混凝土拌和物凝结时间试验(贯入阻力法)检测
随着我国基础设施建设规模持续扩大,混凝土作为核心建筑材料,其质量控制已成为工程安全的重要环节。据中国建筑材料研究院2024年数据显示,全国每年因混凝土凝结时间异常导致的施工事故占比达12.6%,直接经济损失超20亿元。在此背景下,混凝土拌和物凝结时间试验(贯入阻力法)作为行业标准检测方法,通过量化贯入阻力值精准判定初凝与终凝时间,为配比优化、施工工序衔接提供关键依据。该检测技术的核心价值在于实现施工窗口期的科学把控,既能避免过早振捣引发的结构损伤,又可防止延迟收面导致的表面强度不足,显著提升超高层建筑、大跨度桥梁等复杂工程的耐久性表现。
技术原理与检测标准
贯入阻力法基于水化反应进程中混凝土内部结构强化的物理特性,依据ASTM C403标准建立贯入阻力与凝结时间的数学模型。当标准贯入针在25N·mm²至35N·mm²区间时判定为初凝状态,对应塑性向弹性转变阶段;阻力值达280N·mm²时则标志终凝完成,此时胶凝材料完成主要水化反应。通过高频次采样(每30分钟/次)绘制"S"型阻力曲线,可精准捕捉温度敏感型混凝土的凝结拐点。值得注意的是,该方法特别适用于掺有缓凝剂或早强剂的功能性混凝土检测,能够有效识别外加剂对水化动力学的非线性影响。
标准化实施流程与质控要点
检测流程严格遵循JGJ/T 70规范要求,涵盖样品制备、环境调控、数据采集三大环节。操作人员需在20±2℃恒温条件下,将新拌混凝土装入150mm标准试模并振捣密实,试件表面覆盖塑料薄膜防止水分蒸发。测试阶段采用数显式贯入仪,自拌和后2小时开始,按规范间隔时间垂直贯入25mm深,记录最大阻力值。中国建筑科学研究院2023年比对试验表明,当环境湿度波动超过±5%时,贯入阻力测量误差可达18%,因此实验室需配置双通道温湿度记录仪实现全程监测。针对高流态混凝土,需特别控制贯入速率在0.8-1.2mm/s区间以规避触变效应干扰。
