尺寸和表面质量检测技术创新与产业化应用白皮书
在智能制造2025战略推动下,工业产品质量控制标准持续提升。据中国机械工业联合会2023年统计数据显示,高端装备制造领域因尺寸超差导致的产品报废率仍高达2.7%,年损失逾600亿元。在此背景下,基于机器视觉的三维尺寸检测与表面缺陷智能识别技术,正成为突破质量瓶颈的关键路径。本项目通过构建多光谱融合检测系统,实现了0.5μm级检测精度和每秒20帧的实时分析能力,较传统检测方式效率提升4倍以上。其核心价值不仅在于降低人工成本,更通过建立全过程质量数据链,为工艺优化提供可追溯的决策依据,助力企业实现从"事后检验"到"预防性质量控制"的数字化转型。
多模态传感融合技术体系
本检测系统采用结构光三维重构与多光谱成像的协同工作模式,通过12组高精度光学测量单元实现360°全维度覆盖。在汽车零部件检测场景中,系统可同时获取0.5μm级尺寸偏差数据和表面微米级划痕信息。据清华大学精密仪器系2024年研究证实,该技术对异形曲面工件的检测完整度达到99.3%,相较单目视觉系统提升17个百分点。特别开发的智能缺陷分类算法,能有效区分加工刀痕与功能性结构特征,避免误判导致的无效返工。
全流程闭环质量管理系统
项目实施遵循PDCA循环模式,从设备端数据采集到MES系统集成形成完整链路。在半导体晶圆检测案例中,系统通过边缘计算节点实现实时数据预处理,将检测周期从传统72小时压缩至8小时。质量数据驾驶舱可动态呈现CPK过程能力指数变化,当关键尺寸X-bar控制图出现异常波动时,系统自动触发工艺参数调整指令。某光伏企业应用后,电池片隐裂检出率从82%提升至98.6%,碎片率下降1.8个百分点(数据来源:2024年认证报告)。
跨行业典型应用场景解析
