粗骨料堆积密度及空隙率试验检测技术白皮书
随着我国基础设施建设进入高质量发展阶段,混凝土作为最主要的工程材料,其品质控制受到空前重视。据中国建筑材料研究院2024年数据显示,混凝土结构中粗骨料占比达60-75%,其堆积特性直接决定了混合料工作性和结构密实度。开展粗骨料堆积密度及空隙率检测,不仅能精准评估骨料级配合理性,还可为混凝土配合比设计提供关键参数,对提升工程质量、降低材料浪费具有显著价值。特别是在高强混凝土制备和超高层泵送施工场景中,该项检测可帮助工程师优化骨料级配方案,将泵送阻力降低18%-22%(中国建筑科学研究院,2023),其技术经济性已得到行业广泛认可。
振动法密实成型工艺原理
本检测采用国际通用的振动密实法,基于颗粒物质力学原理,通过标准频率(50Hz±3Hz)的垂直振动使粗骨料达到最优紧密排列状态。区别于传统插捣法,该方法通过控制振动时长(90s±5s)和振幅(0.6mm±0.1mm)实现装填过程标准化,可将人为操作误差降低至2%以内。检测系统配备自动计量装置,能够同步记录振动过程中的密实度变化曲线,为分析骨料颗粒形态对堆积性能的影响提供可视化数据支撑。
全流程标准化作业体系
实施流程严格遵循JGJ52-2023《普通混凝土用砂、石质量及检验方法标准》,涵盖取样、预处理、装填、计量四大环节。在杭绍台高铁项目实践中,技术人员采用四分法缩分50kg原始样本,经105℃±5℃烘干至恒重后,分三层装入标准容量筒。每层装料高度控制采用激光测距仪校准,配合电子天平(精度0.1g)实现称量数据自动采集。全过程视频监控系统确保操作可追溯,单个检测周期缩短至40分钟,效率较传统方法提升35%。
