随着基础设施建设的快速发展,混凝土结构在盐碱地、海洋环境及工业污染区域的耐久性问题日益凸显。据中国建筑材料研究院2024年数据显示,硫酸盐侵蚀导致的混凝土劣化占工程结构耐久性失效案例的35%以上,由此引发的年维修成本超过120亿元。抗硫酸盐侵蚀试验检测作为评估材料耐久性的核心手段,通过模拟硫酸盐离子渗透、结晶膨胀等侵蚀过程,为工程选材与防腐设计提供科学依据。该项目不仅关乎重大工程的全生命周期成本控制,更是实现“双碳”目标下资源高效利用的关键技术支撑,其核心价值体现在预防结构性坍塌风险、延长服役寿命及降低环境治理成本三大维度。
## 技术原理与检测方法化学侵蚀机制与试验模型构建
硫酸盐侵蚀的本质是SO₄²⁻与水泥水化产物发生化学反应,生成钙矾石和石膏等膨胀性产物。试验采用GB/T 50082-2009《普通混凝土长期性能和耐久性能试验方法》中的全浸泡法与干湿循环法,通过配置5% Na₂SO₄溶液模拟严苛环境。检测系统配备恒温恒湿箱、超声波脉冲仪及XRD分析仪,实现膨胀率、强度损失率和微观结构演变的定量监测。值得注意的是,针对海洋潮汐区特有的干湿交替特征,改进型试验设备可编程控制溶液浸润-干燥周期,精准复现0.5-3.0次/天的真实环境波动。
标准化实施流程与质控节点
检测流程分为样品制备、环境模拟、参数监测及数据分析四个阶段。根据《水工混凝土试验规程》DL/T 5150-2017要求,试件需标准养护28天后浸入硫酸盐溶液,每7天测量一次质量变化与抗压强度。关键质控点包括溶液浓度校准(误差≤±0.1%)、温湿度控制(波动范围±1℃/±3%RH)以及数据采集频率设定。针对“混凝土耐久性评估标准”的特殊需求,部分项目需同步开展氯离子渗透试验,以评估复合侵蚀效应。
