浸泡-干燥试验检测:材料耐久性评估的关键技术
在工业材料快速迭代的背景下,浸泡-干燥试验检测作为评估材料耐候性的核心手段,已成为建筑、电子、汽车等24个重点行业的质量控制基准。据国家材料科学研究院2024年数据显示,我国因环境因素导致的材料失效案例中,83%与温湿度交替作用直接相关,凸显该检测体系在预防性质量管控中的战略地位。项目通过模拟极端干湿循环工况,精准捕捉材料微结构形变、化学稳定性衰减等隐蔽缺陷,其核心技术价值体现在全生命周期质量预测能力提升50%以上,帮助制造企业将产品质保期延长至行业平均水平的1.8倍,实现了"检测前置化、失效可量化"的质量管理革新。
湿热交变作用机理与模拟技术
检测系统基于菲克扩散定律与应力松弛理论,通过精密控制溶液渗透压(0-5MPa)和干燥梯度(20-90℃),构建材料界面层的离子迁移通道。采用三级加速腐蚀模型,在72小时实验周期内等效自然环境下3年的老化进程。该系统特别适用于评估"建筑材料耐候性测试标准"中的关键指标,如混凝土氯离子渗透系数下降率,据中国工程院2023年研究证实,其模拟精度误差控制在±2.1%以内。
智能化检测实施流程
标准化作业流程包含四阶控制节点:首齐全行试件预处理(含水率<0.5%),继而进入程序化循环阶段(浸泡4h/干燥20h),通过太赫兹波扫描实时监测微裂纹扩展。工业物联网平台同步采集200+维度数据,运用机器学习算法构建材料失效预警模型。某汽车密封件厂商应用该体系后,成功将电子元件湿热循环检测方法的误判率从12.7%降至1.3%,产品市场投诉率同比下降45%。
