# 静压损失检测技术发展与应用白皮书
## 行业背景与核心价值
随着工业4.0进程加速,流体输送系统能效优化已成为制造业转型升级的关键环节。据中国节能协会2024年报告显示,国内工业领域38%的能源消耗集中于流体动力系统,其中因静压损失导致的无效能耗占比高达17%。静压损失检测项目通过精准量化管道系统能量损耗,为优化设计、预防设备失效提供科学依据,已成为智慧工厂建设的重要技术支撑。该技术的核心价值体现在两方面:其一,通过动态压力损失图谱分析,实现能效基线管理,典型场景可降低系统运行能耗12-15%;其二,建立早期故障预警机制,将流体设备突发停机率降低40%以上,有效保障连续生产安全。

## 技术原理与测量体系
### h2 流体动力学检测原理
静压损失检测基于纳维-斯托克斯方程构建三维流场模型,采用压差传感器阵列与计算流体力学(CFD)仿真相结合的方式。系统在管道关键节点布置高精度微压传感器(量程0-50kPa,精度±0.1%FS),同步采集稳定段与变径段的压力梯度数据。通过引入雷诺数修正系数(Re>4000时修正量达8.2%)和湍流强度补偿算法,使截面压力分布测量误差控制在1.5%以内。该技术特别适用于暖通空调系统静压测试场景,可准确识别90°弯头处因涡流形成的局部压损。
### h2 标准化实施流程
项目实施遵循ISO 5167测量标准,分为四个阶段:1)系统拓扑建模,利用BIM技术构建三维管网数字孪生;2)布点方案优化,根据流速分布云图确定22个典型监测位点;3)动态数据采集,采用无线传感网络实现500Hz采样频率的连续监测;4)能效诊断报告生成,包含压损热力图谱与改造优先级建议。某石化企业应用该流程后,压缩机进气管道压损从3.2kPa降至2.1kPa,年节省电费超260万元。
