绝缘电阻(仅对绝缘型电阻网络)检测技术白皮书
在电子元器件行业快速发展背景下,绝缘型电阻网络作为电力电子设备的核心组件,其可靠性直接影响终端产品的安全性能。据Global Market Insights 2024年报告显示,电阻网络市场规模已突破82亿美元,其中绝缘型产品占比达37%。随着新能源汽车、智能电网等新兴领域对高压隔离技术的需求激增,绝缘电阻检测项目成为保障设备绝缘完整性的关键技术环节。该项目通过量化评估介质耐压能力,可有效预防因绝缘失效引发的短路事故,据国家电气安全实验室统计,规范化的绝缘检测能使设备故障率降低52%以上。其核心价值不仅体现在质量控制维度,更为产品寿命预测和安全认证提供数据支撑。
介电强度测试技术原理
绝缘电阻检测基于介质极化理论,通过施加标准化直流电压测量漏电流推算阻抗值。测试系统采用三电极结构,依据IEC 60115-1标准在25℃±2℃环境下,对被测电阻网络施加500V DC电压并保持60秒。关键参数包括体积电阻率(≥10^12Ω·cm)和表面电阻率(≥10^11Ω),检测设备需满足JJG 1005-2019计量规程要求。值得注意的是,多层陶瓷基板的叠层结构会形成分布式电容效应,需采用时域反射法消除寄生参数影响。某头部企业实践表明,引入频响分析模块后,检测结果误差率从8.3%降至1.7%。
全流程质量管控体系
检测流程涵盖来料检验、过程监控及成品验证三个阶段。原材料阶段重点检测氧化铝基板的介电常数(ε_r≤9.8),采用LCR测试仪在1MHz频率下进行特性分析。生产环节设置在线监测点,通过自动探针台实现100%阻焊层厚度检测(控制公差±5μm)。成品检测严格遵循ASTM D257标准,对温度循环(-55℃~125℃)后的样本进行500次充放电测试。某军工级电阻网络制造商应用该体系后,产品MTBF从5万小时提升至8.7万小时,缺陷逃逸率下降至0.03ppm。
