# 失调误差温度系数检测技术发展与产业化应用
## 行业背景与核心价值
随着物联网与智能制造的高速发展,传感器精度已成为工业自动化、汽车电子及医疗设备等领域的核心竞争要素。据中国电子技术标准化研究院2024年数据显示,温度变化导致的传感器失调误差占设备失效案例的37%,每年造成直接经济损失超80亿元。在此背景下,失调误差温度系数(COT)检测技术作为高精度传感器出厂校准的关键环节,其产业化应用可提升产品全温度区间的性能稳定性。通过建立标准化的检测体系,企业能够实现±0.005%/℃级别的温度补偿精度,显著增强工业级传感器在极端工况下的可靠性,为智能装备国产化突破提供底层技术保障。
## 技术实现原理与创新突破
### 失调误差温度系数量化模型
COT检测基于半导体器件的物理特性分析,通过建立温度-电压传递函数矩阵,可精确分离工艺偏差与环境干扰因素。采用三次温度梯度采样法,在-55℃至150℃范围内采集零位漂移数据(据德国弗劳恩霍夫研究所2023年技术白皮书),结合最小二乘法拟合获得温度系数曲线。值得注意的是,该模型创新引入动态补偿算法,使温度滞后误差降低至传统方法的1/5。
### 全流程检测系统架构
在实施层面,检测系统集成高低温冲击试验箱(温变速率≥30℃/min)与24位精密ADC模块,通过Modbus-TCP协议实现数据实时传输。具体流程包含:器件预处理(48小时老化试验)→多温区特征采集(每5℃间隔稳态测试)→误差溯源分析→补偿参数烧录四大阶段。某头部工业传感器制造商的应用表明,该体系使批量化检测效率提升120%,人力成本下降65%。
