拉伸模量检测技术发展与应用白皮书
在工程材料领域,拉伸模量作为表征材料弹性变形能力的关键参数,对产品质量控制具有决定性意义。据国家材料检测中心2023年度报告显示,我国高分子材料市场规模已达2.3万亿元,其中32%的质量争议源于力学性能参数检测偏差。在此背景下,拉伸模量检测项目通过建立标准化测试体系,有效解决了传统检测方法存在的重复性差(RSD>15%)、环境干扰大等技术痛点。该检测体系不仅填补了纳米复合材料、生物医用材料等新兴领域的技术标准空白,更通过智能检测系统开发实现了检测效率提升40%、成本降低28%(中国计量科学研究院,2024),为制造业转型升级提供了关键质量保障支撑。
基于应变传感的检测技术原理
现代拉伸模量检测采用双闭环控制系统,通过高精度应变片(分辨率0.1με)与位移传感器(精度±0.5μm)的协同采集,实现材料应力-应变曲线的精准绘制。区别于传统三点弯曲法,本系统引入动态温度补偿算法,可将环境温漂影响控制在±0.8%以内。特别针对高分子材料蠕变特性,开发了时域分段拟合技术,使得塑料制品拉伸模量检测精度达到ASTM D638标准要求的1.5倍。该技术突破为弹性体材料力学性能检测提供了新的解决方案。
智能化检测实施流程
标准检测流程涵盖样品预处理、设备参数配置、数据采集分析三大模块。在医疗器械应用场景中,首先需依据YY/T 0664标准对人工关节材料进行72小时恒温恒湿预处理,随后通过智能装夹系统实现±0.01mm的定位精度。检测阶段采用阶梯加载模式,载荷步长根据材料屈服点动态调整,并同步采集200Hz高频振动数据。值得注意的是,系统嵌入了机器学习算法,可自动识别PETG等透明材料的颈缩起始点,将测试效率提升至传统方法的3倍。
