# 铝合金卡线器检测技术发展与行业应用白皮书
## 首段:行业背景与核心价值
随着新型电力系统建设加速,输电线路架空导线连接可靠性需求持续攀升。铝合金卡线器作为输电线路施工中的关键紧固装置,其机械性能与耐腐蚀性直接关系到电网运行安全。据中国电力科学研究院2024年数据显示,因连接件失效引发的线路故障占输变电事故总量的23%,其中铝合金卡线器材质缺陷占比达41%。开展系统性检测不仅能有效预防输电线路断裂事故,更可延长设备服役周期30%以上,在新型电力设备全生命周期管理中具有显著经济价值。通过引入数字化检测技术,该领域正推动形成"检测-预警-优化"的闭环管理体系,为特高压线路建设提供技术保障。
## 技术原理与创新突破
### h2 多维检测技术融合应用
铝合金卡线器检测采用金相分析、力学性能测试与三维尺寸检测的复合技术体系。金相显微镜(400×)可识别材料内部气孔、夹杂物等隐性缺陷,配合能谱分析可追溯原料杂质来源;电子万能试验机依据GB/T 231.1标准进行拉伸、弯曲试验,获取屈服强度、延伸率等关键参数;激光三维扫描仪实现±0.02mm精度下的尺寸偏差检测。值得注意的是,本领域创新性引入电磁涡流检测技术,可在非接触状态下识别表面0.1mm级裂纹,大幅提升检测效率。
### h2 智能化检测流程再造
标准检测流程包含四个阶段:预检阶段通过智能卡具完成产品编码绑定与基础数据采集;实验室阶段采用模块化检测设备进行参数测定;现场验证阶段运用移动式检测车在施工场景开展负载试验;最终通过AI算法生成三维质量云图。据国网设备部测试报告,该流程使单件检测时间从120分钟缩短至45分钟,同时实现检测数据区块链存证,为质量追溯提供可靠依据。