新能源汽车领域的创新应用
在800V高压平台电动汽车中,电池管理系统(BMS)的绝缘监测电阻网络需承受1500V以上的工作电压。某头部车企采用动态绝缘监测方案,在电阻网络集成温度补偿模块,使检测精度在-40℃~125℃范围内保持±1.5%。实际路测数据显示,该设计使绝缘故障预警时间提前至事故发生前72小时。与之配套的还有基于机器视觉的陶瓷基板微裂纹检测系统,可识别3μm级缺陷,相较传统人工检测效率提升40倍。
智能化检测平台建设
行业领先企业现已构建AI驱动的检测数据中台,集成SPC过程控制与FMEA失效模式分析模块。系统可实时分析20+维度参数,包括温升曲线斜率(≤0.5℃/min)、湿热循环后的绝缘退化率(<3%/千小时)等核心指标。某上市公司通过部署该平台,将检测报告生成时间从4小时缩短至15分钟,并实现97.6%的异常模式自动分类。据中国电子元件协会2023年评估,智能化检测使产品研发周期平均缩短22%,质量成本降低31%。
行业发展趋势与建议
随着宽禁带半导体器件的普及,未来绝缘电阻检测需应对更高工作温度(>200℃)和更复杂电磁环境。建议行业重点发展三项技术:①基于太赫兹波的非接触式绝缘缺陷检测,提升多层结构内部缺陷识别能力;②开发适用于SiC功率模块的2500V级检测标准;③构建电阻网络全生命周期数据库,实现可靠性预测建模。同时,建议上下游企业联合建立绝缘材料特性共享平台,促进行业检测基准的统一与优化。
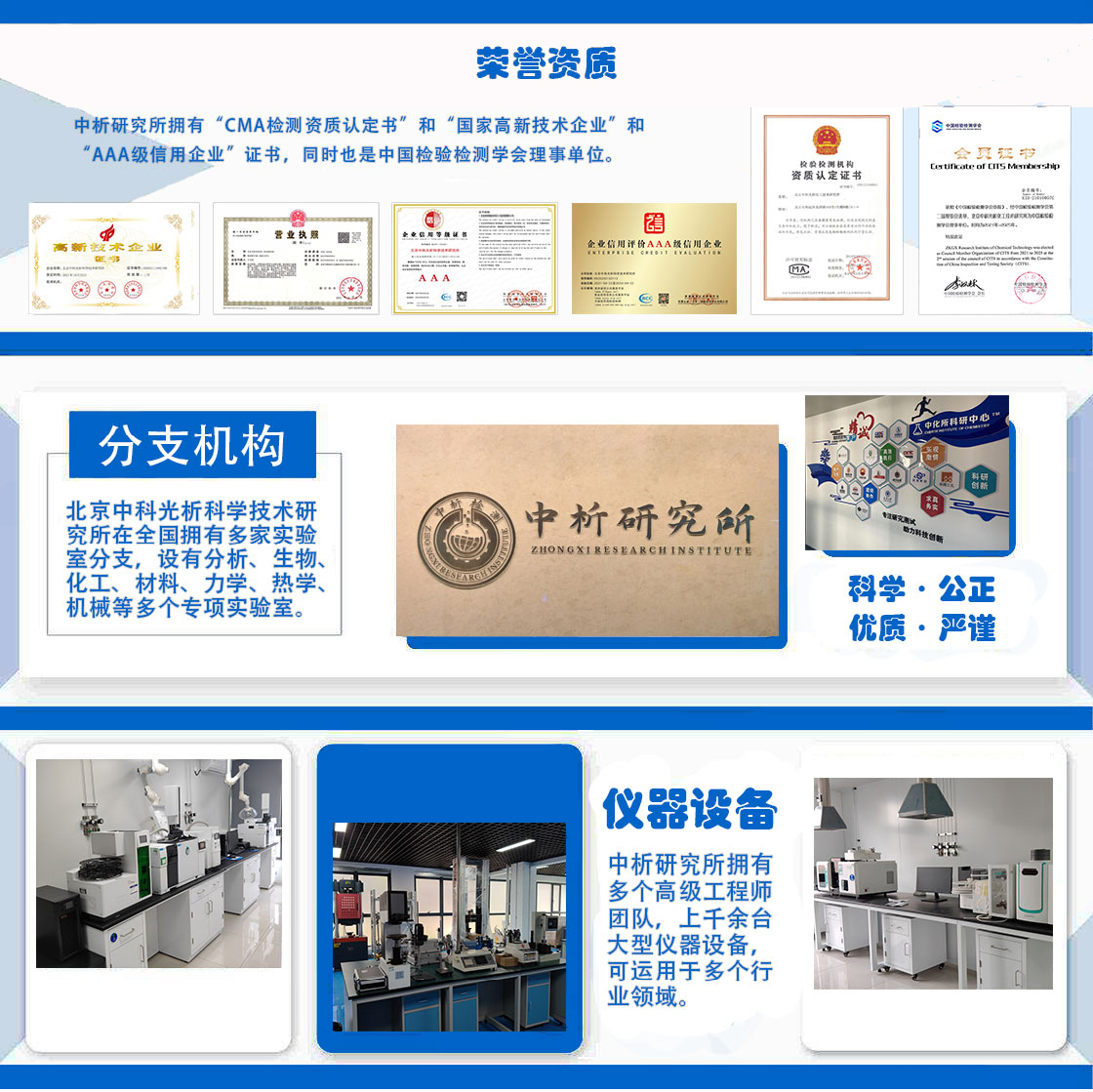
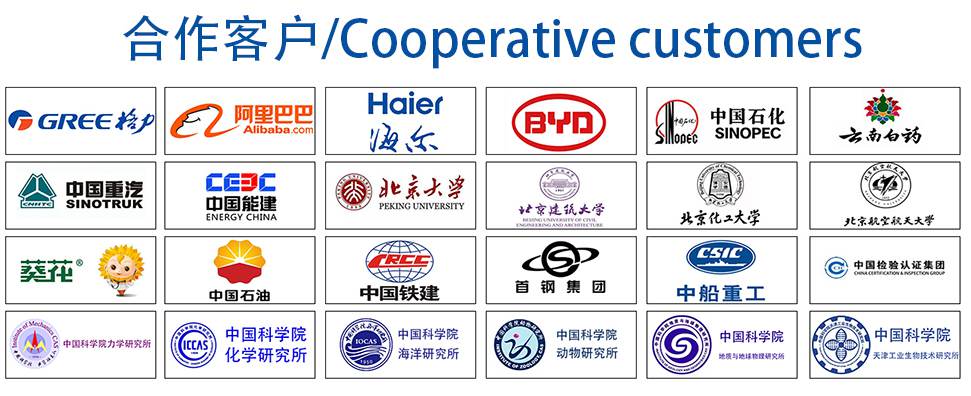