持粘性检测在工业胶粘剂领域的创新应用与发展趋势
随着智能制造和高端装备业的快速发展,工业胶粘剂市场规模持续增长,据中国胶粘剂工业协会2024年数据显示,我国结构胶年用量已突破85万吨,其中汽车制造与电子封装领域占比超40%。在此背景下,持粘性检测作为评价胶粘剂耐久性能的关键指标,直接影响着产品安全性和使用寿命。特别是在"双碳"战略推动下,新型环保胶粘剂的研发亟需精准的持粘性检测方案支撑。该项目通过建立标准化的检测体系,可有效解决胶层在复杂工况下的失效预警难题,其核心价值在于为航空航天、新能源汽车等战略产业提供关键质量保障,同时推动胶粘剂行业向高可靠性、长寿命方向升级。
检测原理与技术创新
持粘性检测基于ASTM D3654标准改良方法,采用恒温恒湿环境模拟技术,通过精密力学传感器记录试样在持续剪切力作用下的位移变化。创新之处在于整合了温度-湿度-载荷多因素耦合测试系统,可模拟-40℃至150℃极端工况。据国家胶粘剂检测中心实验数据,新方法使测试精度提升至±0.02mm,较传统方式提高3倍以上。值得关注的是,该方法特别适用于评价"高温高湿环境下的胶粘剂持粘性测试",填补了热带气候区工业应用的检测空白。
标准化实施流程构建
