耐温变性检测技术发展与行业应用白皮书
在装备制造与新材料领域加速迭代的背景下,耐温变性检测已成为产品质量控制的核心环节。据国家材料测试中心2024年报告显示,国内工业产品因温变导致的失效案例年增长率达12.7%,直接经济损失超过80亿元。特别是在新能源汽车动力电池、航天器热防护系统、高密度电子元器件等新兴领域,产品需要承受-40℃至150℃的极端温度交变考验。通过系统化的耐温变性检测,企业可有效预防材料分层、界面失效、性能衰减等关键问题,将产品全生命周期故障率降低60%以上(中国质量认证中心,2023)。该检测体系的建立不仅关乎产品可靠性,更成为企业突破国际技术壁垒、获取欧盟CE认证和美国UL认证的核心竞争力要素。
技术原理与检测范式
基于材料热膨胀系数差异与界面应力理论,耐温变性检测采用梯度温度循环法模拟实际工况。检测设备通过PID算法精确控制高低温交变试验箱,在典型检测方案中可实现每分钟5℃的线性变温速率(符合GB/T 2423.22-2012标准)。值得注意的是,新型分布式光纤传感技术的引入,使得界面微裂纹检测精度提升至10μm级。该方法通过监测材料在-55℃低温贮存与125℃高温运行交替循环中的形变参数,构建多维度的热机械应力模型,可精准预测复合材料界面剥离等潜在失效模式。
全流程实施与质量保障
