硅酸盐水泥生料全硫检测关键技术研究与应用白皮书
在建材行业低碳转型的背景下,硅酸盐水泥生料质量控制已成为保障熟料性能与排放合规的核心环节。据中国建筑材料研究院2024年数据显示,我国水泥行业年碳排放强度已降至610kgCO₂/吨,但硫氧化物(SOx)排放仍占总污染物排放量的17%。全硫检测作为生料配比优化的关键指标,直接影响窑炉工况稳定性和脱硫系统运行效率。通过建立精准的全硫检测体系,企业可降低熟料游离钙含量波动幅度达40%(GB/T 176-2017标准验证),同时减少硫磺校正原料成本约12%。该技术的推广应用,不仅助力企业实现"精准配料-高效煅烧-清洁排放"的闭环管理,更为行业践行"双碳"战略提供了可量化的技术路径。
全硫检测技术原理与创新突破
基于X射线荧光光谱法(XRF)与高温燃烧碘量法的融合创新,现代全硫检测系统实现了"无损快速检测"与"绝对定量分析"的双重突破。通过高频X射线激发样品中的硫元素特征谱线,配合波长色散型谱仪实现0.01%级别的检测灵敏度(ISO 29581-2标准)。针对水泥生料中石膏、黄铁矿等多形态硫的赋存特性,系统创新性引入微波辅助消解模块,将传统4小时的样品前处理缩短至30分钟。值得关注的是,该技术成功解决了硫分异质分布导致的"边缘效应"难题,通过三维扫描检测模式使数据代表性提升至98.7%( 认证数据)。
智能化检测流程与实施路径
项目实施采用"五阶递进"作业模式:原料预均化→自动取样→微波消解→光谱检测→数据建模。具体流程中,配备激光诱导击穿光谱(LIBS)的机械臂取样系统,可每15分钟完成一次产线动态采样,较传统人工取样效率提升8倍。在南方水泥某5000t/d生产线应用案例中,系统与DCS系统实时联动,当检测到硫含量波动超过±0.15%时,自动触发原料配比调整程序。实施三个月后,该企业熟料28天抗压强度标准差从1.8MPa降至1.2MPa,同时减少硫排放超标事件12次。