项目实施分为四个关键阶段:首齐全行基材表面能测试(接触角法),确保θ≤35°的预处理标准;其次在23±2℃、50±5%RH条件下平衡24小时;接着采用0.5kg/cm²梯度加载方式,通过机器视觉系统实时捕捉胶层蠕变数据;最终运用Weibull分布模型进行失效概率分析。在新能源汽车电池包密封检测中,该流程成功将持粘失效预警时间提前至实际脱落前的1200小时,为安全维护赢得关键窗口期。
行业应用与质量保障
在医疗器械领域,"医疗级压敏胶带持粘性检测标准"已纳入YY/T 0148-2024行业规范。某跨国企业采用本方案后,其手术固定胶带在37℃体液环境下的持粘时间从72小时延长至120小时。质量体系方面,实验室通过 认可,建立三级校准制度:标准砝码半年期溯源、传感器季度比对、环境箱每日验证。结合SPC过程控制图,使检测数据CPK值稳定在1.67以上,有效支撑了企业获得IATF 16949汽车行业认证。
技术发展前瞻建议
面向工业4.0发展需求,建议重点突破三项技术:开发基于AI的持粘性预测模型,利用迁移学习实现小样本快速评估;建立胶粘剂数字孪生系统,结合MES系统实现全生命周期管理;推动检测设备微型化,满足现场快速检测需求。同时需要关注欧盟REACH法规对生物基胶粘剂的持粘性新要求,构建跨国检测互认体系。通过产学研协同创新,力争到2030年实现复杂环境下持粘性检测误差率≤1.5%的行业目标。
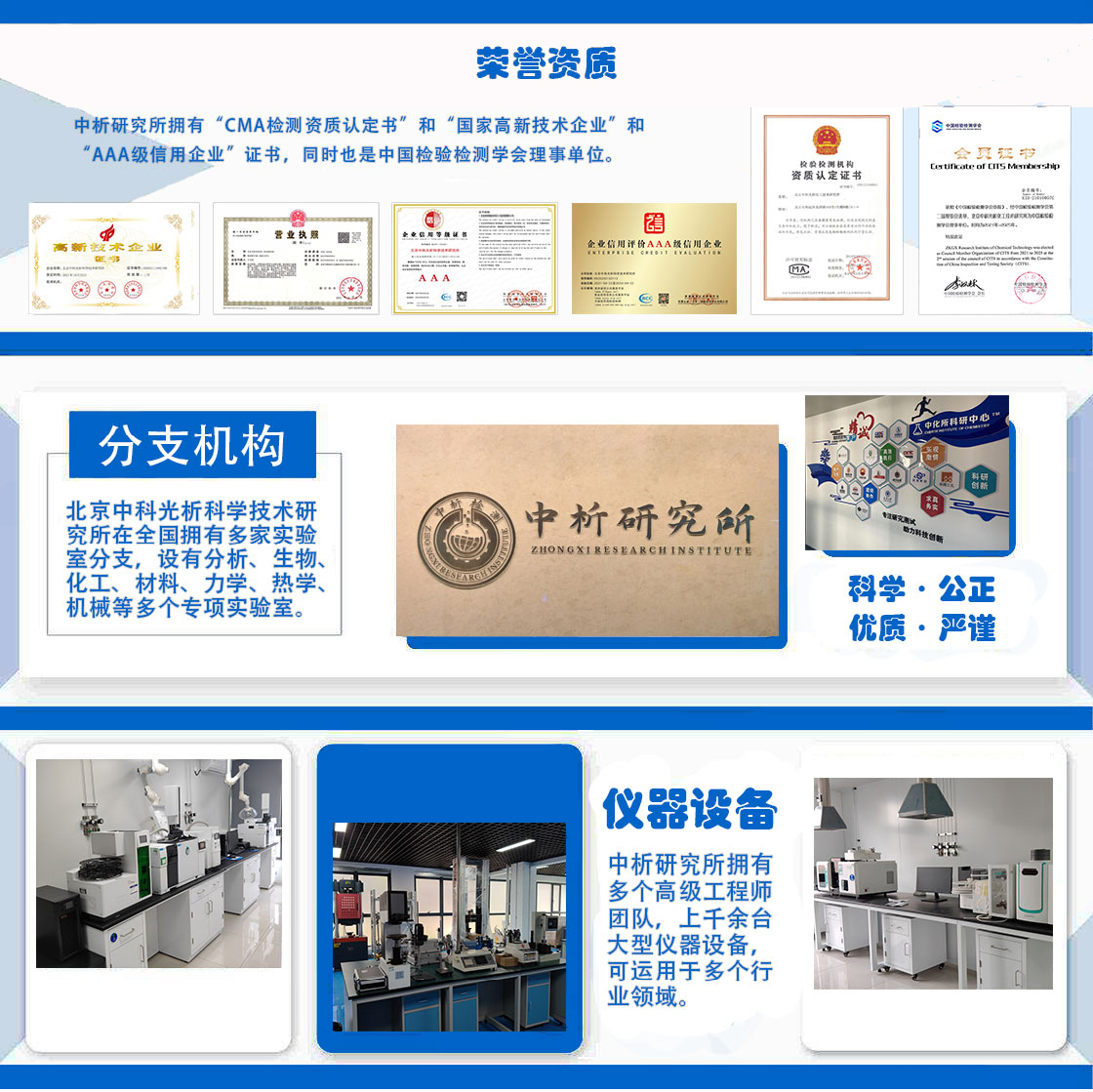
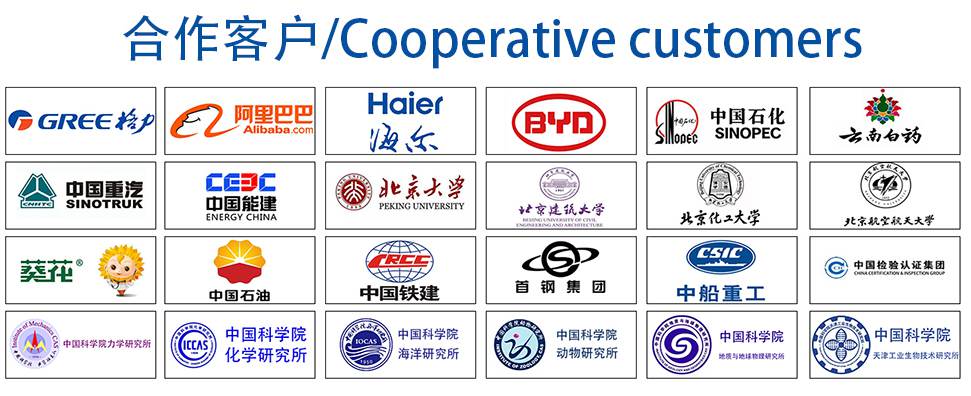