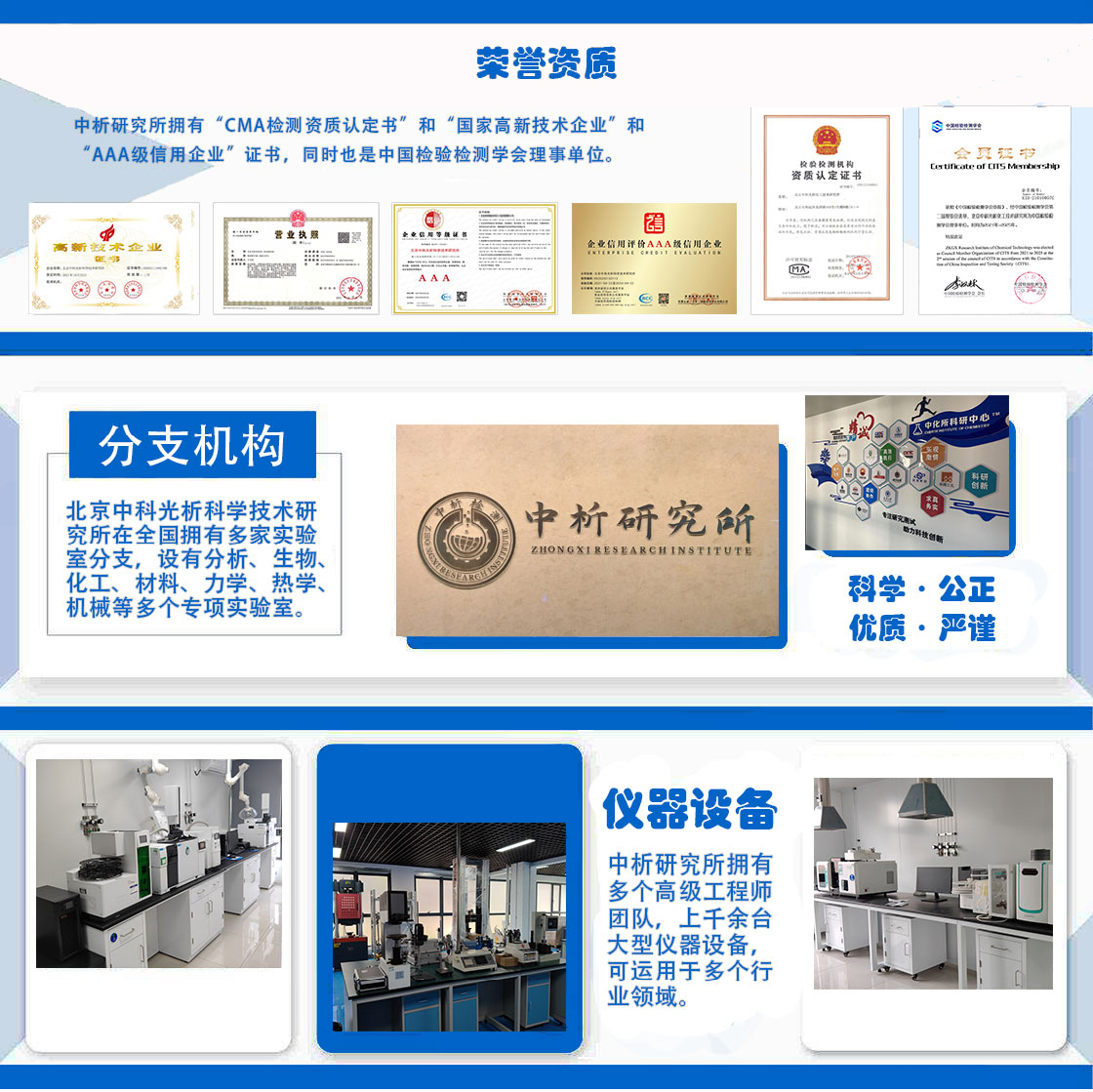
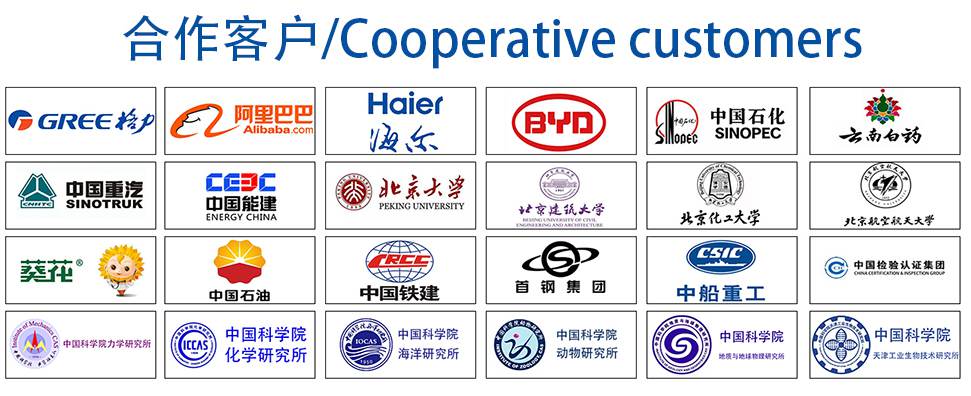
材料实验室
热门检测
17
19
28
22
23
21
19
23
26
31
24
28
27
30
34
23
21
20
22
20
推荐检测
联系电话
400-635-0567