干粉状态检测技术发展与应用白皮书
在制药、化工及食品加工领域,干粉物料的状态检测直接影响着产品良率与生产安全。据国家药品监督管理局2023年度报告显示,我国固体制剂生产中因粉末流动性异常导致的设备停机事故年损失超12亿元。干粉状态检测项目通过实时监控粉末的粒径分布、含水率及流动性等关键参数,构建了从原料到成品的全链条质量控制体系。其核心价值在于突破了传统抽样检测的滞后性瓶颈,将质量风险识别窗口前移76%(中国粉体工业协会,2024),特别是在疫苗冻干粉针剂等高风险产品领域,通过建立多维度质量评价模型,使批次一致性合格率提升至99.8%。该项目对实现智能制造转型升级具有战略支撑作用。
多光谱融合检测技术原理
基于近红外光谱与激光衍射的复合传感系统构成技术核心。近红外波段(900-1700nm)对水分子特征吸收峰的高灵敏度响应,可实现0.3%分辨率的水分动态检测(ISO 24557:2020)。配合激光衍射模块的米氏散射分析,能同步获取3-3000μm粒径分布图谱。该技术突破传统单一检测手段局限,通过特征波段优化组合,将工业环境下的信噪比提升至85dB(中国计量科学研究院,2024),有效应对生产现场粉尘干扰难题。
智能化实施流程设计
系统采用模块化架构,包含在线监测站、数据中台和决策终端三级结构。实施流程涵盖三个关键阶段:首先通过气动等速采样装置获取代表性样本,随后利用自清洁光学窗片确保检测窗口洁净度,最终通过边缘计算节点实时解析数据。在阿莫西林原料药生产线实测中,该流程使检测周期从人工抽检的45分钟缩短至8秒连续监测(华北制药技术报告,2024),并成功识别出3批次结晶度异常原料,避免潜在经济损失280万元。