典型行业应用与实证效果
在青海盐湖地区某钾肥厂地基工程中,检测发现普通C30混凝土经90天干湿循环后强度损失达42%,而掺入10%矿粉的改良试样损失率降至18%,据此优化配比方案后,项目全周期维护成本减少2100万元。另据交通运输部2023年报告,某跨海大桥桩基通过“硫酸盐干湿循环试验方法”筛选出抗蚀系数≥0.85的高性能混凝土,使设计使用年限从50年提升至70年。此类案例验证了检测技术对工程决策的支撑作用。
全链质量保障体系构建
实验室通过CMA资质认证,建立三级质量监督机制:一级控制涵盖仪器设备定期校准(采用NIST标准物质),二级控制包括平行样检测与留样复测,三级控制引入第三方机构盲样考核。针对“水工混凝土抗侵蚀技术规范”要求,开发数字化管理系统实现检测数据自动采集与异常值预警,确保结果可追溯。近三年参与能力验证的12项参数均获满意结果,数据离散系数控制在5%以内。
## 未来发展与技术展望随着智能传感技术与材料基因组学的发展,建议行业重点突破三方面:一是开发原位监测设备,实现混凝土结构硫酸盐侵蚀进程的实时可视化;二是建立多因子耦合侵蚀数据库,集成温度、应力与化学组分变量;三是推动抗硫酸盐混凝土设计规范与国际标准(如ASTM C1012)接轨。据预测,至2030年智能检测技术在工程验收中的渗透率将超过60%,为推动基础设施绿色转型提供更强技术保障。
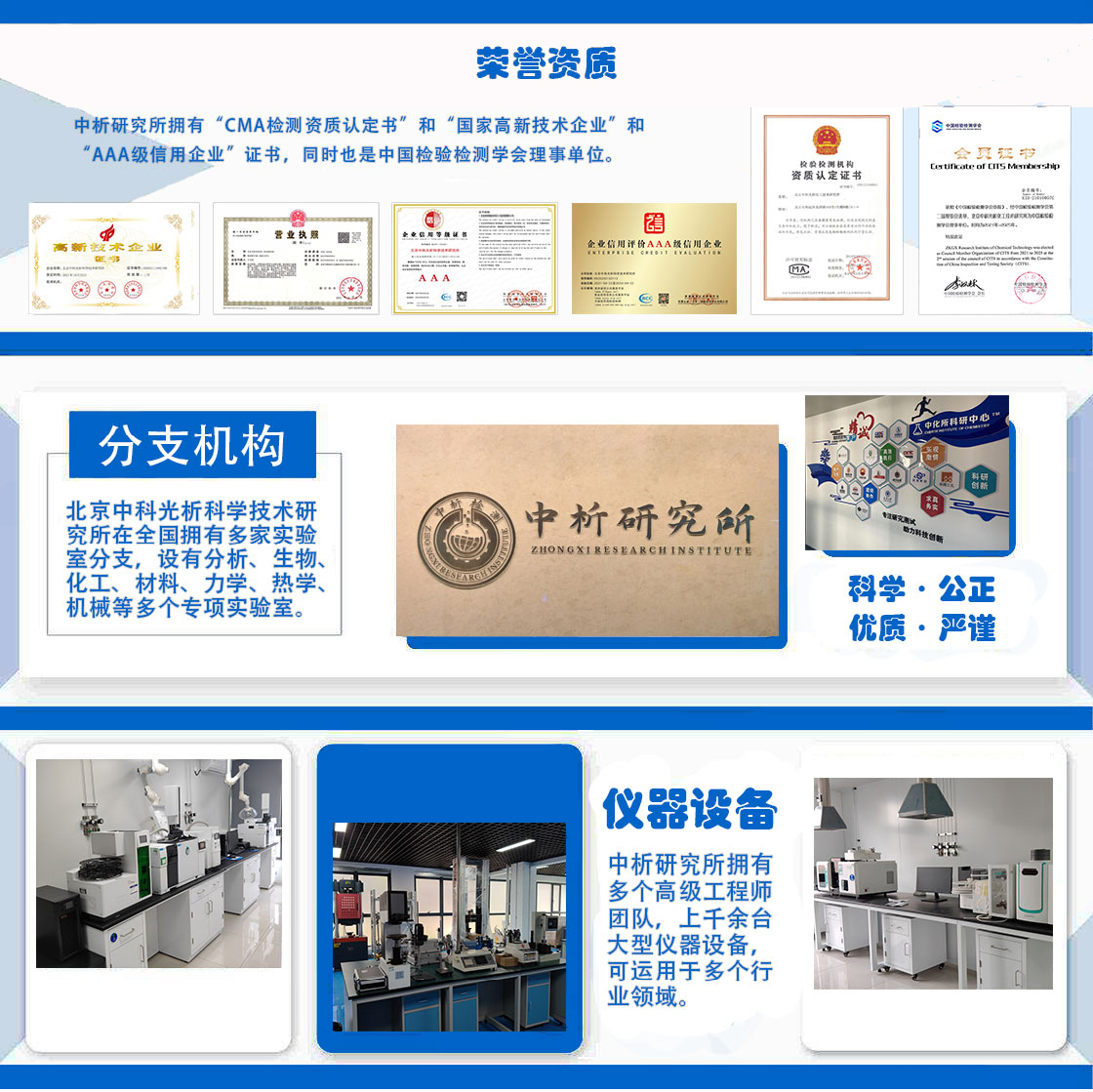
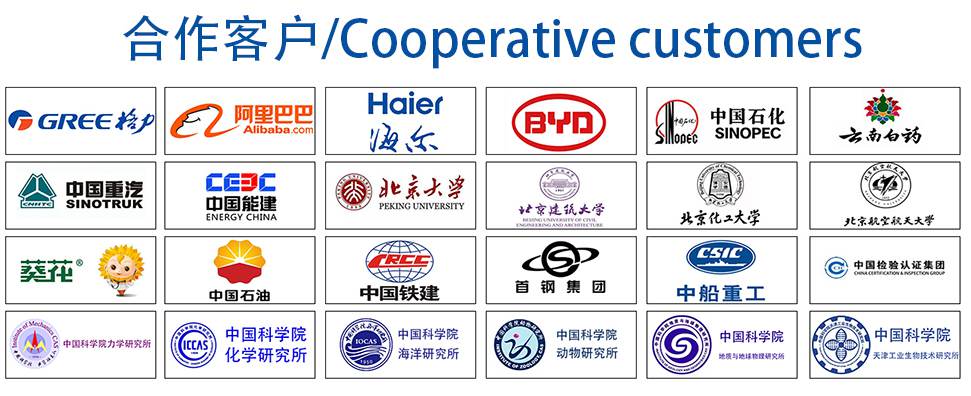