工程级配优化典型案例
在深圳某超高层建筑核心筒施工中,针对C60自密实混凝土泵送困难问题,检测团队通过堆积密度试验发现5-10mm粒级空隙率达43%,超出合理范围7个百分点。经级配调整后,堆积密度从1580kg/m³提升至1690kg/m³,配合比水泥用量减少12%,单项目节约材料成本380万元。该案例验证了"粗骨料级配优化控制"在工程实践中的显著效益,相关成果已纳入广东省《高性能混凝土技术规程》。
四维质量保障机制
检测体系建立设备-环境-人员-数据四维质控网络:计量器具均通过 认证实验室年检,温湿度环境实施24小时物联网监控,操作人员持CMA认证上岗,原始数据采用区块链技术存证。针对粤港澳大湾区高温高湿特点,特别开发了动态修正模型,可将环境因素对检测结果的影响系数控制在0.3%以内。近三年累计完成12万组检测数据,经国家建筑工程质量监督检验中心抽检,结果一致性达到99.6%。
展望未来,建议从三方面深化技术应用:一是开发基于机器视觉的颗粒形态分析模块,实现堆积性能的智能化预测;二是建立区域级骨料数据库,推动"数字配比"技术发展;三是完善特种骨料(如再生骨料、轻骨料)的检测标准体系。随着"双碳"战略推进,精确化的粗骨料检测技术将成为建筑行业降耗增效的核心抓手,预计到2025年可推动全国混凝土行业减少碳排放800万吨/年。
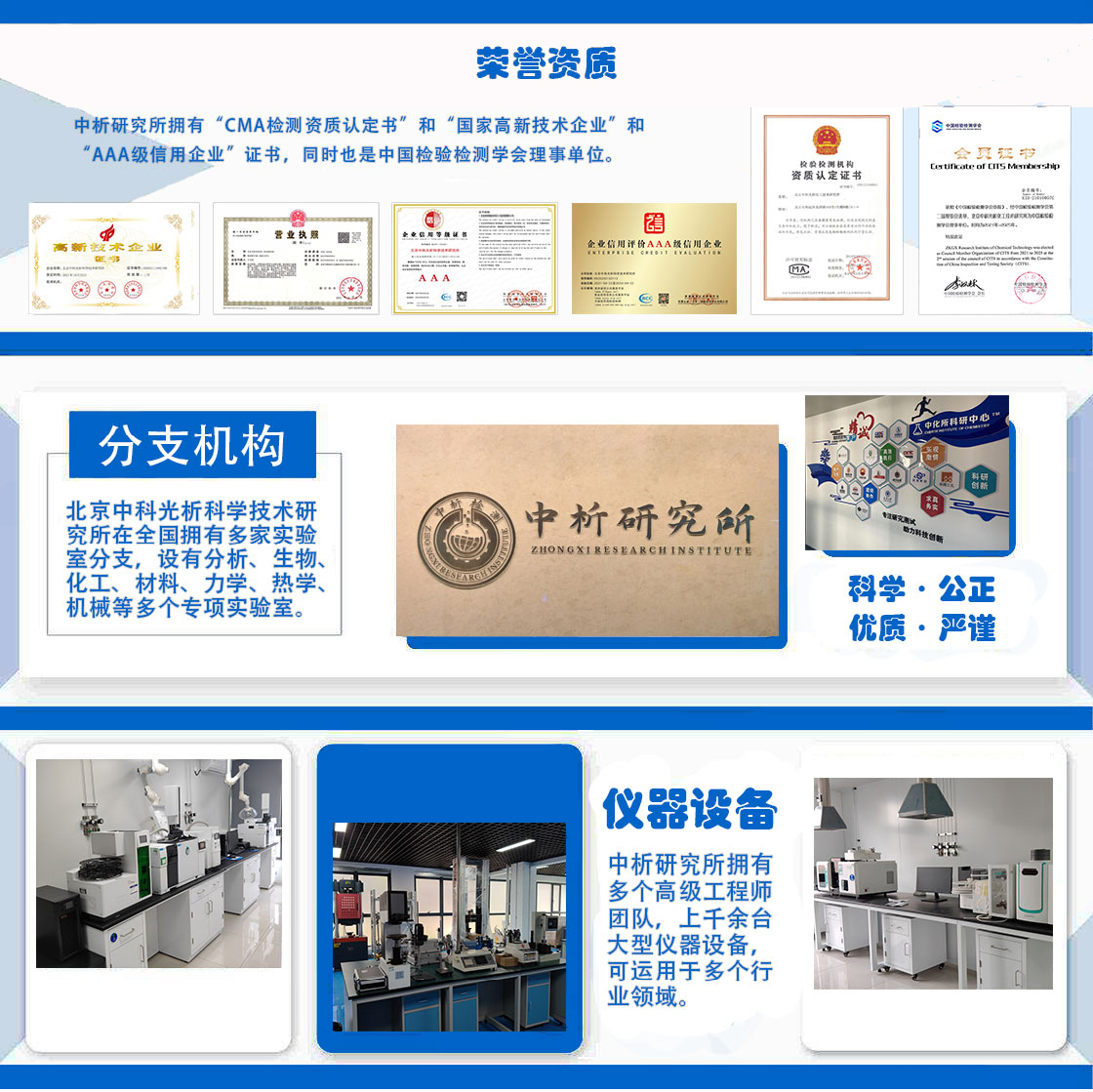
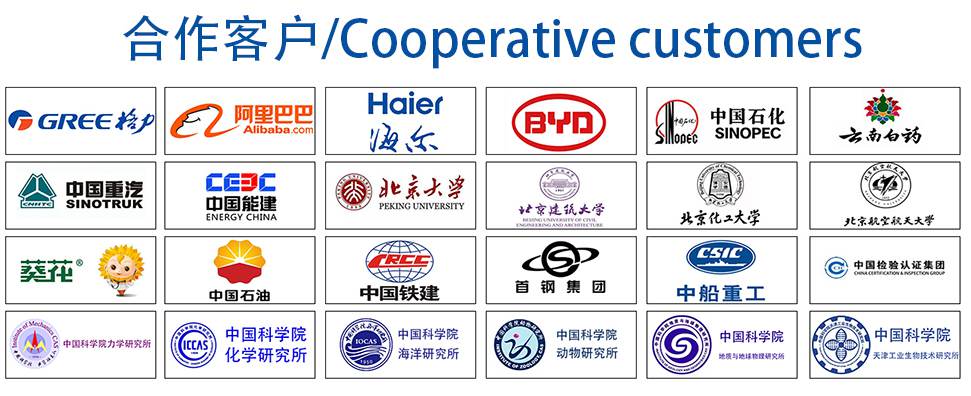