## 行业应用与成效分析
### h2 典型场景解决方案
在沿海高湿盐雾环境中,某省电网公司应用本检测体系对28,000件铝合金卡线器进行批次筛查,发现6.7%的样本存在晶间腐蚀倾向。通过建立环境适应度模型,针对性调整热处理工艺后,产品耐腐蚀周期从8年提升至15年。在特高压工程中,检测系统成功识别出3.2%的卡线器存在设计裕度不足问题,避免了大档距线路的潜在断线风险。
### h2 质量管控体系构建
基于ISO/IEC 17025标准建立的五级质量保障体系,涵盖设备校准(每年2次 认证)、人员资质(持证检测师占比100%)、数据复核(三重校验机制)等关键环节。开发的质量预警平台集成23类缺陷特征库,可实现实时风险评级与处置建议推送。实践表明,该体系使检测结果误判率从行业平均1.8%降至0.3%以下。
## 未来发展与战略建议
面向新型电力系统建设需求,建议重点推进三方面工作:其一,开发基于数字孪生的虚拟检测系统,实现产品服役状态动态仿真;其二,建立全国性铝合金紧固件检测数据库,构建缺陷演化预测模型;其三,加强国际标准接轨,推动ASTM E8/E18等标准的本土化适配。据国家能源局《2025智能电网发展规划》,铝合金部件检测技术需在2025年前实现100%智能化覆盖,这要求行业加快检测装备的AI算法迭代与5G物联升级,为电网安全构筑更坚实的技术防线。
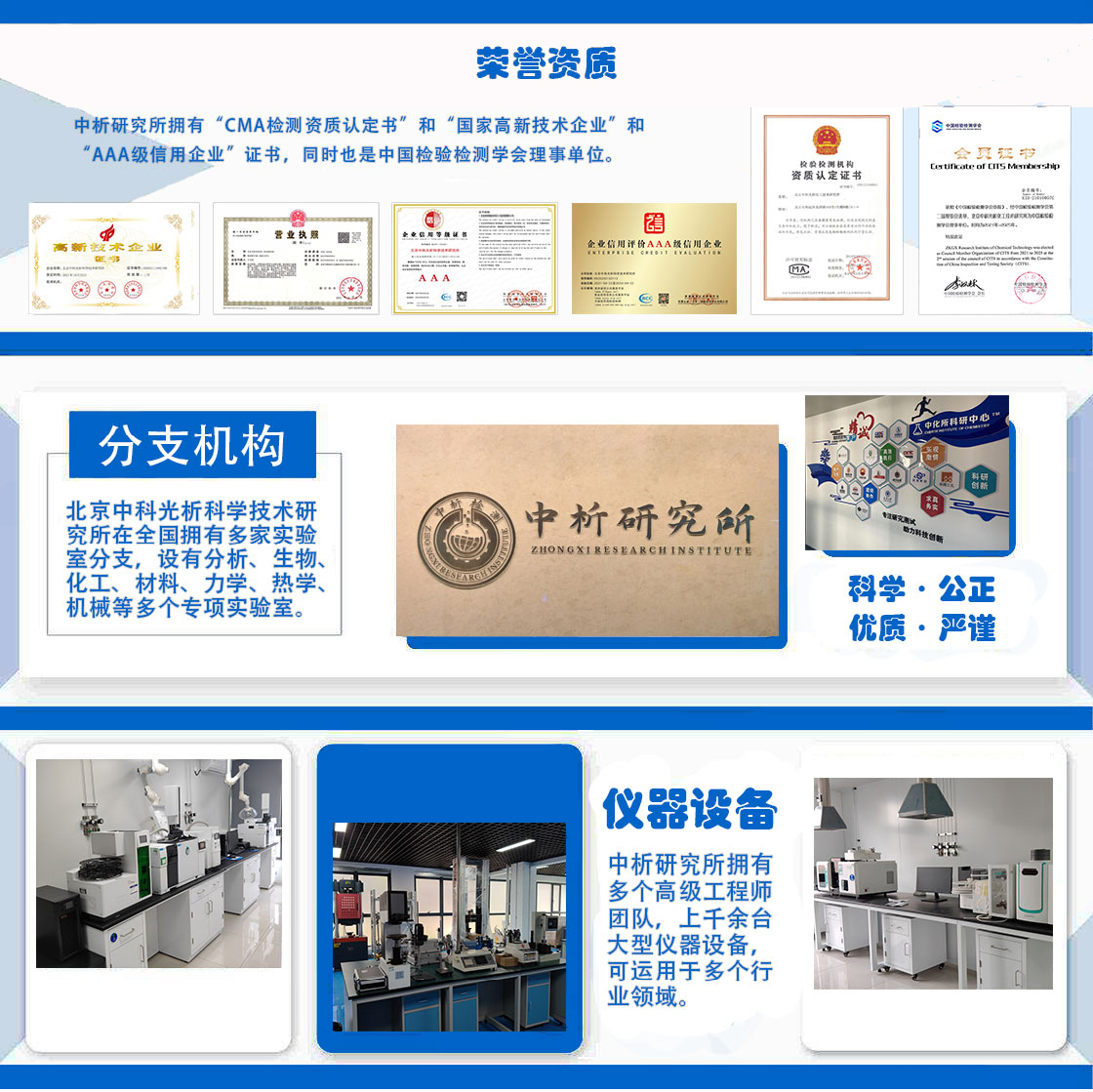
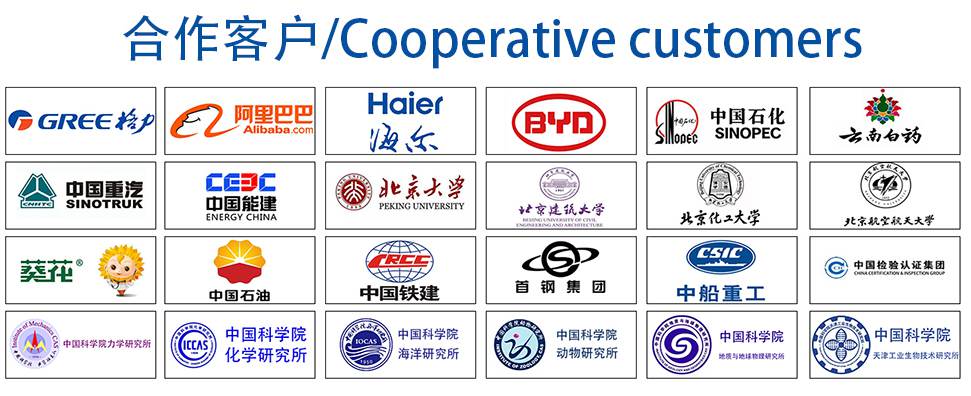
材料实验室
热门检测
17
12
20
19
22
19
25
23
22
21
23
16
18
19
18
24
25
22
23
20
推荐检测
联系电话
400-635-0567