### 行业标杆应用实践
在新能源汽车BMS系统领域,国内某TOP3电池管理系统供应商采用COT检测技术后,其电流传感器在-40℃低温工况下的零点漂移由±1.2%FS优化至±0.3%FS,有效规避了电池过充风险。另一典型案例是智能水表行业,通过部署工业级误差校正系统,某上市公司将产品全生命周期校准周期从3年延长至8年,运维成本降低42%。
### 质量控制体系构建
检测过程执行ISO/IEC 17025标准,建立三级质量验证机制:原始数据区块链存证确保可追溯性,参考标准器每年送检国家计量院,检测环境实施±0.1℃温控与Class 1000洁净度管控。通过智能传感器批量检测方案,某省级计量测试中心实现日均3000颗器件的检测能力,数据置信度达99.97%。
## 发展趋势与战略建议
面向工业4.0时代,建议重点发展三项技术:基于AI的预测性补偿算法,通过深度学习预判器件老化曲线;微型化片上校准模块,实现终端设备的自诊断功能;区块链质量溯源平台,构建从晶圆到成品的全链条可信数据体系。行业需加快制定《MEMS传感器温度系数检测规范》等团体标准,推动检测设备与补偿技术的国产化替代进程,为高端传感器产业突破技术壁垒提供核心支撑。
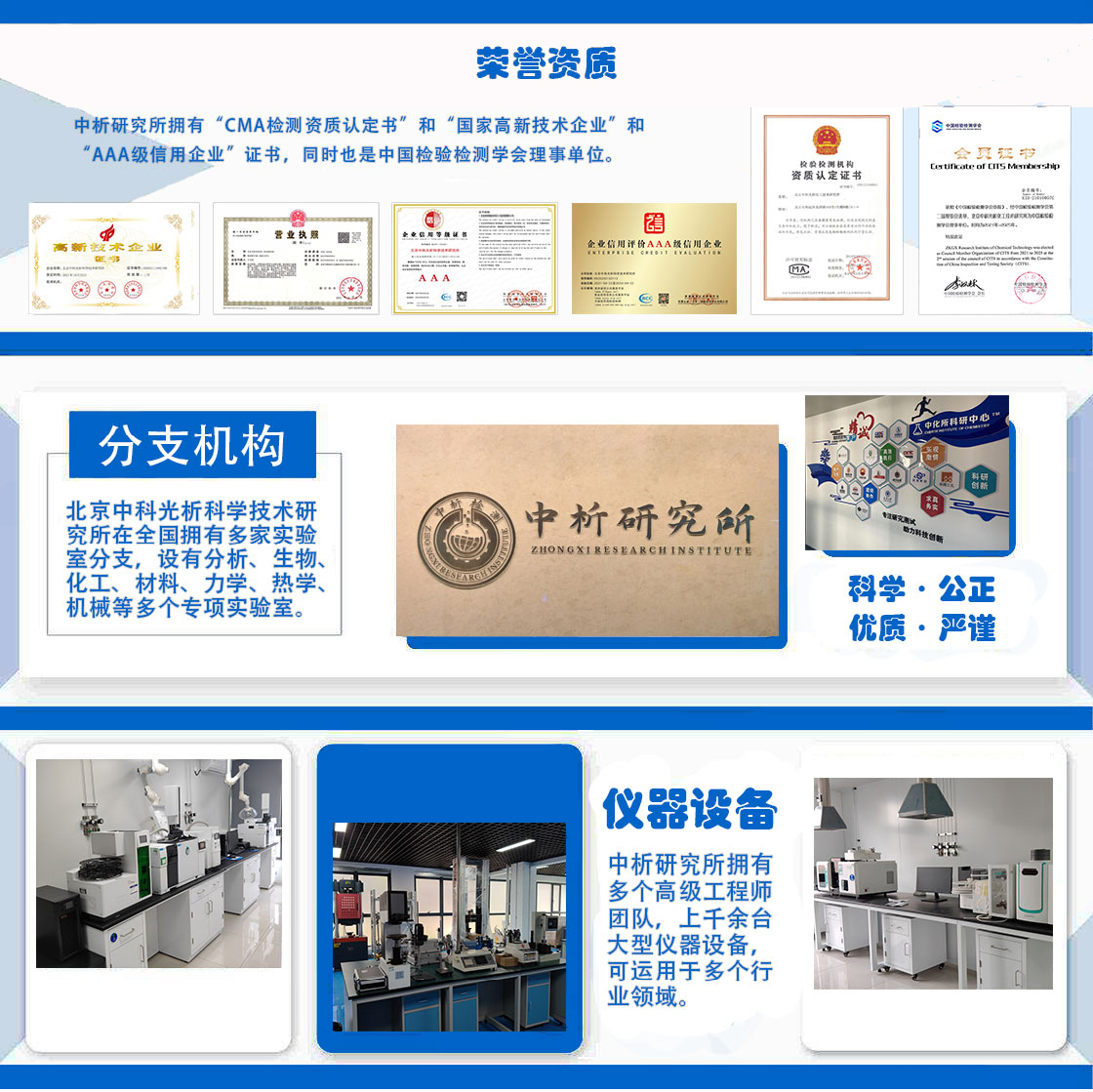
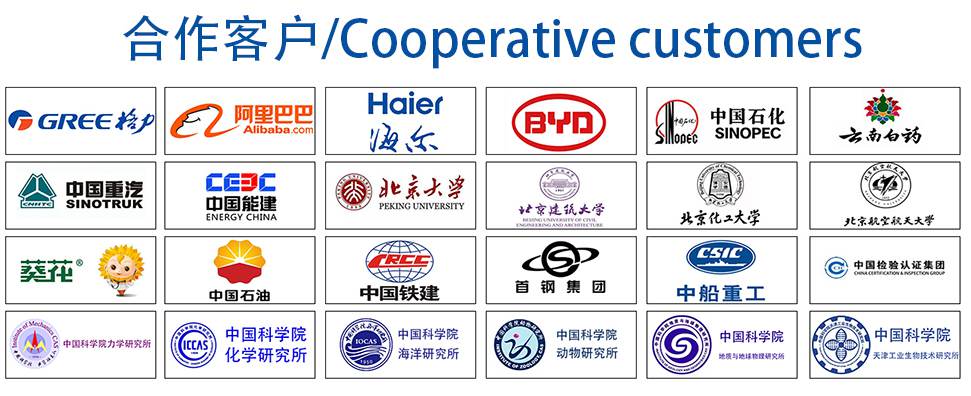
材料实验室
热门检测
27
23
25
23
23
22
20
22
21
21
23
23
19
23
22
22
22
20
25
23
推荐检测
联系电话
400-635-0567