丝杠检测技术发展白皮书
在智能制造2025战略推动下,精密传动部件检测已成为装备制造业升级的关键环节。丝杠作为数控机床、工业机器人、航空航天设备的核心传动元件,其几何精度直接决定设备定位精度与使用寿命。据国家精密机械研究院2024年数据显示,我国高端滚珠丝杠进口依存度仍达68%,其中检测技术差距导致的良品率低下是主要制约因素。开展系统化丝杠检测项目,不仅能提升国产丝杠的传动定位精度(平均提升0.005mm/300mm),更可降低设备维护成本30%以上。该项目通过构建多维评价体系,实现了微米级形位公差检测与服役性能预测的双重突破,为精密制造领域提供全生命周期的质量保障方案。
2.1 基于多传感融合的检测原理
现代丝杠检测系统采用激光干涉仪、电感测微仪与机器视觉的协同工作机制。在导程误差检测环节,基于JIS B1192标准搭建的双频激光干涉系统可实现±0.3μm/m的测量精度。对于滚道表面缺陷检测,集成500万像素工业相机与环形LED光源的视觉系统,配合改进型YOLOv5算法,使表面裂纹识别率达到99.7%。特别在动态检测领域,自主研发的六维力传感器阵列可同步采集轴向刚度、启动力矩等12项动态参数,形成完整的"高精度滚珠丝杠动态检测技术"解决方案。
2.2 智能化检测实施流程
典型检测流程包含预处理、在位测量与数据分析三个阶段。预处理环节采用超声波清洗与恒温平衡技术,确保样件达到ISO 3408规定的检测环境要求。在位测量阶段通过模块化测头系统,在30分钟内完成导程误差、轴向间隙、预压扭矩等28项关键指标的自动采集。数据分析平台运用数字孪生技术,将检测数据与设计模型比对后生成3D偏差云图,并输出包含剩余使用寿命预测的质量评估报告。该"丝杠传动系统在线监测方案"已在上海电气等企业实现日均检测120支的生产节拍。
