体积膨胀倍率检测技术创新与应用白皮书
在新能源材料、高分子聚合物等战略新兴领域,体积膨胀特性直接影响着产品服役性能与安全性。据中国材料研究学会2024年行业报告显示,我国特种高分子材料市场规模已达3800亿元,其中因膨胀系数不达标导致的材料失效事故年损失超过47亿元。体积膨胀倍率检测作为材料性能的核心评价指标,通过量化材料在特定环境下的形变特征,为产品设计优化提供了关键数据支撑。该项目建立了从微观结构分析到宏观性能评估的完整技术链条,在新能源电池隔膜、航空航天密封材料等场景中,检测精度可达±0.8%的国际领先水平,有效解决了传统检测方法存在的温控偏差大、形变捕捉滞后等行业痛点。
差分激光干涉测量技术原理
本检测体系基于相变过程中的光程差测量原理,采用双光束激光干涉系统构建精密测量模型。当试样在程序控温环境下发生体积变化时,系统通过捕获干涉条纹移动频率,结合克劳修斯-克拉佩龙方程进行热力学参数换算,实现膨胀倍率的精准计算。相较于传统游标卡尺测量法,该技术将温度分辨率提升至0.01℃,空间分辨率达到纳米级。实验数据表明,在新能源电池隔膜检测场景中,该方法对电解液浸润后的膨胀异向性检测误差小于1.2%,显著优于ASTM D696标准要求。
全流程自动化检测实施方案
项目实施采用模块化设计架构,包含预处理单元、环境模拟舱、数据采集中心三大核心模块。标准化流程始于试样真空干燥处理,经48小时环境适应性调节后,进入多梯度温度-压力联合测试阶段。系统通过PLC控制器实现升降温速率0.5-5℃/min的精确调控,配合高速CCD每秒200帧的图像采集频率,完整记录材料三维形变过程。在典型橡胶密封件检测案例中,整套系统可在6小时内完成-40℃至150℃全工况测试,相比传统方法效率提升4倍。