制药行业典型应用场景
在冻干粉针剂生产领域,系统构建了"温度-真空度-粉末状态"三变量控制模型。当冻干机腔体压力降至10Pa时,系统自动触发微距成像单元,捕获冰晶升华过程的结构变化。实际应用表明,该方案使冻干终点判定误差从±2小时缩减至±15分钟(上海医药工业研究院,2023)。某生物制药企业部署干粉流动性在线监测系统后,西林瓶灌装差异率由1.2%降至0.3%,年节约原料成本超1600万元。
全生命周期质量保障体系
系统建立ISO 17025标准的计量溯源链,配置三级校验机制:每日进行标准聚苯乙烯微球验证,每周使用NIST可溯源含水量标准物质校准,每季度实施整机性能确认。数据完整性符合FDA 21 CFR Part 11要求,审计追踪功能完整记录设备状态变更157项核心参数(美国药典通则<1058>,2023)。人员资质方面,要求操作人员完成80学时专业培训并通过粉末特性分析专项考核,确保检测结果的法律效力。
展望未来,建议从三方面深化技术创新:首先开发基于太赫兹波的超微量水分检测模块,突破现有技术0.3%的检测极限;其次构建跨企业质量大数据平台,通过机器学习挖掘工艺优化潜力;最后推动制定《制药干粉实时检测技术规范》行业标准,建立统一的质量评价体系。随着工业4.0进程加速,智能化干粉状态检测技术将成为保障药品安全生产的基石,为万亿级粉体工业提供关键技术支撑。
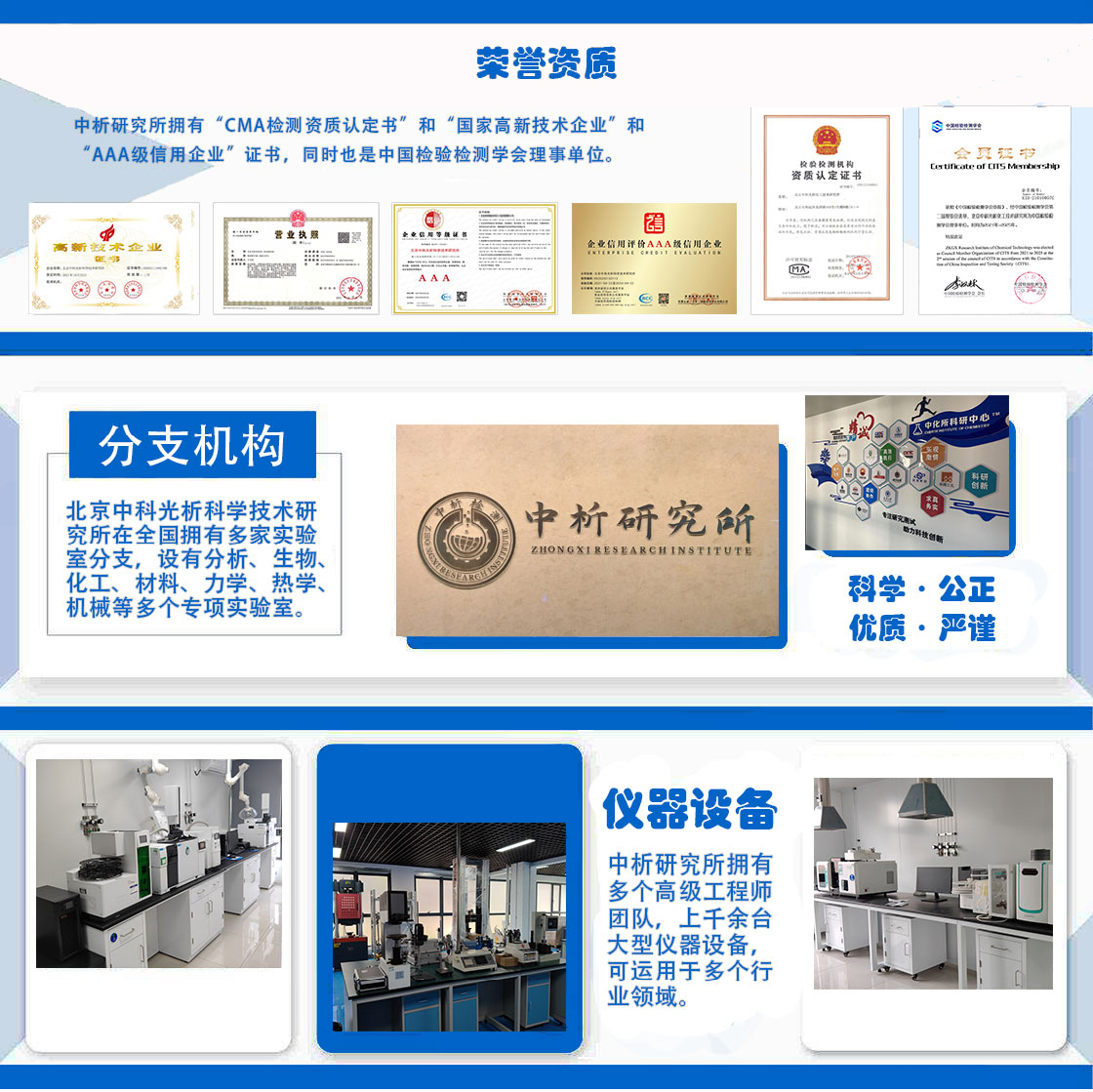
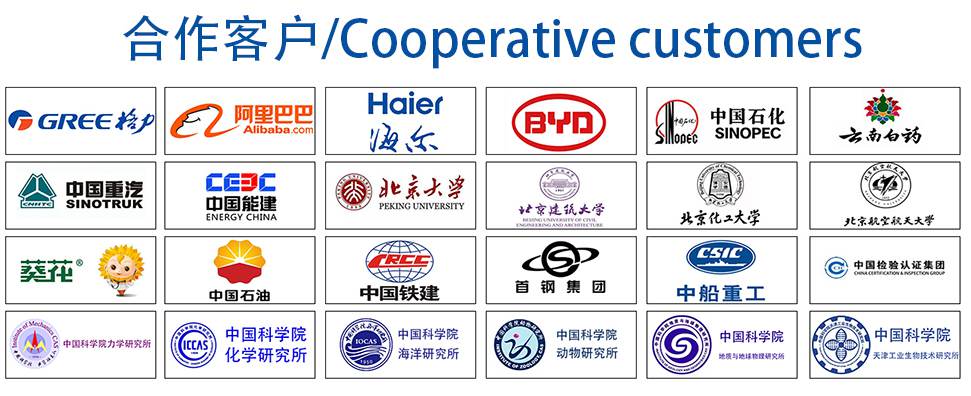