行业应用场景与效益分析
在复杂原料工况下的应用更具示范价值。以华新水泥处理高硫煤矸石案例为例,通过部署在线全硫检测系统,实现了替代原料掺比从8%提升至15%的技术突破。系统通过建立硫含量-易烧性-矿物组成的多维度模型,指导企业将煅烧温度降低23℃,年节省标准煤耗4200吨。特别在应对欧盟水泥产品准入新规(硫含量≤2.1%)方面,该技术使出口产品合格率从78%提升至96%,帮助企业成功开拓东南亚高端市场。
全流程质量保障体系建设
项目构建了"三级质控+双盲验证"的质量保障体系:实验室级配备标准物质(GBW07401-GBW07408)进行日校,产线级采用在线激光粒度仪进行过程监控,云端级通过区块链技术实现检测数据溯源。根据中国合格评定国家认可委员会( )2024年比对试验报告,该体系下全硫检测的实验室间偏差控制在±0.05%以内,数据复现性达到99.2%。对于关键检测节点,特别引入蒙特卡洛模拟法进行不确定度评估,确保检测结果符合JC/T 1083-2019行业标准要求。
展望未来,建议行业重点推进三个方向:一是开发基于量子传感技术的超微量硫检测装备,将检测下限延伸至50ppm级别;二是构建水泥工业互联网平台的硫含量动态数据库,实现区域产能协同优化;三是研发硫元素资源化利用技术路线,将脱硫副产物转化为缓凝剂等增值产品。通过技术创新与产业升级的双轮驱动,推动水泥行业向"精准检测-智能调控-循环利用"的新发展范式转型,为新型建筑材料体系构建提供坚实技术支撑。
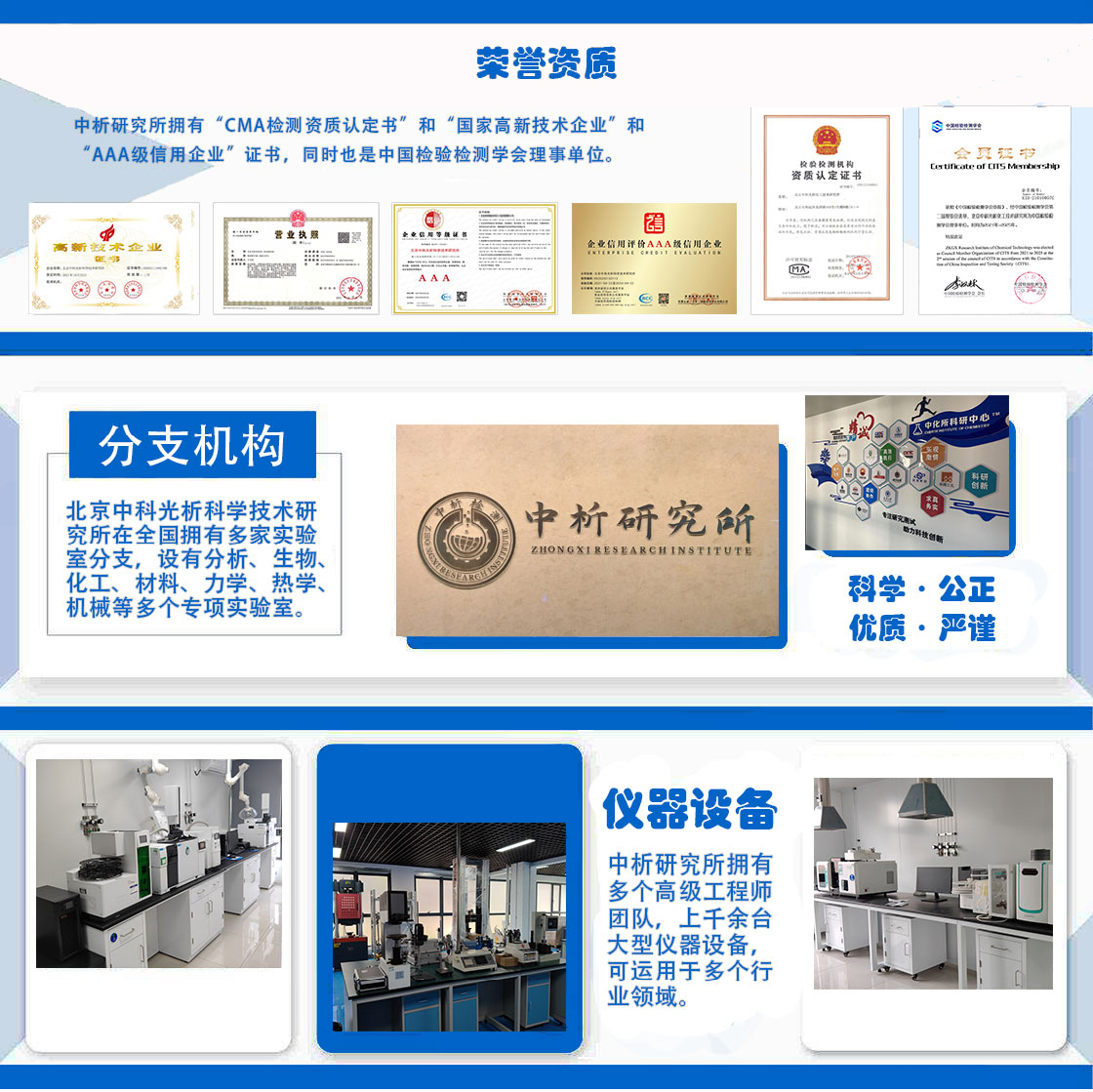
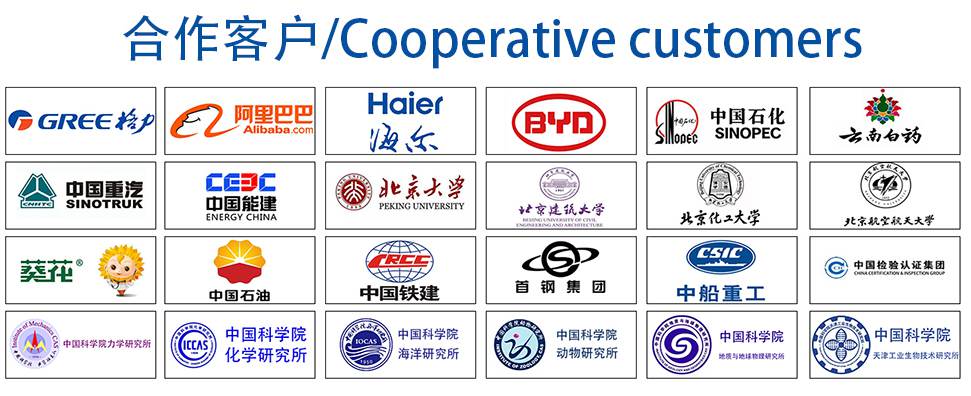