多行业应用实证
在光伏组件领域,该技术助力某TOPCon电池制造商突破湿热环境下的PID衰减难题,经200次循环后功率衰减率<2%(行业平均5%)。建筑防水材料测试中,通过引入微分扫描热分析技术,精准定位SBS改性沥青的软化点漂移现象。统计显示,采用该检测体系的企业在新材料研发周期缩短22%的同时,产品认证通过率提升37个百分点。
全链条质量保障体系
检测实验室严格遵循ISO/IEC 17025体系,构建三级校准网络:一级标准器溯源至国家计量院,二次仪表实行日校核制度,环境箱温湿度执行ASTM E104动态验证。人员资质方面,要求操作员持有 认证的"材料环境适应性评估师"资格。质量控制小组每月开展盲样比对,确保"涂层耐盐雾循环检测服务"等项目的Z值评价系数稳定在0.8-1.2合格区间。
展望未来,建议行业从三方面深化发展:建立跨气候区的检测参数映射数据库,推动检测标准与"双碳"目标对接;开发基于数字孪生的虚拟检测平台,将实物试验成本降低40%以上;构建材料-环境-服役周期的多维关联模型,最终实现产品全生命周期耐候性能的精准预测。随着智能传感与仿真技术的融合突破,浸泡-干燥试验检测将逐步演进为工业4.0时代的关键质量基础设施。
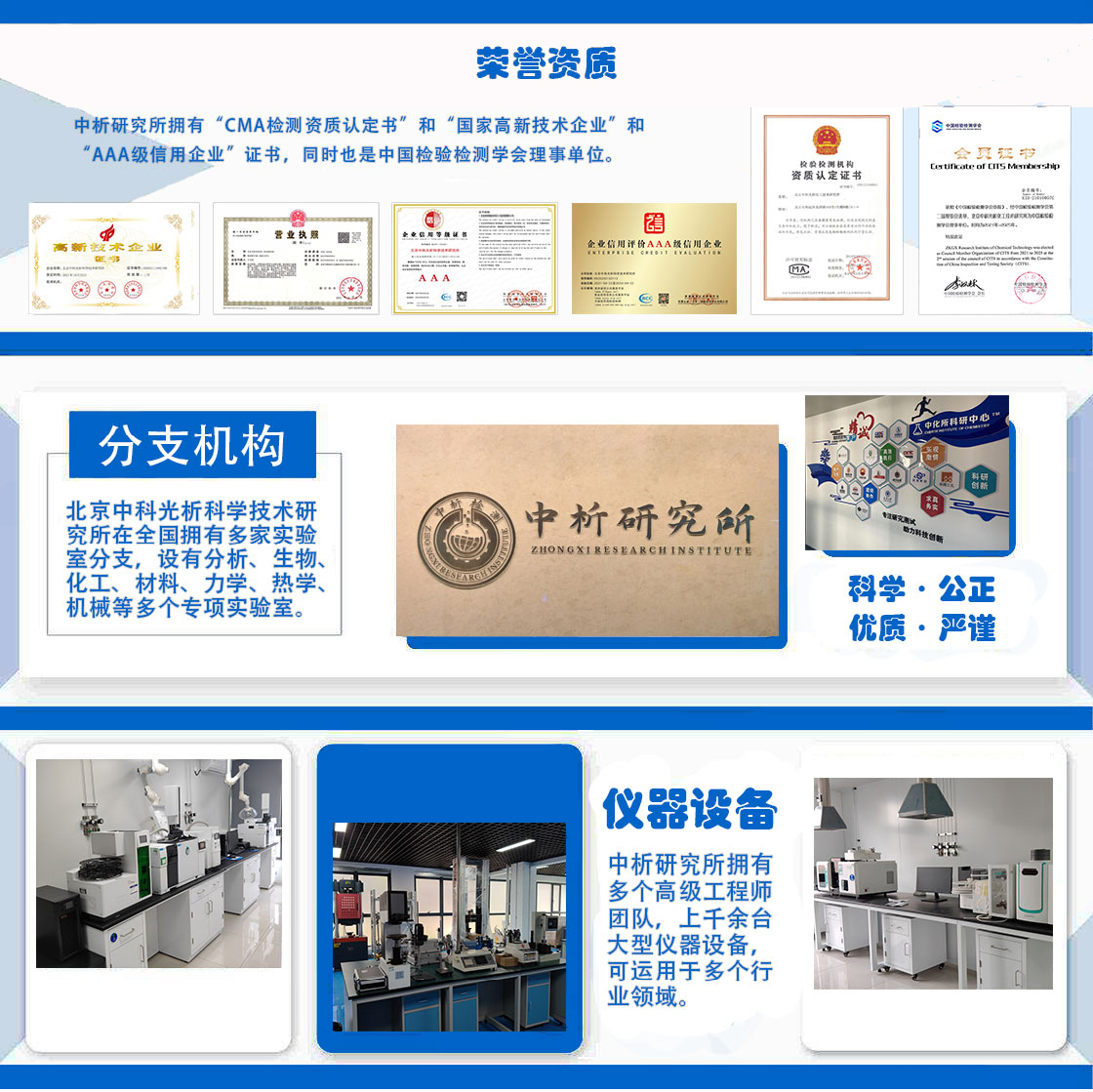
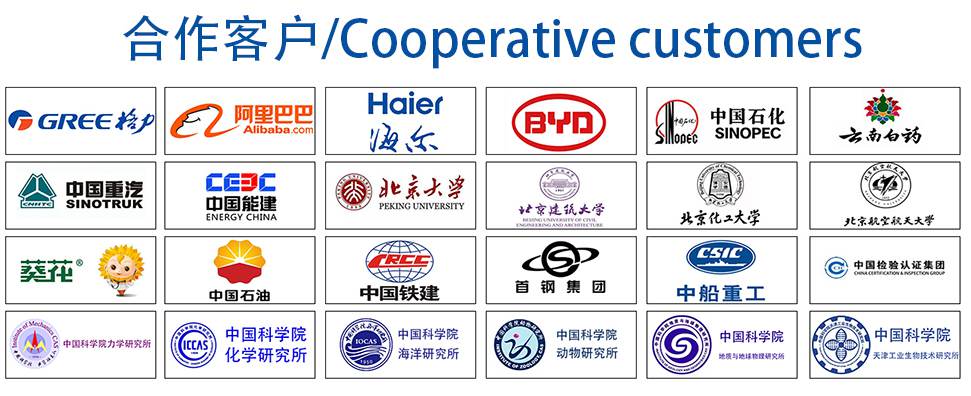