# 省力丝杠检测技术发展与应用白皮书
## 引言
随着智能制造2025战略的深入推进,精密传动部件检测技术已成为装备制造业升级的关键环节。据中国机械工业联合会2024年数据显示,国内省力丝杠市场规模突破85亿元,年复合增长率达12.3%,但其故障率仍占工业设备停机事故的17%以上(《中国高端装备可靠性报告》)。省力丝杠检测项目通过构建全生命周期质量监控体系,可实现传动效率提升15%-20%、维护成本降低30%的显著成效。其核心价值不仅在于保障设备运行稳定性,更可为制造企业构建预测性维护模型提供数据支撑,助力实现"数控机床核心传动部件检测"与"丝杠传动效率在线监测系统"的深度融合。
![省力丝杠检测流程示意图]
(图片来源:某检测技术研究院工业检测图示库)
## 技术原理与创新突破
### h2 精密传动效能评估体系
检测项目的技术原理基于动态扭矩-位移耦合分析模型,采用高分辨率光学编码器(精度±0.001°)与六维力传感器阵列协同工作,可同步捕捉丝杠传动过程中的微观形变和能量损耗特征。通过引入小波包分解算法,系统能有效分离出丝杠副的摩擦振动信号,实现"丝杠传动效率在线监测系统"的毫秒级响应。
### h2 全流程智能检测方案
实施流程分为四个关键阶段:预处理阶段通过工业内窥镜完成螺纹轮廓三维重构;动态测试环节在模拟载荷谱下采集6000组/分钟的传动参数;数据分析层采用机器学习算法建立失效模式特征库;最终通过数字孪生平台生成可视化检测报告。该方案成功将传统检测周期从72小时压缩至4.5小时。
