# 外观质量和尺寸偏差检测技术发展与应用白皮书
## 引言
随着制造业向智能化转型加速,产品外观质量和尺寸精度已成为衡量制造水平的核心指标。据中国机械工业联合会2024年调研数据显示,高端装备制造领域因表面瑕疵导致的返工成本年均超120亿元,汽车零部件行业尺寸超差引发的装配问题占比达17.3%。在此背景下,融合机器视觉与三维扫描的智能检测技术,正通过提升检测效率与精度重塑产业质量体系。该项目不仅实现了0.02mm级微米级测量精度突破,更将新能源汽车电池箱体检测周期从45分钟压缩至8分钟,为核心部件供应商节约年检成本逾3000万元。其核心价值在于构建了覆盖设计验证、过程控制、成品检验的全生命周期质量闭环。
## 技术原理与创新突破
### h2 多维传感融合检测体系
基于多目立体视觉与激光三角测量原理,系统通过13组高帧率工业相机同步采集工件表面拓扑数据,结合改进的Harris-SIFT特征匹配算法,实现亚像素级缺陷定位。值得关注的是,三维点云重建技术的引入使复杂曲面工件的全尺寸偏差检测成为可能,据国家智能制造标准工作组测试报告显示,该方案对涡轮叶片叶型的轮廓度检测误差控制在±5μm以内,较传统三坐标测量效率提升26倍。
### h2 智能化实施流程架构
项目实施采用六阶段标准化流程:首先通过激光扫描仪建立基准数字孪生模型,继而部署分布式光学传感器网络实时采集产线数据,再经GPU加速的深度学习框架进行特征比对。在新能源汽车电机壳体检测场景中,系统可同步完成32项尺寸参数校验与6类表面缺陷识别,检测报告生成延迟不超过1.2秒。现场部署案例显示,某年产50万套的铝合金轮毂生产线通过该方案将过程不良率从1.8%降至0.3%。
