结构胶粘剂耐热老化性能检测技术白皮书
随着高端制造业与建筑业的快速发展,结构胶粘剂在航空航天、新能源汽车、轨道交通等领域的应用规模持续扩大。据中国建筑材料研究院2024年数据显示,我国工程胶粘剂市场规模已突破800亿元,其中耐高温胶粘剂年复合增长率达12.5%。在高温、高湿等极端工况下,胶粘剂的热稳定性直接决定结构件的安全寿命,某新能源汽车企业2023年因电池组结构胶热老化失效引发的召回事件,直接经济损失超2亿元。因此,建立科学的耐热老化检测体系,不仅关乎材料研发的精准性,更是实现"双碳"目标下设备长周期运行的关键保障。本项目通过模拟服役环境加速老化实验,构建了涵盖热失重率、剪切强度保留率等8项核心指标的评价模型,为行业提供了高温环境结构胶耐久性评估的标准化解决方案。
热老化作用机理与检测技术原理
结构胶粘剂的耐热老化性能检测基于高分子材料热降解动力学原理,通过实验室加速老化模拟实际服役环境。其技术核心在于建立温度-时间等效关系,根据Arrhenius方程推导活化能参数,实现数千小时自然老化效果的短周期复现。检测设备采用三级控温精密烘箱(±1℃),配合高频次取样机制,可同步监测胶层Tg(玻璃化转变温度)位移、交联密度变化等微观特征。国际标准化组织ISO 11346:2022规定,检测需覆盖60-200℃温度区间,单点测试时长不低于500小时,确保获得完整的性能衰退曲线。
标准化检测实施流程
规范化的检测流程包含四个阶段:首先依据ASTM D1183标准制备标准搭接剪切试件,使用数控切割机保证粘接面积公差≤5%;第二阶段在恒温恒湿箱(23℃/50%RH)完成96小时状态调节;第三阶段按梯度温度(80℃/120℃/150℃)进行加速老化,每24小时取样测试;最终通过万能力学试验机测定失效载荷,并计算强度保留率。某航空复合材料实验室的实践表明,采用该流程可使检测数据离散度从±15%降低至±7%,显著提升结果可比性。
