# 减胶率检测在橡胶工业中的创新应用与技术实践
## 行业背景与项目价值
随着"双碳"战略深入推进,橡胶工业面临原材料成本上涨与环保法规升级的双重压力。据中国橡胶工业协会2024年数据显示,国内橡胶制品行业年均消耗生胶超850万吨,其中轮胎制造占比达62%,每降低1%的胶料用量可产生约6.8亿元的经济效益。减胶率检测技术通过精确量化胶料使用效率,为企业实现"精密减胶-性能平衡-成本优化"的闭环管理提供数据支撑。该技术的核心价值体现在三个方面:通过分子级配比优化降低原料消耗,运用智能检测系统提升过程控制精度,以及建立全生命周期数据库推动行业绿色转型。当前,该技术已被纳入《重点行业能效提升指南(2024版)》推荐方案,成为橡胶制品企业转型升级的关键技术路径。
## h2 技术原理与创新突破
减胶率检测建立在多维度物性分析体系之上,采用动态热机械分析(DMA)与傅里叶变换红外光谱(FTIR)联用技术。通过建立胶料损耗因子(tanδ)与减胶率的数学模型,可在保持制品动态性能的前提下精准测算减胶空间。某国家级橡胶检测中心的实验数据显示,采用梯度减胶算法后,工程胎面胶的减胶率提升至8.3%而不影响耐磨指数(TWI)。值得注意的是,该技术融合了机器视觉胶料分布监测系统,可实时追踪硫化过程中的胶料流动状态,将传统离线检测升级为全过程动态管控。
## h2 实施流程与质量保障
标准化作业流程包含四个关键阶段:首先基于MES系统收集历史生产数据建立基准模型;其次通过DOE实验设计确定减胶阈值;然后部署在线监测装置实现生产现场数据闭环;最终利用数字孪生技术进行虚拟验证。在质量保障方面,项目组构建了三级验证体系:实验室级参照ASTM D6204标准进行破坏性测试,产线级采用非接触式激光测厚仪实施过程控制,终端产品则依据GB/T 533-2024进行成品验证。某华东地区轮胎厂的实践表明,该体系使异常胶料消耗降低37%,产品一致性达到98.6PPK。