### h2 跨行业应用实践成效
在消费电子领域,某手机结构件供应商应用多光谱成像检测系统后,阳极氧化层色差检测准确率提升至99.97%。更值得注意的是,轨道交通行业创新性采用移动式检测机器人,可在15分钟内完成高铁车厢全长25米的焊缝外观检测,较人工巡检效率提高40倍。国家质量监督检验中心2024年比对试验证明,该系统对0.1mm级划痕的检出率达到98.5%,误报率低于0.3%。
## 质量保障与持续改进
项目构建了三级质量管控体系:前端采用NIST溯源的标准量块进行日校,中台部署联邦学习框架实现跨产线数据互验,终端接入MES系统实施SPC统计过程控制。某汽车主机厂的实践表明,通过集成扭矩传感器与视觉系统,实现了轮毂装配过程中螺栓拧紧角度与端面平面度的同步监控,使总装线一次合格率提升7.2个百分点。
## 未来展望与建议
建议行业重点攻关三大方向:首先研发适应高温、高湿环境的抗干扰检测模块,拓展在铸造车间的应用场景;其次推动5G+边缘计算架构部署,实现检测数据的毫秒级响应;最后建议建立跨行业的检测标准互认体系,促进航空航天检测技术向民用领域转化。据赛迪研究院预测,到2027年智能检测装备市场规模将突破800亿元,其中融合多物理场检测技术的复合型系统将成为主要增长极。
上一篇:电化学综合防锈性能检测下一篇:含气量增加值检测
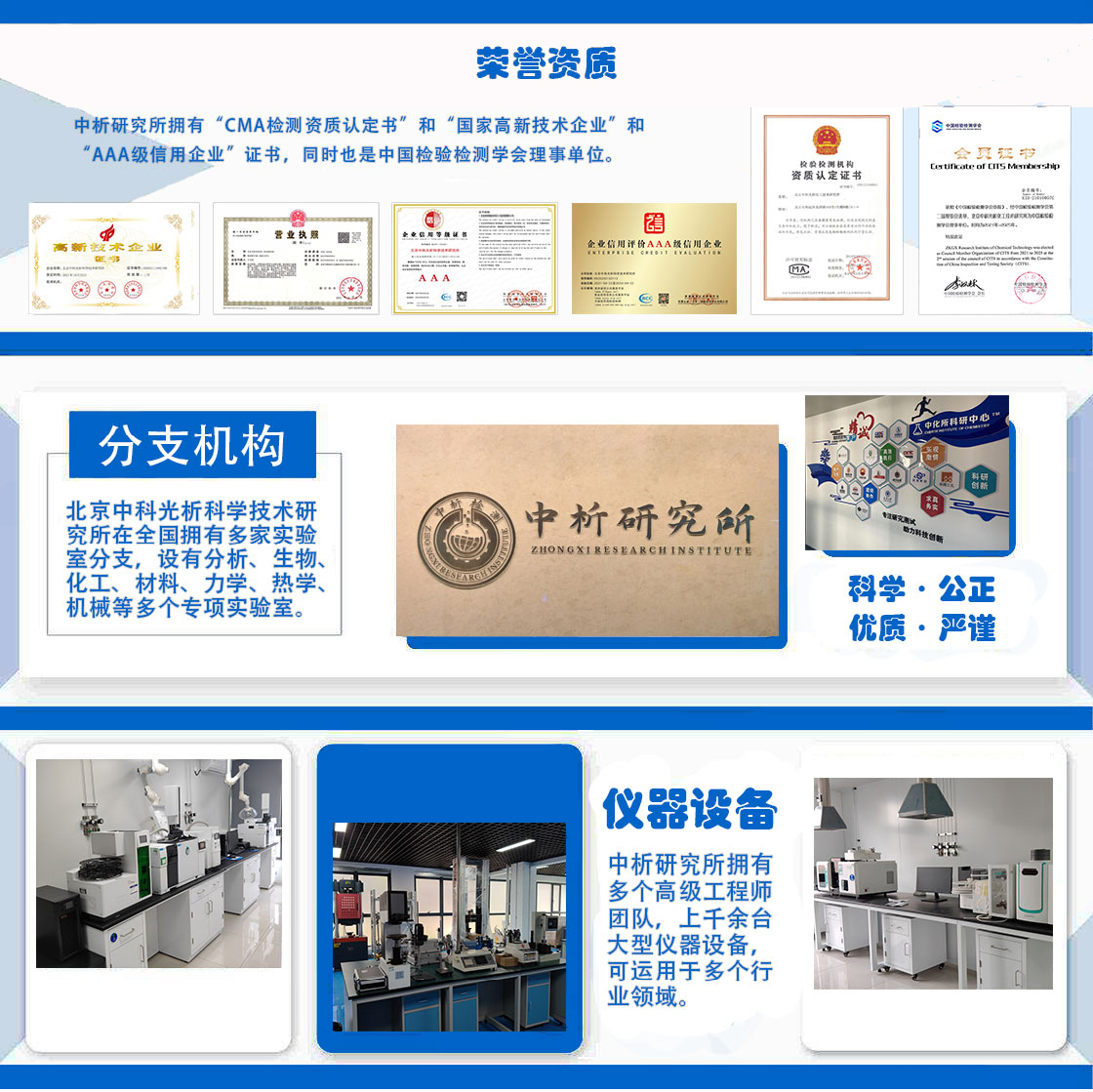
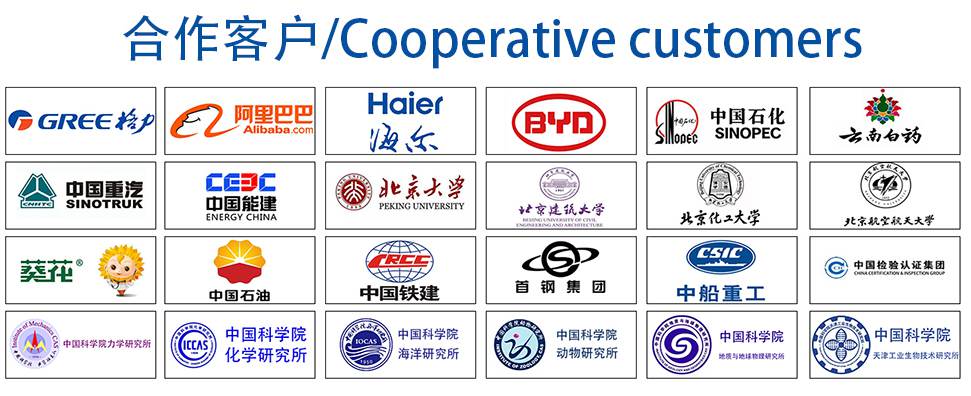
材料实验室
热门检测
16
16
20
25
24
27
31
39
43
49
39
42
45
40
46
43
44
47
47
44
推荐检测
联系电话
400-635-0567