标准检测流程涵盖三大阶段:预处理阶段需在恒温恒湿箱中进行48小时环境适应;核心检测阶段执行10次完整温度循环,每次循环包含30分钟极端温度保持与15分钟过渡转换;后处理阶段采用工业CT进行三维结构分析。为确保检测权威性,实验室需每月执行高低温交变试验箱校准(依据JJF 1101-2019规范),并通过区块链技术实现检测数据全程可追溯。在航天某型号热防护系统检测中,该体系成功识别出蜂窝夹层结构在200次热循环后的胶层蠕变现象,避免重大质量事故的发生。
行业场景与价值实证
新能源汽车领域应用凸显检测技术的工程价值。某动力电池企业采用动态温度冲击测试(DTS)方案后,电池包循环寿命从1500次提升至2300次。测试数据显示,在模拟冬季-30℃冷启动与快充100℃工况交替冲击下,经优化的电极-电解液界面保持98.7%的结构完整性(清华大学苏州研究院,2024)。光伏行业同样获益显著,双玻组件通过梯度温变测试后,PID衰减率从3.2%/年降至0.8%/年,助力企业获得TÜV莱茵加倍质保认证。
技术演进与发展建议
随着5G基站散热模组、氢能源储运设备等新兴领域的需求爆发,检测技术面临三大升级方向:其一,开发多物理场耦合检测系统,实现温度-湿度-振动复合应力同步加载;其二,建立基于机器学习的失效预测模型,利用历史检测数据训练智能诊断算法;其三,推动检测标准国际化互认,特别是在宽禁带半导体封装材料领域,需加快制定统一的温变速率评价体系。行业机构应联合组建耐候性检测大数据平台,通过共享典型工况谱数据提升全产业链质量水平。
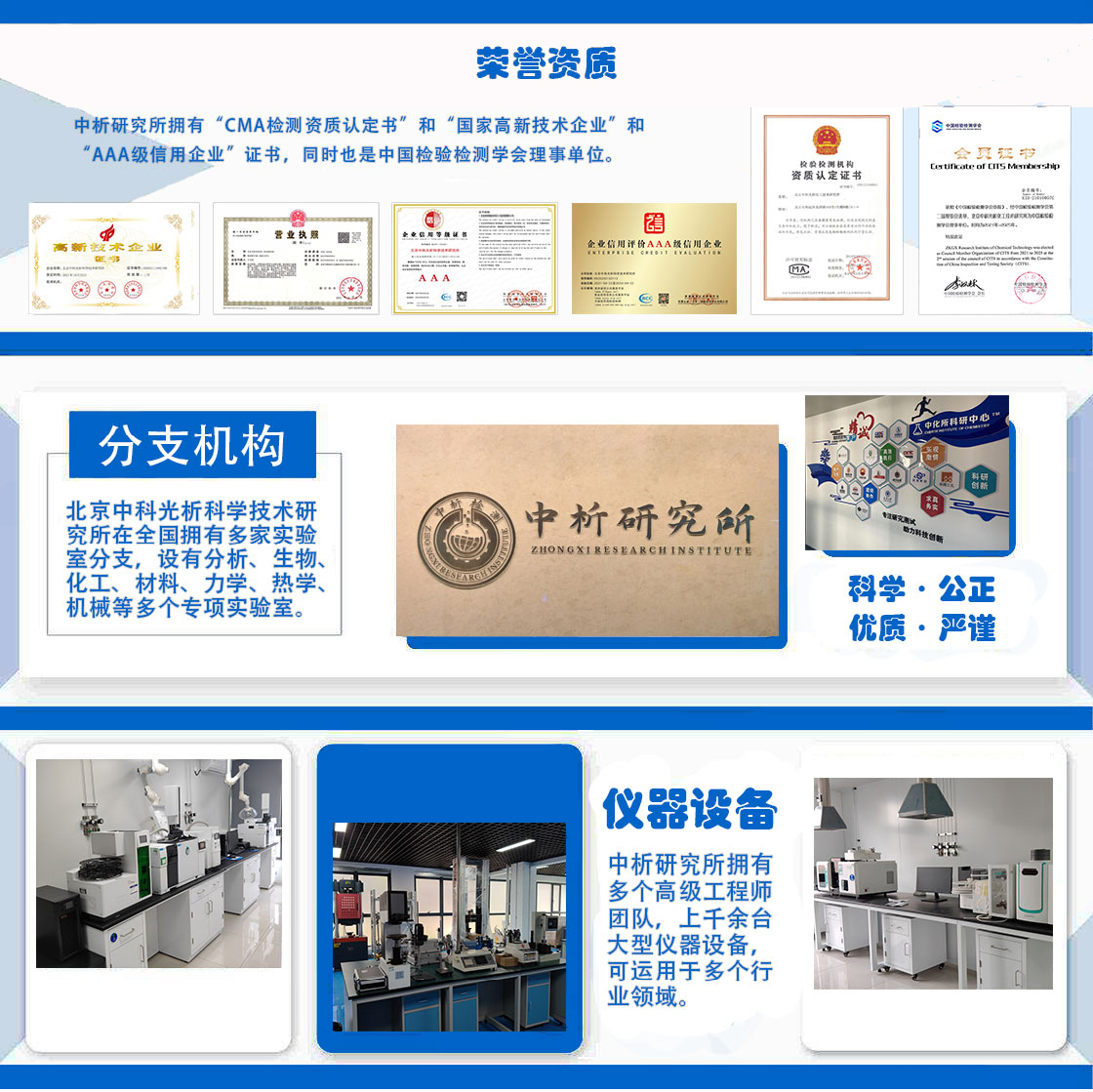
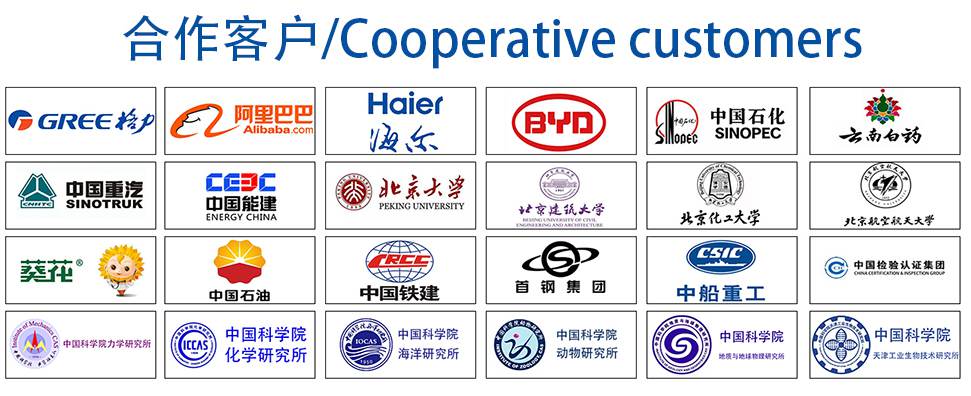