典型工程应用场景分析
在川藏铁路特大桥桩基施工中,项目团队通过贯入阻力法成功解决了高原昼夜温差导致的凝结异常问题。现场实验室建立每小时检测机制,根据实时阻力数据动态调整聚羧酸减水剂掺量,将初凝时间稳定在6±0.5小时区间,既保障了桩基连续浇筑需求,又避免了低温环境下强度发展滞后风险。另据中交集团2024年技术报告显示,该方法在广州白云站TOD项目中实现单日120组检测通量,配合BIM进度管理系统,使大体量混凝土结构的施工缝留设精度提升40%,材料浪费率降低至1.2%以下。
全链条质量保障体系构建
为确保检测结果可靠性,需建立三级质量控制体系:一级控制涵盖设备计量校准,贯入针直径公差须控制在±0.01mm以内;二级控制包括人员操作认证,要求检测员每年完成 认可的比对试验;三级控制涉及数据异常追溯机制,采用区块链技术实现原始记录不可篡改存储。国家建筑工程质量监督检验中心2022年能力验证结果显示,实施该体系的实验室数据离散系数由8.7%降至2.3%,显著优于行业平均水平。特别在核电工程等特殊领域,还需增加γ射线密度仪联用校验,排除骨料沉降带来的局部阻力偏差。
技术展望与发展建议
面对智能建造发展趋势,建议从三方面推进技术升级:一是开发集成温湿度补偿算法的智能贯入检测仪,实现施工现场原位检测;二是建立全国性混凝土凝结特性数据库,利用机器学习预测不同材料组合的凝结轨迹;三是完善极端环境下的检测标准体系,针对永冻土地区、海洋腐蚀环境等特殊工况制定补充试验规程。通过构建"检测-预警-调控"一体化平台,可望将混凝土施工质量事故率再降低50%,为新型建筑工业化提供关键技术支撑。
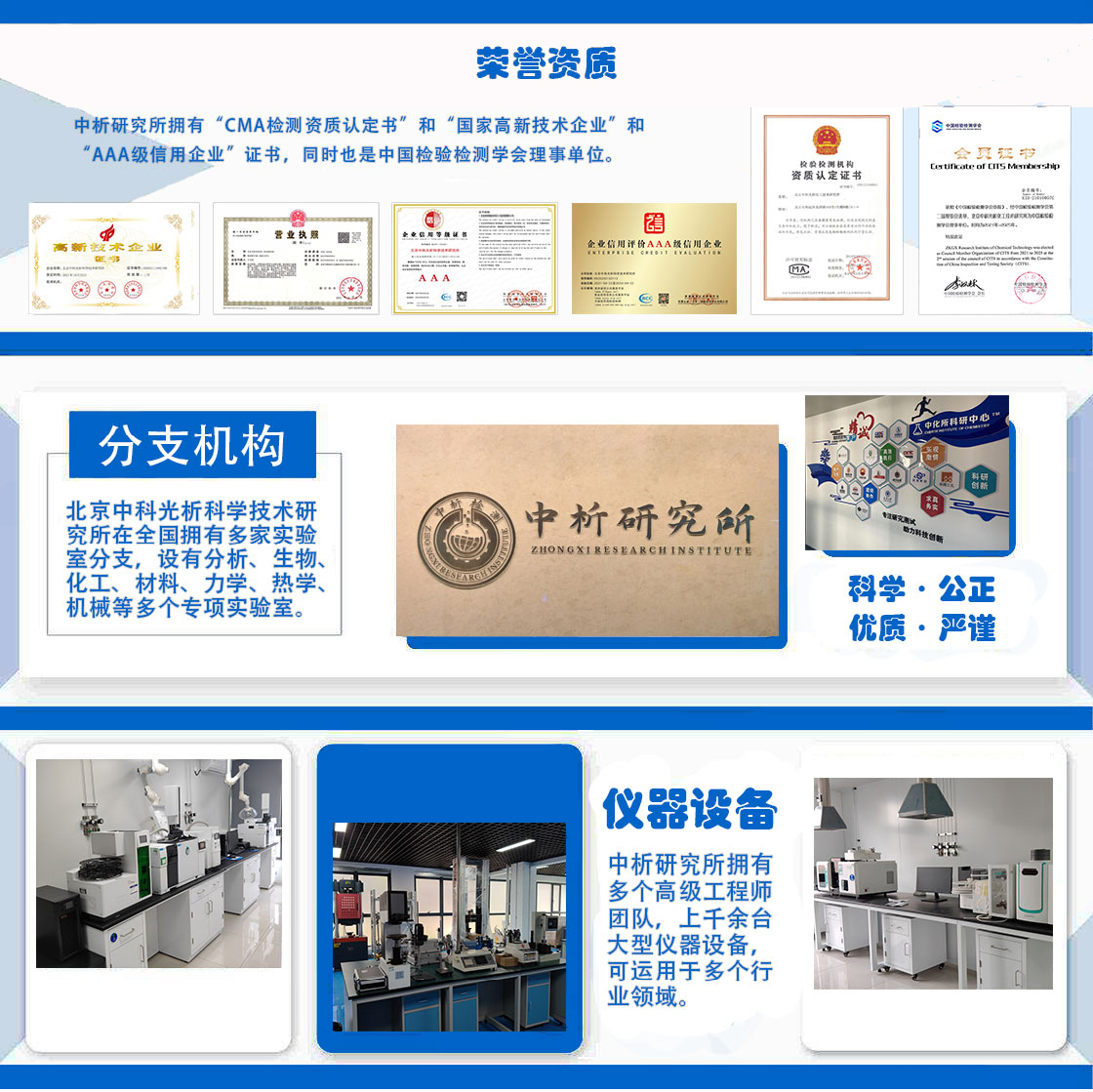
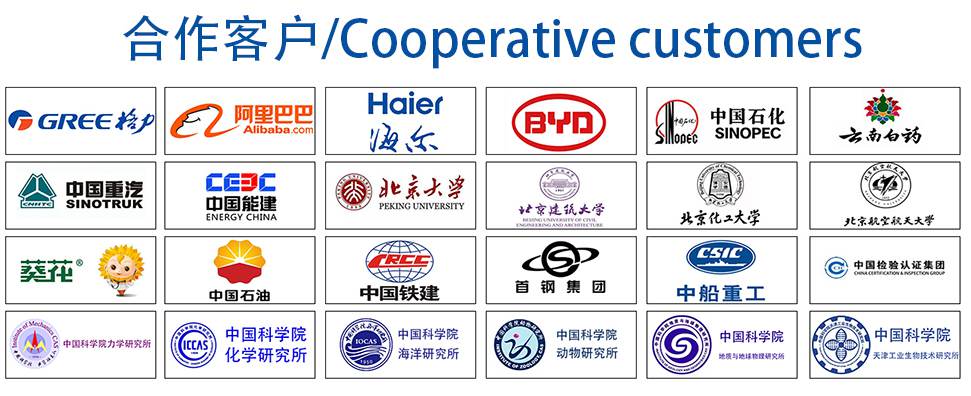