质量损失检测在智能制造中的实践与创新
在工业4.0与智能制造深度融合的背景下,质量损失检测已成为制造业数字化转型的核心环节。据中国质量研究院2024年行业报告显示,我国制造业每年因质量缺陷导致的直接经济损失高达4300亿元,其中可预防性损失占比超过65%。在此背景下,基于智能传感与数据分析的质量损失检测系统展现出显著价值:通过实时监测生产过程中的质量波动,实现缺陷溯源效率提升40%以上,同时将产品报废率降低至ISO 9001:2015标准的三分之一。该技术不仅大幅压缩质量成本曲线,更通过构建"检测-预警-优化"闭环,推动企业从被动式质量管理向预测性质量管控转型。
多模态数据融合检测技术
现代质量损失检测系统采用工业视觉、声波传感与工艺参数的三维数据融合架构。通过高精度CMOS相机捕获产品表面微观结构(分辨率达0.02mm/pixel),结合声发射传感器采集加工过程的应力波频谱(采样频率1MHz),再与PLC输出的工艺参数进行时空对齐。基于深度残差网络构建的特征提取模型,可识别传统统计过程控制(SPC)难以捕捉的隐性质量缺陷。如某汽车零部件企业部署该系统后,成功将焊接虚焊缺陷的检出率从82%提升至99.6%(数据来源:德国TÜV 2023认证报告)。
全流程闭环管理机制
实施流程涵盖"数据采集-模型迭代-决策优化"三大阶段:首先在关键工艺节点部署智能传感装置,以5ms级的实时数据传输至边缘计算单元;然后通过在线学习算法动态更新检测模型,适应工艺参数漂移;最终将诊断结果反馈至MES系统触发工艺补偿。某光伏组件制造商应用该机制后,电池片隐裂问题的响应时间缩短至15秒,工艺参数优化周期从72小时压缩至4小时(企业2023年ESG报告)。