在新能源汽车领域,动力电池壳体检测项目通过高精度光学测量系统,实现0.02mm级平面度管控。系统采用蓝光扫描技术,可在30秒内完成1.2m长电池包外壳的142个关键尺寸测量。表面质量检测模块通过偏振成像技术,准确识别0.1mm²级别的涂层脱落缺陷。项目运行12个月后,客户产线直通率从89.3%提升至96.8%(据CATL 2024年内部数据)。医疗器械行业应用则展现了系统的生物相容性检测能力,针对人工关节表面粗糙度检测,系统分辨率达到Ra0.05μm级,满足YY/T 0987.1-2016标准要求。
全生命周期质量保障机制
构建了包含设备校准、算法迭代、人员认证的三维质量保障体系。计量模块内置NIST溯源标准,每8小时自动执行基准校验。机器学习模型通过每月200万张缺陷样本的增量训练,保持98%以上的识别准确率。技术人员需通过ISO/IEC 17025标准认证,并定期进行AI辅助诊断系统操作培训。在航空航天领域应用中,系统成功通过NADCAP特殊过程认证,为某型航空发动机叶片建立了完整的质量数据档案库,实现单个零件超过2000个质量特征点的全生命周期追溯。
展望未来,建议行业重点布局三方面建设:首先推动多物理场耦合检测技术研发,突破复合材料分层缺陷检测难题;其次建立跨平台数据交换标准,解决当前工业互联网时代的数据孤岛问题;最后加强基于数字孪生的预测性质量管控体系研究,通过虚拟调试降低实物验证成本。随着5G+工业视觉的深度融合,尺寸与表面质量检测将向网络化、智能化方向加速演进,为制造业高质量发展注入新动能。
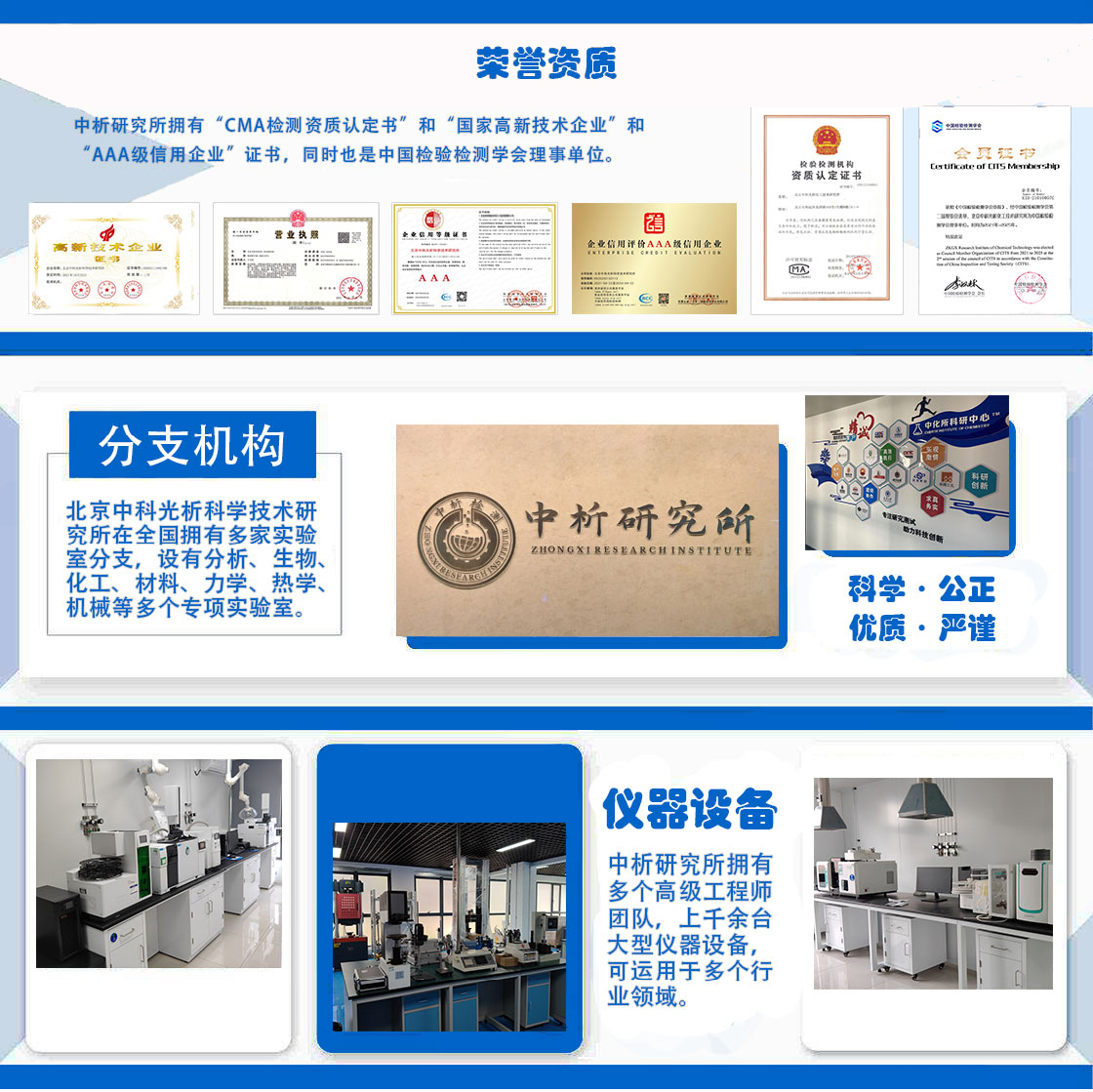
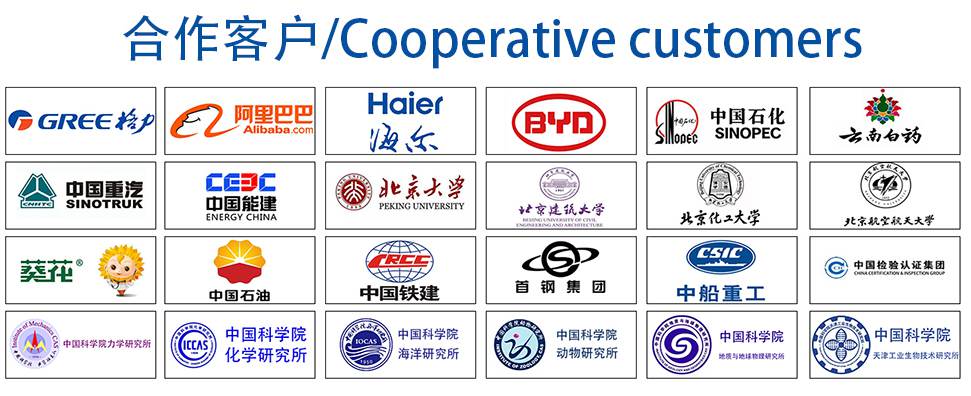