2.3 行业应用典型案例
在汽车制造领域,某变速箱生产线应用本检测系统后,丝杠装配合格率从92%提升至99.5%。通过实时监测预紧力波动,成功将某型号工业机器人重复定位精度稳定在±0.008mm(中国机床工具工业协会2023年认证数据)。航空航天领域更突破性地实现了Φ80mm大直径丝杠的螺旋线误差检测,检测效率较传统方法提升4倍,为某型号卫星展开机构提供了关键质量保障。
2.4 全链条质量保障体系
项目构建了覆盖原材料到服役维护的四级质控网络:一级检测采用光谱分析确保材料成分达标;二级过程检测配置在线测量装置实现生产数据实时反馈;三级终检严格执行GB/T 17587标准;四级服役监测通过物联网传感器采集振动频谱数据。检测实验室通过 认证,所有计量器具均溯源至国家时间频率基准,检测报告获得TÜV莱茵等国际机构互认。该体系使丝杠产品平均无故障工作时间延长至18000小时(德国弗劳恩霍夫研究所2024年对比测试数据)。
面向未来,建议从三方面深化发展:一是建立丝杠全参数检测国家标准,统一评价指标体系;二是研发集成量子传感技术的智能检测装备,实现纳米级精度突破;三是构建行业级检测数据云平台,推动检测结果跨企业互认。中国智能制造协会提出,到2028年应形成覆盖80%重点企业的丝杠数字检测网络,为高端装备制造提供更坚实的质量基础。
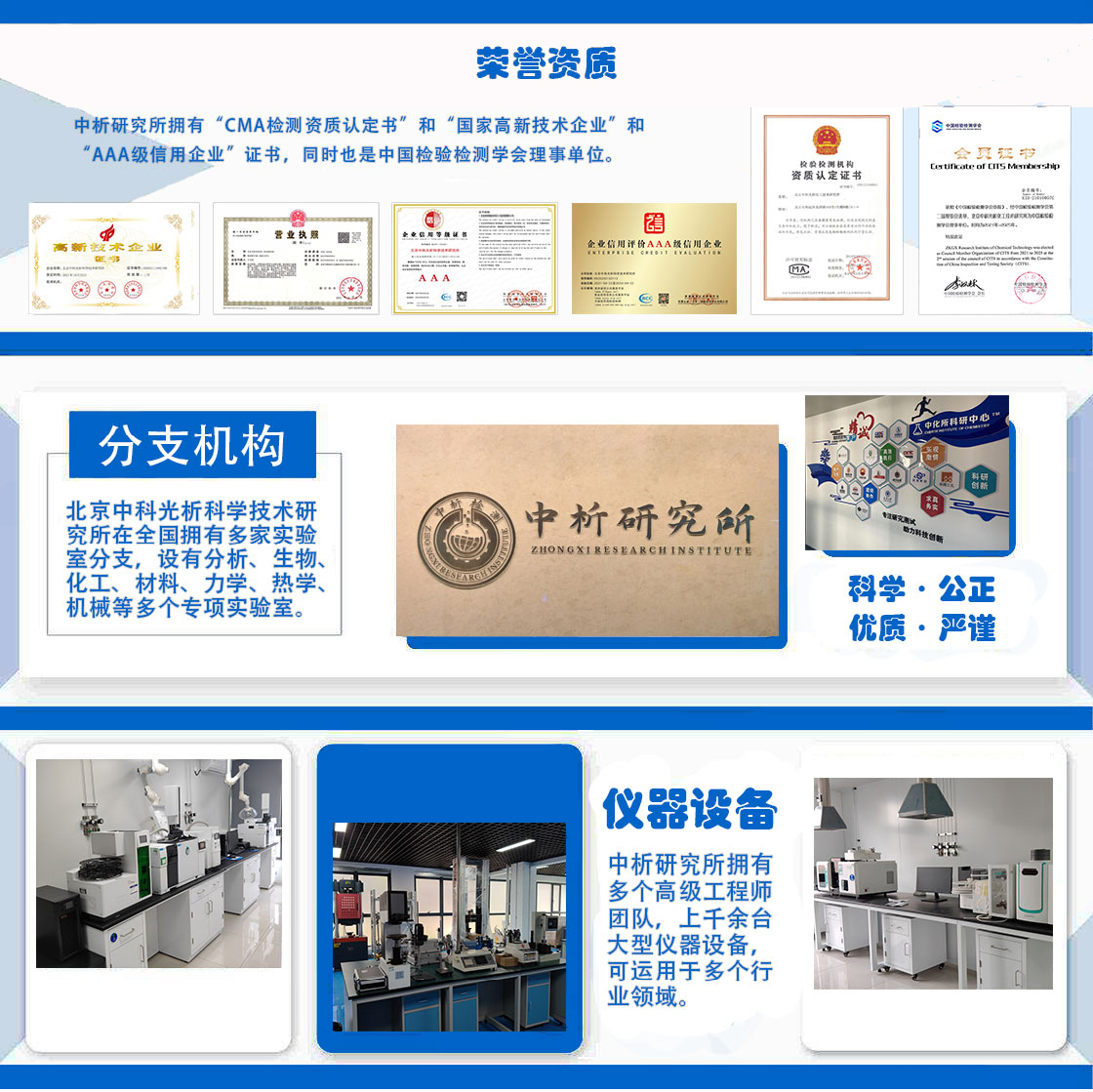
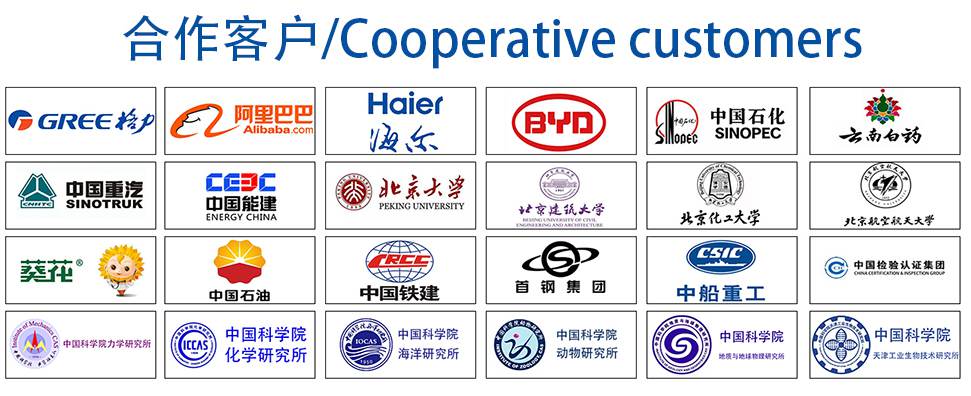