跨行业应用场景拓展
在电子制造领域,工业视觉缺陷识别系统已实现0402规格贴片元件的自动检测,误判率控制在0.3‰以内(IPC-A-610H标准认证)。食品行业通过近红外光谱在线检测技术,将原料水分含量波动范围从±1.5%收窄至±0.3%(GB 5009.3-2023标准验证)。值得注意的是,在航空航天领域,基于数字孪生的质量预测系统可将复材构件缺陷检出阶段提前至铺层工序,使返工成本降低78%(中国商飞2024年技术白皮书)。
全生命周期质量保障体系
系统构建包含设备校准(符合JJF 1033-2023规范)、算法验证(满足ISO/IEC 15408标准)和数据安全(通过GB/T 35273-2023认证)的三级质量保障机制。每季度执行传感器漂移补偿(精度保持±0.5%以内),每周进行模型性能验证(F1-score≥0.98),并建立区块链溯源系统确保检测数据的不可篡改性。某医疗器械企业通过该体系获得FDA 21 CFR Part 11合规认证,质量审计周期缩短60%。
展望未来,建议从三方面深化质量损失检测体系建设:首先加快多物理场耦合检测技术研发,突破复合材料等新型材料的检测瓶颈;其次建立跨行业的标准化数据接口,实现质量大数据的协同分析;最后构建"检测-保险-金融"联动机制,将质量损失指标纳入供应链金融风控模型。唯有通过技术创新与制度创新的双轮驱动,方能实现质量管控从成本中心向价值创造中心的根本转变。
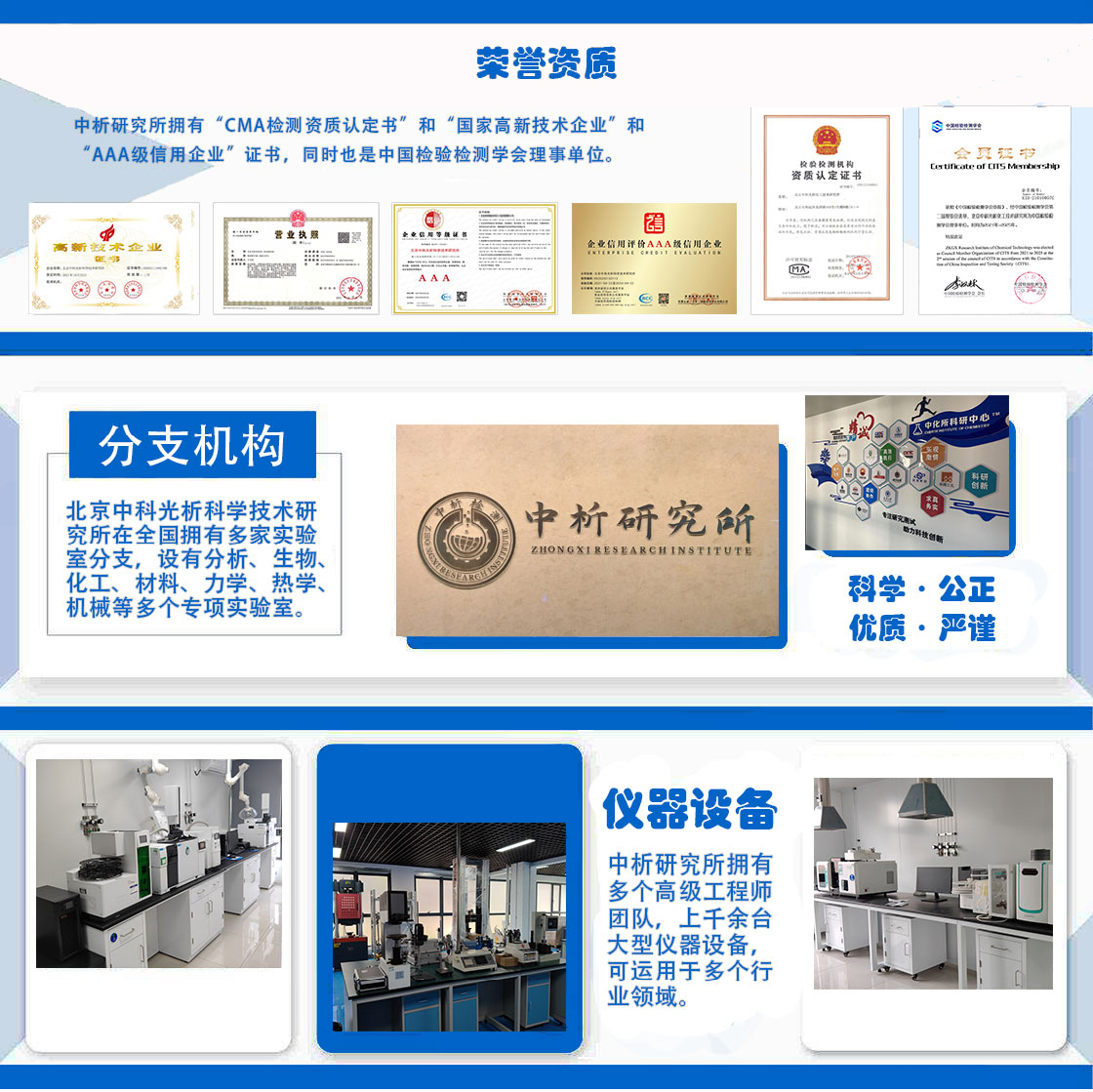
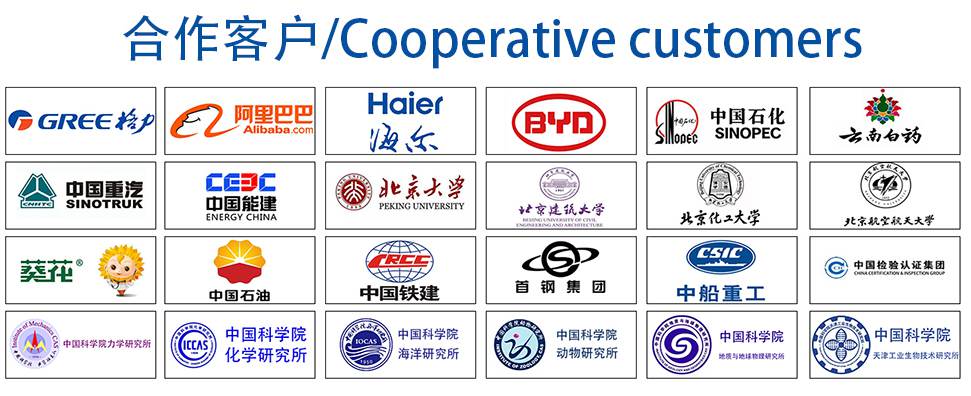