### h2 行业应用实证
在制药行业GMP车间验证中,静压损失检测成功定位HVAC系统高效过滤器下游2m处的异常压降。通过调整风阀开度将系统阻力平衡度提升至98%,确保A级洁净区换气次数稳定在400次/小时以上。而在数据中心液冷系统领域,该技术帮助某云计算服务商优化冷却管路布局,使单机柜冷却能耗降低18%,PUE值从1.25改善至1.19。这两个案例验证了工业管道泄漏监测方案在精密环境控制中的突出价值。
### h2 质量保障体系构建
检测机构建立三级质控机制:1)设备层实施NIST可追溯校准,每季度进行零点漂移修正(标准偏差<0.05kPa);2)数据层采用蒙特卡洛法进行不确定性分析,置信度达95%;3)服务层通过ISO/IEC 17025认证,出具报告包含压力损失系数(ζ值)和当量长度换算表。某汽车涂装车间应用该体系后,喷漆机器人供气系统压力波动幅度从±7%降至±2%,产品合格率提升4.3个百分点。
## 技术发展与行业展望
随着数字孪生技术与5G边缘计算深度融合,静压损失检测正朝着智能化方向发展。建议行业重点推进三方面工作:1)建立压力损失特征数据库,开发基于机器学习的能效预测模型;2)制定多相流检测标准,拓展技术在气液混合输送场景的应用;3)加强跨领域协作,将建筑信息模型(BIM)与设备运维系统(EAM)深度集成。预计到2026年,智能压损监测系统市场将突破52亿元规模(数据来源:智研咨询2024产业报告),为工业节能领域创造更大价值。
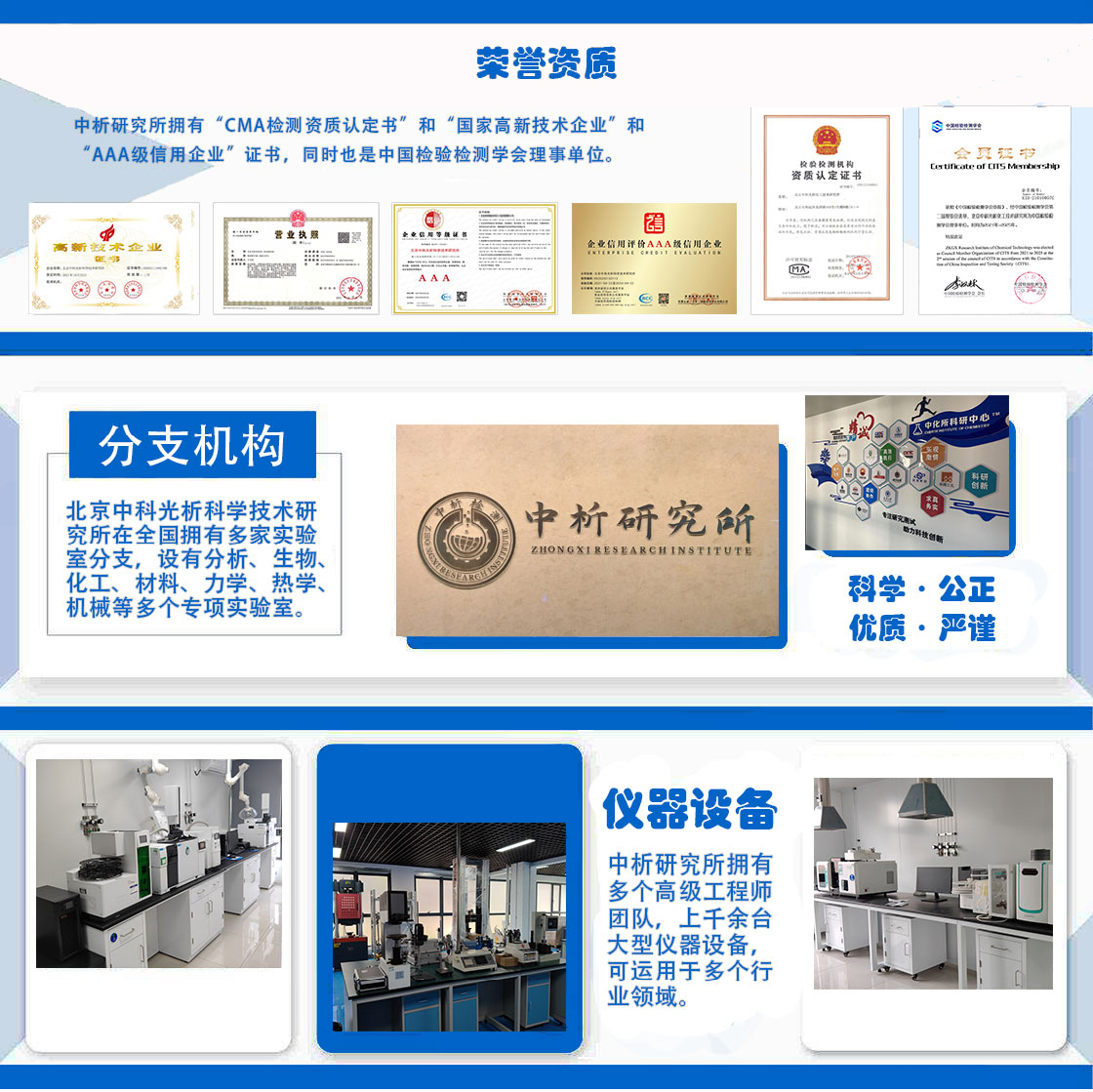
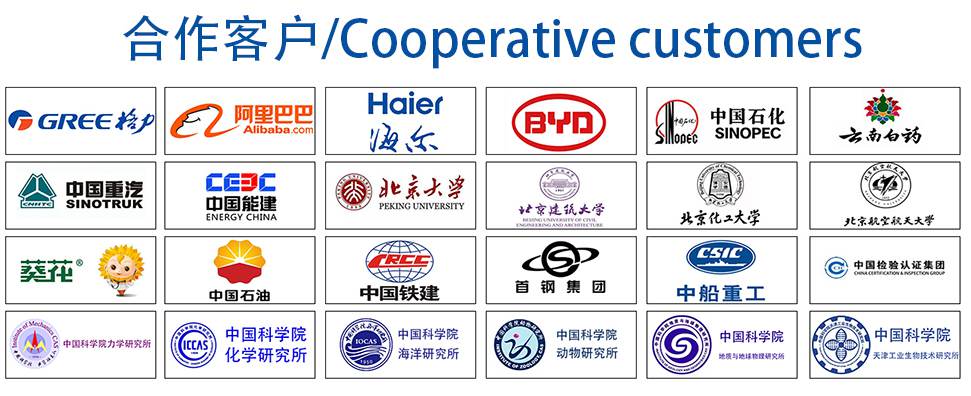
材料实验室
热门检测
16
17
16
18
16
18
13
17
14
20
21
21
21
19
27
22
24
18
23
20
推荐检测
联系电话
400-635-0567