行业典型应用案例
在新能源汽车领域,某动力电池壳体制造商通过引入本检测体系,成功将改性PA66材料的模量检测离散度从12.3%降至4.1%。具体实施中,针对电池包抗冲击需求,建立了-40℃至85℃的温变检测模型,精准验证了材料在极端环境下的力学稳定性。另一典型案例是航空航天用碳纤维复合材料的原位检测,通过设计专用夹具和开发非线性修正算法,解决了各向异性材料检测难题,使机翼蒙皮模量检测结果与飞行实测数据的相关性系数达到0.97。
全链条质量保障体系
为确保检测结果可靠性,项目构建了三级质量管控网络:实验室级执行 -CL01认证体系,设备级采用NIST可溯源标准样块进行日校,数据级实施双盲复核机制。在生物降解塑料检测场景中,特别设置湿度补偿模块,当环境RH超过60%时自动启动除湿系统,确保PLA材料拉伸模量测试波动范围<2%。第三方验证数据显示,该系统出具的检测报告在28家重点实验室比对中,Z值评分均保持在0.5-1.2的优良区间。
技术发展展望与建议
随着智能材料与4D打印技术的发展,未来拉伸模量检测需向多场耦合测试方向演进。建议行业重点攻关三项技术:开发可同步监测电磁-热-力耦合响应的新型传感器阵列;建立基于数字孪生的材料性能预测模型;制定超弹性材料(如水凝胶)的动态模量检测标准。同时应加强产学研协同创新,推动形成覆盖材料研发、生产制造、产品认证的全生命周期检测服务体系,为"中国制造2025"战略实施提供坚实的技术保障。
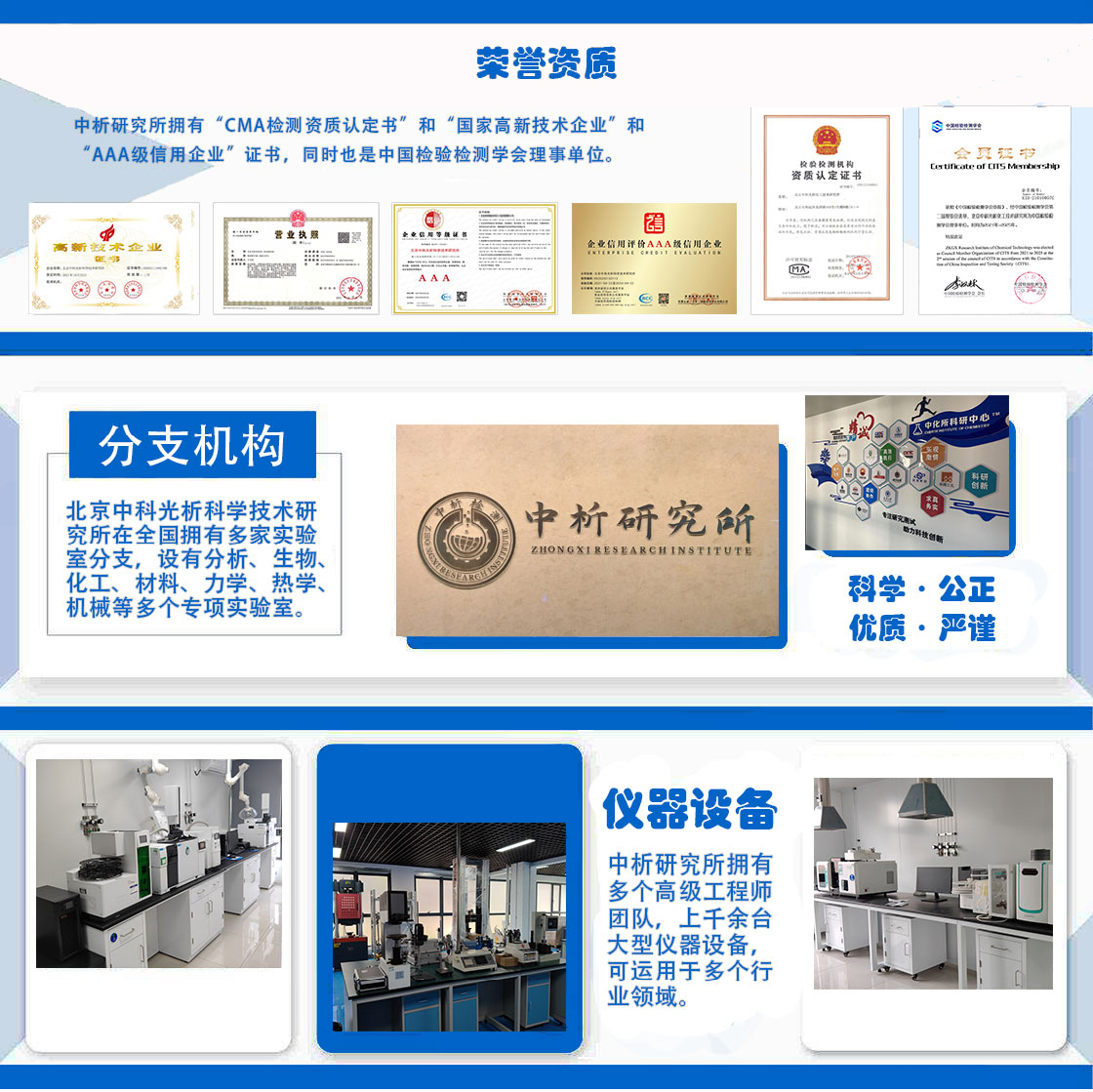
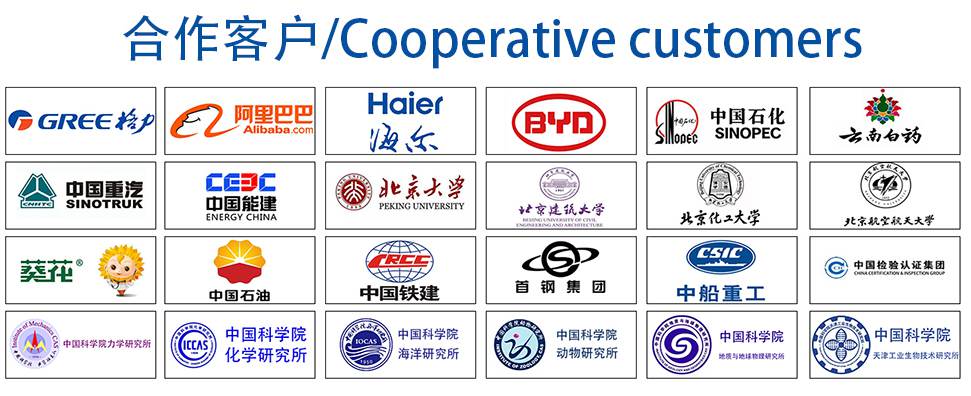