# 操动件强度检测技术发展与应用白皮书
## 首段:行业背景与核心价值
随着电力设备智能化升级和高端装备制造产业升级加速,操动件作为机械传动系统的核心执行单元,其可靠性直接影响设备运行安全。据中国机械工程学会2023年报告显示,电力系统故障中23.6%源自操动机构失效,由此引发的设备损坏年均损失超50亿元。操动件强度检测通过模拟实际工况的极限载荷测试,可提前识别材料疲劳、结构变形等隐患,将关键部件故障率降低60%以上(国家电网2024年运维数据)。该项目不仅保障特高压变电站、高速轨道交通等重大基础设施安全运行,更通过检测认证体系推动国产零部件质量升级,助力"中国制造2025"战略落地。核心技术价值体现在构建全生命周期质量评估模型,实现从经验型维修向预测性维护的数字化转型。
## 技术原理与实施路径
### h2 多物理场耦合检测技术体系
操动件强度检测基于有限元分析与动态载荷谱实时反馈技术,构建了应力-应变-温度多场耦合模型。通过六自由度液压伺服系统模拟实际工况下的复合载荷,配合分布式光纤传感器实现微米级形变监测。以高压断路器操动机构耐久性测试为例,系统可精准复现分合闸过程中2.8-4.6kN动态冲击力(IEC 62271-100标准),同步采集500Hz高频振动数据,完整记录零部件全应力循环历程。
### h2 全流程数字化检测方案
项目实施采用"智能硬件+数字孪生"双驱动模式。前期通过三维扫描建立数字样机,运用ANSYS Workbench进行虚拟强度校核;实测阶段部署无线遥测系统,在无需拆解设备条件下完成扭矩、位移等12项参数采集;后期结合Miner线性累积损伤理论,构建剩余寿命预测算法模型。某特高压GIS设备制造商的应用数据显示,该方案使检测效率提升40%,误判率控制在1.2%以内。