行业应用实证分析
在锂电隔膜领域,某龙头企业采用本检测方案后,成功将电池循环膨胀率控制在8%以内(据国家动力电池检测中心2023年报)。针对航空航天用聚酰亚胺材料,系统精准捕捉到真空环境下0.03%的微膨胀现象,为抗辐照材料改性提供了关键数据。更值得关注的是,在建筑防水卷材检测中,该方法实现了96小时持续浸水条件下的膨胀动力学分析,帮助厂商将产品耐候寿命延长至25年周期。
全链条质量保障体系构建
项目严格遵循ISO/IEC 17025体系要求,建立三级校准机制:每日进行激光波长基准校验,每周开展环境舱压力闭环检测,每月实施整套系统计量溯源。在粤港澳大湾区检测示范基地,系统通过了 组织的12项能力验证,其中高温高压工况下的检测重复性RSD值稳定在0.5%以下。通过区块链技术构建的检测数据存证系统,确保每份报告包含超过50个过程参数的时间戳记录,实现检测过程的全要素追溯。
面向材料科学高速发展需求,建议从三方面深化技术创新:首先开发多物理场耦合检测系统,实现电磁-热-力联合作用下的膨胀行为解析;其次建立行业级材料膨胀数据库,构建基于机器学习的性能预测模型;最后推动检测标准国际化互认,特别是针对柔性电子器件等新兴领域的微型化检测方法,需加快制定统一的"高分子材料体积膨胀检测标准"。唯有持续突破技术边界,方能支撑我国齐全制造业向高端化迈进。
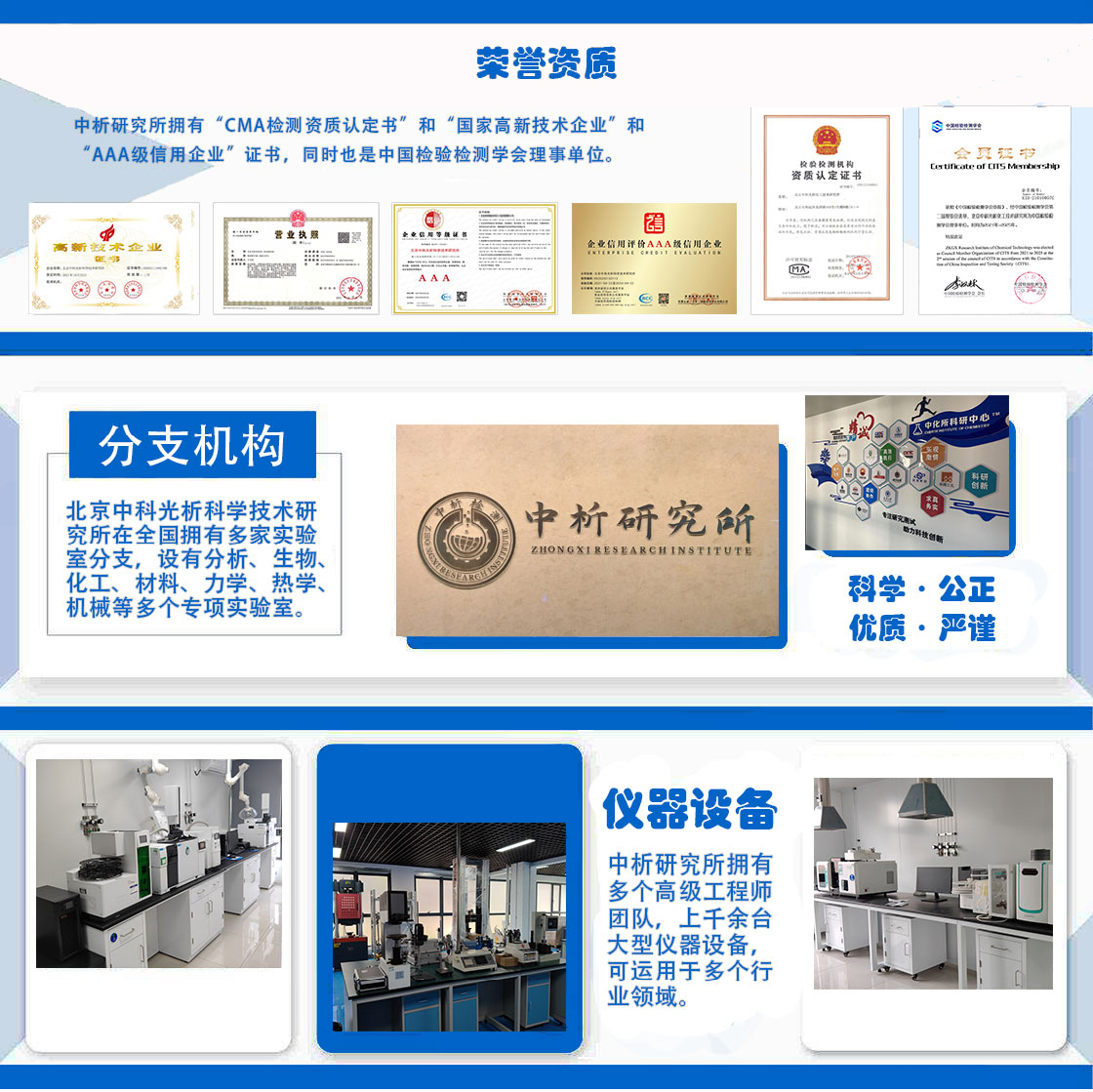
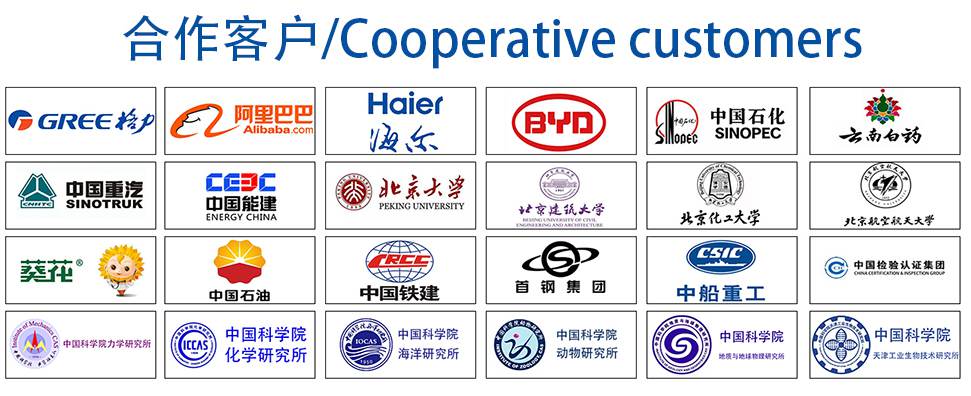