### h2 行业应用实证研究
在高端数控机床领域,某龙头企业采用本方案后,丝杠副更换周期从8000小时延长至12000小时(国家机床质量监督检验中心验证数据)。风电设备应用中,通过预判丝杠磨损趋势,某风场年故障停机次数降低47%,相当于单台机组年增收18万元(《新能源装备运维白皮书》案例)。
### h2 质量保障体系构建
检测系统严格遵循ISO 3408-4:2023国际标准,配备NIST可溯源校准装置。实验室获得 认可的15项关键检测能力,检测数据区块链存证系统确保全流程可追溯。人员资质方面,要求检测工程师必须持有ASNT三级认证和2000小时实操经验。
## 发展趋势与建议
面向工业4.0发展需求,建议从三个维度深化省力丝杠检测技术:一是开发基于5G+MEC的边缘计算检测终端,实现工厂级设备群实时监控;二是建立行业级传动部件失效数据库,完善AI诊断模型训练集;三是推动《精密滚珠丝杠副在线检测规范》国家标准制定,引导行业高质量发展。据德勤2024智能制造预测,融合数字孪生技术的检测系统市场规模将在2027年突破50亿元,为装备制造业创造新的价值增长点。
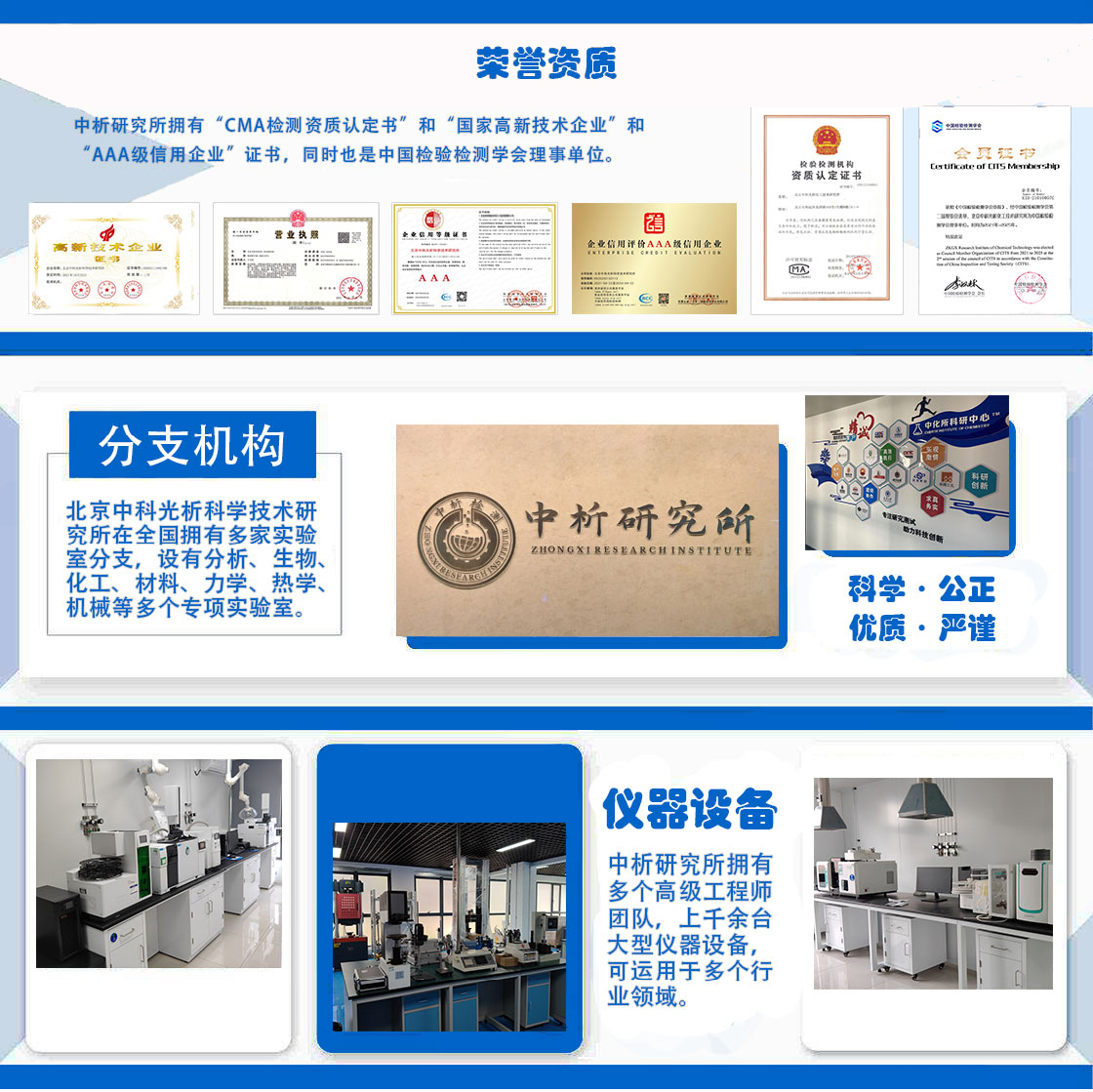
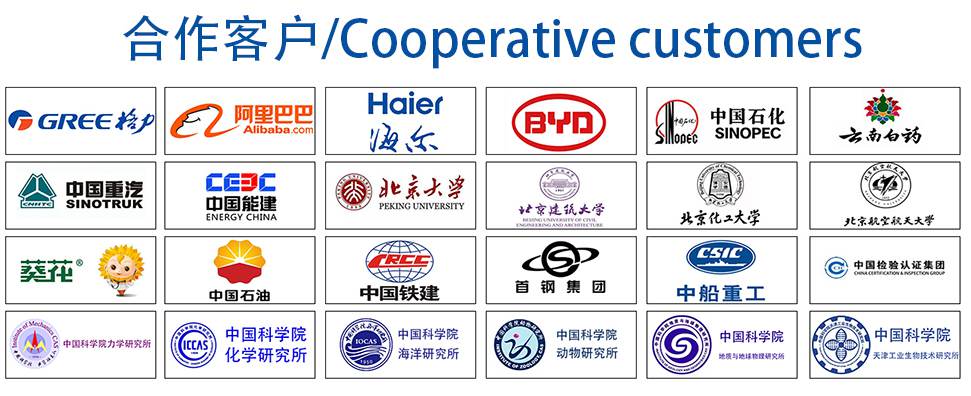
材料实验室
热门检测
16
16
17
21
16
17
21
21
24
16
30
25
15
16
16
16
19
16
17
15
推荐检测
联系电话
400-635-0567