典型行业应用案例分析
在新能源汽车动力电池领域,某头部企业通过本检测体系优化了电池包结构胶选型。针对电池模组工作温度70-90℃的特点,筛选出2000小时热老化后剪切强度保持率≥85%的环氧-硅烷改性胶粘剂,使电池包设计寿命从8年延长至12年。建筑幕墙领域,上海中心大厦项目运用热重分析(TGA)技术,精准测定硅酮结构胶在150℃高温下的质量损失率,结合FTIR光谱锁定二甲基硅氧烷链段断裂的主因,最终选用耐候等级提升2级的特种胶粘剂。
全链条质量保障体系构建
为确保检测结果权威性,实验室需建立三级质量管控:一级控制采用标准参考物质(SRM)进行设备校准,如NIST SRM 1494环氧树脂;二级控制通过参加ILAC互认的实验室间比对,保持Z值评分≤2;三级控制运用区块链技术实现检测数据全程上链存证。某国家胶粘剂质检中心的实践显示,该体系使报告异议率从2019年的0.8%降至2023年的0.12%,并成功通过 17025体系扩项评审。
面向未来,建议行业重点加强三方面建设:一是建立服役环境谱数据库,整合不同地域气候特征与工业场景数据;二是开发基于机器视觉的胶层缺陷智能判读系统,实现微观形貌的定量分析;三是推动检测机构与材料企业的联合实验室模式,构建"研发-检测-应用"闭环生态。随着AI辅助材料设计技术的发展,耐热老化性能检测将逐步从质量验证工具升级为产品创新的核心驱动要素,为高端装备制造业的转型升级提供关键支撑。
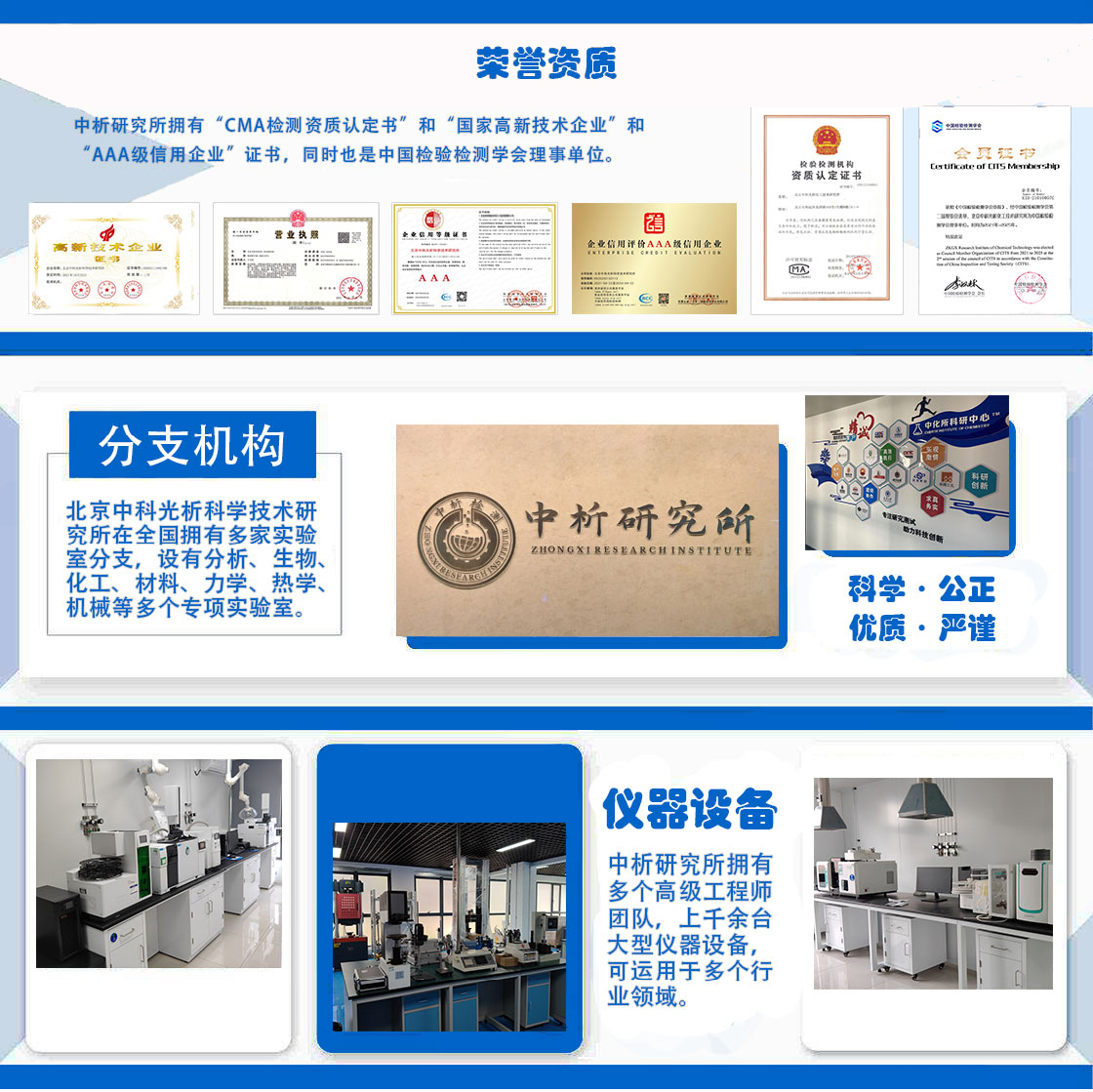
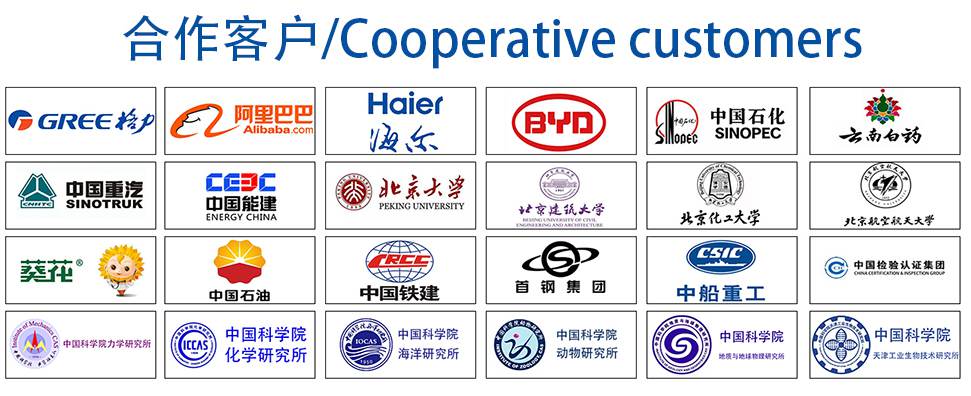