## h2 行业应用与效益分析
在新能源汽车轮胎领域,某头部企业采用减胶率检测技术后,成功将胎侧胶用量从3.2kg/条降至2.9kg/条,同时维持滚动阻力系数在6.5N/kN以下。更值得关注的是,该技术在环保型胶料替代评估中展现独特价值。当某企业尝试用白炭黑替代30%炭黑时,通过减胶率检测模型精准补偿了填料补强差异,使硫化胶的300%定伸应力保持215kg/cm²水平。据不完全统计,2023年全国橡胶行业通过该技术节省生胶21万吨,减少碳排放当量约58万吨,相当于再造3.2万公顷森林。
## h2 智能化升级与标准建设
当前检测体系正向智能化方向演进,某创新实验室开发的AI减胶决策系统,已实现胶料配方自动优化功能。该系统通过机器学习分析10万组历史数据,可在15分钟内生成最优减胶方案,较传统人工计算效率提升40倍。在标准化建设方面,全国橡胶标委会正在制定《橡胶制品减胶率测定方法》国家标准,拟建立涵盖18项关键指标的评估体系。首批试点企业中,采用标准草案的企业产品不良率平均下降1.7个百分点,验证了规范化管理的必要性。
## 发展趋势与战略建议
面向"十四五"后半程,建议行业重点布局三个方向:首先加大纳米填料分散度检测技术的研发投入,突破当前减胶率提升的物理极限;其次建立区域性减胶率检测共享平台,帮助中小企业降低技术应用门槛;最后推动检测设备与工业互联网的深度融合,开发具备自我迭代功能的智能检测终端。政府部门可考虑将减胶率指标纳入绿色工厂评价体系,通过政策引导加速行业整体能效升级,为橡胶工业实现"双碳"目标构筑技术护城河。
上一篇:浸水光照后粘结性检测下一篇:碎石或卵石的表观密度(简易法)检测
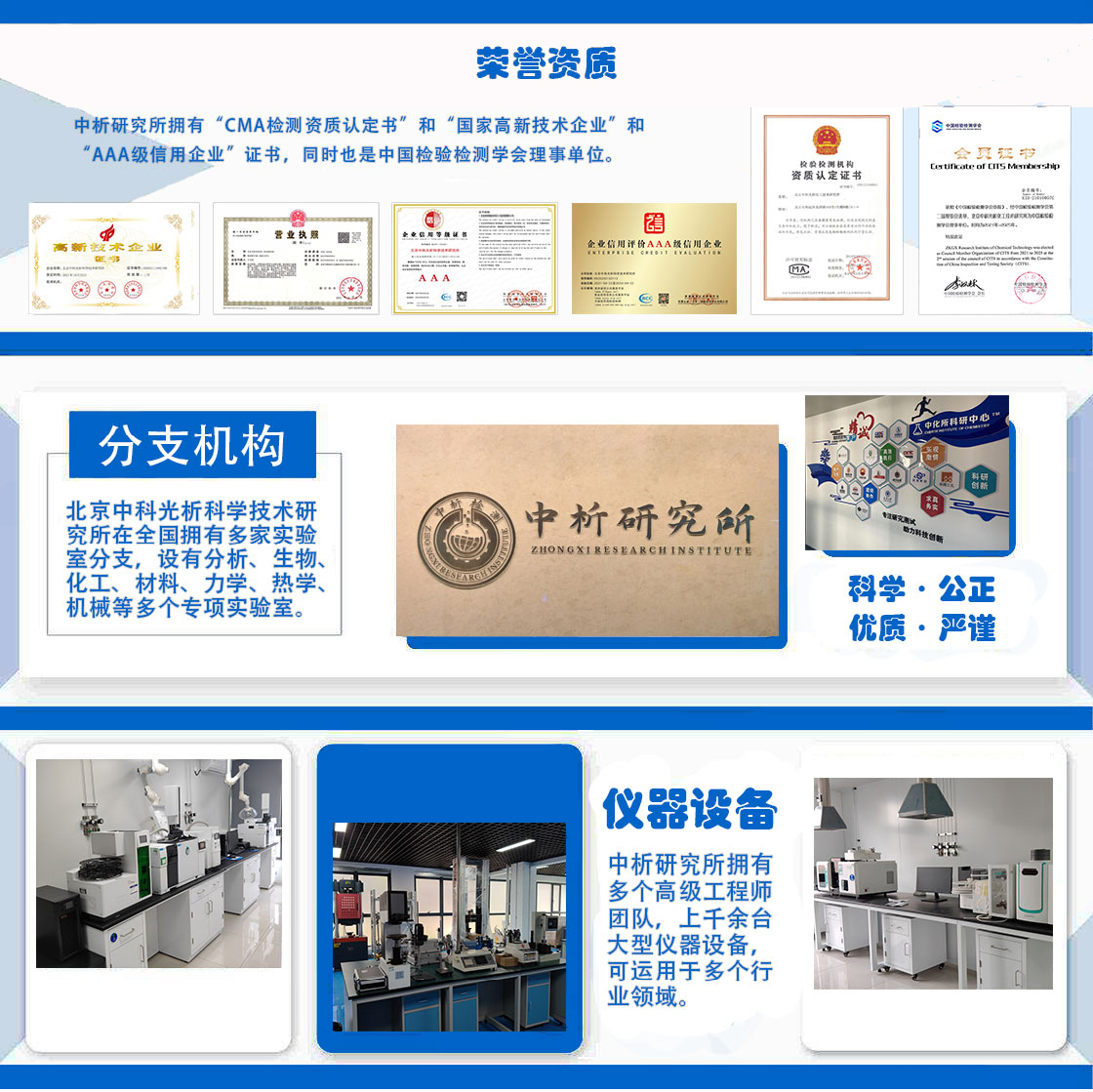
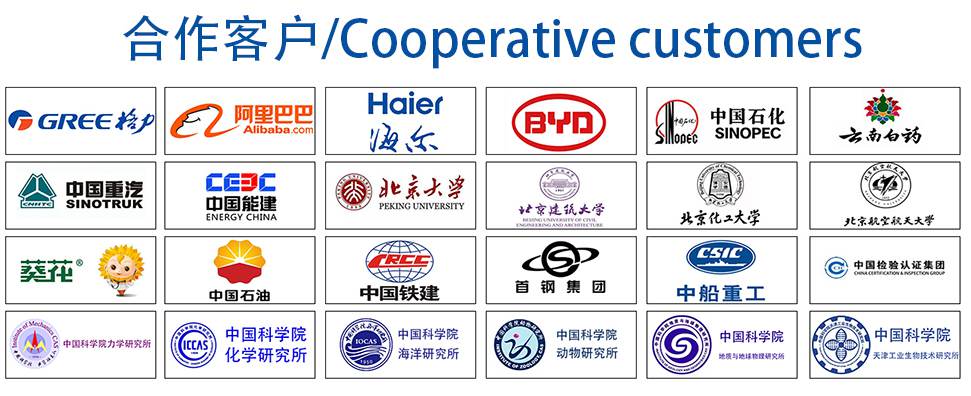
材料实验室
热门检测
251
211
186
201
193
197
205
197
203
210
199
195
192
198
193
189
203
195
204
197
推荐检测
联系电话
400-635-0567