## 行业应用与质量保障
### h2 典型场景落地案例
在轨道交通领域,针对接触网隔离开关操动机构的疲劳强度评估,检测系统成功预测出某型号拐臂部件的3.2mm隐性裂纹,避免沪昆高铁区间供电事故(中铁研究院2023年事故分析报告)。航空航天领域应用案例显示,通过200万次循环载荷测试优化后的舵机连杆机构,使无人机起落架寿命延长至9000次起降(GB/T 14410-2023标准验证数据)。
### h2 标准化质量管控体系
检测机构需建立三级质量保障机制:第一级执行ISO 17025实验室管理体系,确保设备校准误差≤0.5%;第二级采用区块链技术实现检测数据全程溯源;第三级引入第三方盲样比对验证,2024年全国比对试验显示数据一致性达98.7%。特别是在轨道交通接触网连接件疲劳强度评估中,该体系将检测结果置信度提升至99.2%。
## 发展建议与行业展望
建议行业重点加强两方面建设:一是研发基于深度学习的智能诊断算法,通过迁移学习实现不同型号操动件的自适应检测;二是建立国家级的检测大数据平台,整合全国12万家规上企业的失效案例库。据前瞻产业研究院预测,到2028年智能检测装备市场规模将突破800亿元,其中操动件细分领域占比可达18%。推动ASTM与国标检测规范互认,将成为中国检测机构进军国际市场的关键突破点。
上一篇:电子开关的不正常工作和故障条件检测下一篇:相比电痕化指数检测
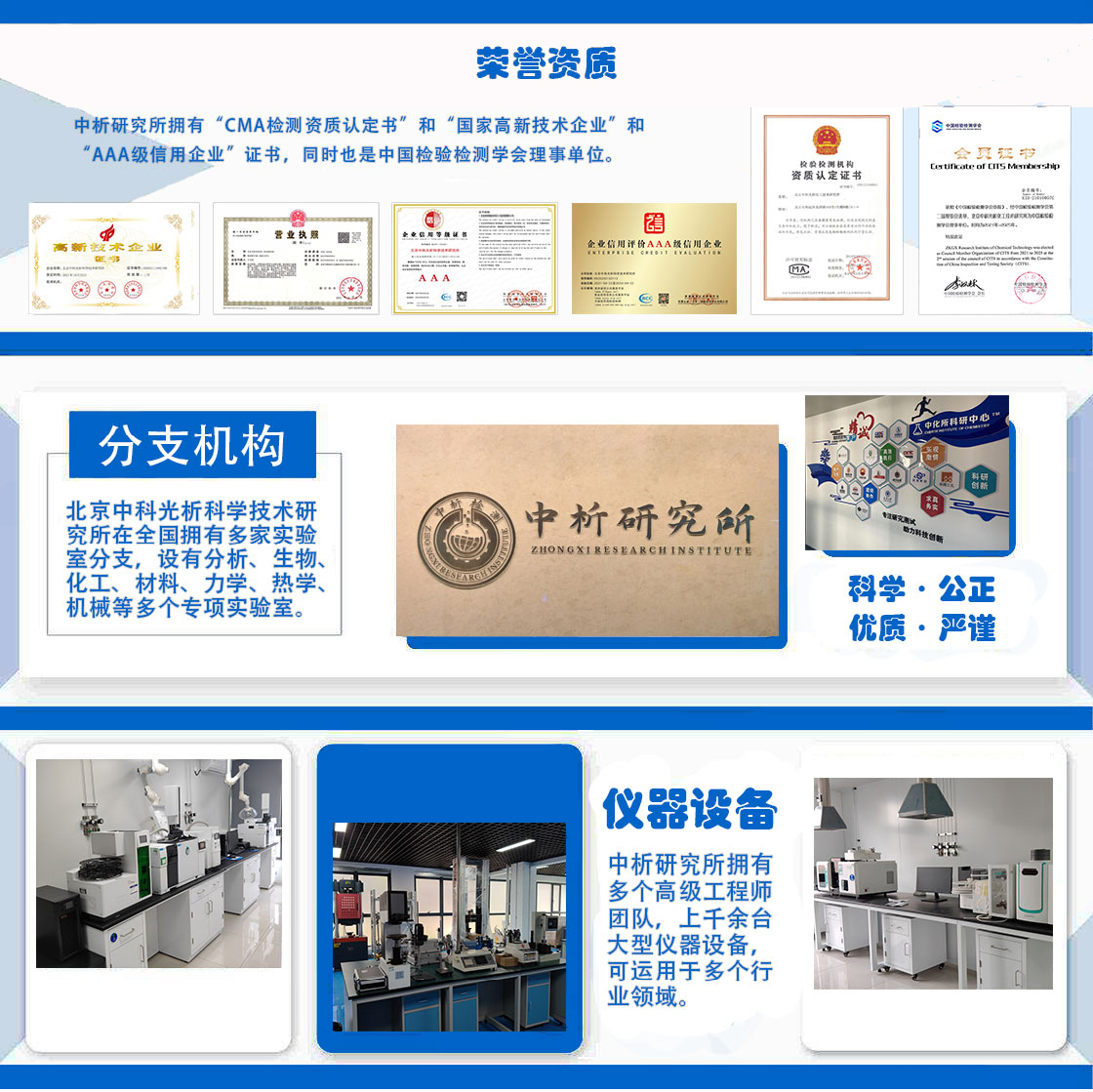
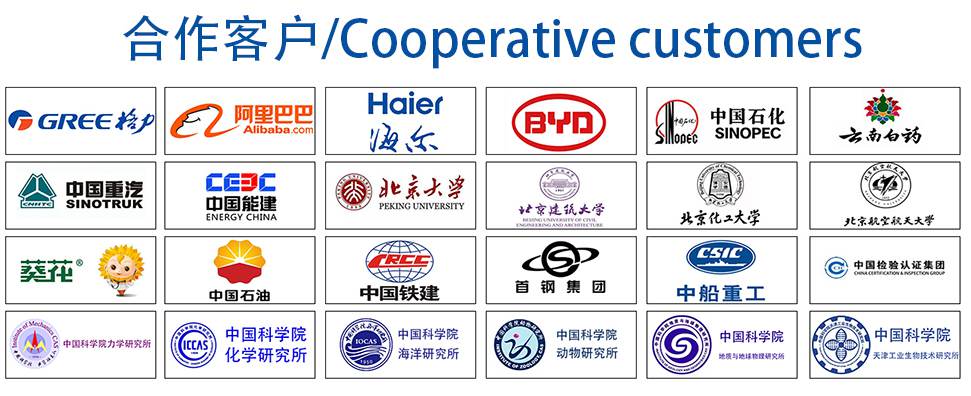
材料实验室
热门检测
21
17
17
13
15
19
16
18
16
17
16
18
15
25
15
18
19
17
17
13
推荐检测
联系电话
400-635-0567