里氏硬度检测:核心检测项目详解
一、里氏硬度检测的核心检测项目
-
- 检测内容:通过冲击装置(如D型或G型冲击头)垂直撞击材料表面,测量冲击体反弹速度与冲击速度的比值,转换为里氏硬度值(HL)。
- 依据标准:ISO 16859、ASTM A956等。
- 适用范围:碳钢、合金钢、铸铁、有色金属(如铝、铜合金)等。
- 数据解读:结果可直接显示为HL值,或通过换算表转为布氏(HB)、洛氏(HRC)等常用硬度单位。
-
- 检测目的:检查同一工件不同区域的硬度分布是否均匀,识别材料内部缺陷(如气孔、夹杂)或热处理不均。
- 方法:在工件表面选取多个测试点(通常≥5点),计算硬度值的标准差(SD)和极差(R)。若SD超过材料标准的10%,则判定为不均。
- 应用场景:铸件、锻件、焊接接头等。
-
- 检测内容:评估渗碳、渗氮、感应淬火等表面处理工艺的硬化层深度。
- 技术要点:
- 使用高精度探头(如C型冲击头)逐层打磨后测量,绘制硬度-深度曲线。
- 硬化层深度(如HV550对应的深度)需符合ISO 2639或相关工艺标准。
-
- 检测项目:
- 回火硬度:验证回火温度是否达标(如工具钢回火后HRC 50-55)。
- 淬火硬度:检测淬火后马氏体转变的完成度。
- 注意事项:避免在氧化皮或脱碳区域测试,需提前打磨至光洁表面。
- 检测项目:
-
- 检测重点:
- 焊缝硬度:确保焊接材料与母材硬度匹配(如管道焊接接头硬度≤250 HV10)。
- 热影响区(HAZ)硬度:检测是否因焊接热循环导致硬度过高(可能引发脆裂)。
- 标准参考:ASME B31.3、EN ISO 15614。
- 检测重点:
-
- 检测目的:通过硬度变化判断材料是否因环境腐蚀或循环载荷导致性能退化。
- 典型应用:
- 化工设备:奥氏体不锈钢经氯化物腐蚀后硬度上升(可能发生σ相脆化)。
- 轴承或齿轮:疲劳损伤区域硬度可能下降5-10%。
二、检测流程与技术要点
-
- 表面处理:测试区域需打磨至Ra≤2μm,去除氧化皮、油污及涂层。
- 温度控制:工件温度需在-10°C至60°C之间,避免热胀冷缩影响数据。
- 设备校准:使用标准硬度块(如HLD=760±20)进行每日校准。
-
- 冲击方向:确保冲击方向与测试面垂直,倾斜角≤±5°。
- 测试间距:相邻冲击点间距≥3mm,避免应力叠加。
- 数据记录:自动存储多次测量结果并计算平均值,剔除异常值(如单次偏差>5%)。
-
- 硬度换算:通过内置公式或查表转换为目标硬度单位(如HLD→HRC)。
- 判定依据:根据材料牌号(如Q235、304不锈钢)或行业标准(如API 6A)设定合格范围。
三、应用领域与局限性
-
- 制造业:模具、齿轮、轴类零件的在线质检。
- 航空航天:钛合金部件、发动机叶片的硬度抽检。
- 能源行业:风电螺栓、石油管道的定期维护检测。
-
- 不适用于超薄件(厚度<5mm)或弹性模量差异大的材料(如橡胶)。
- 对表面粗糙度敏感,需严格控制预处理工艺。
四、注意事项与误差控制
- 表面质量影响:粗糙表面会导致硬度值偏低,需优先抛光。
- 磁场干扰:避免在强磁场附近测试(如电磁设备周边)。
- 材料各向异性:各向异性材料(如轧制钢板)需注明测试方向。
- 数据修正:对曲率半径<30mm的圆柱面,需进行曲率补偿修正。
五、未来发展趋势
- 智能化升级:结合无线传输与AI算法,实现实时数据分析和云端存储。
- 微型探头开发:用于狭窄空间(如内孔、深槽)的高精度检测。
- 多参数融合:将硬度值与残余应力、金相分析结合,提供综合材料性能报告。
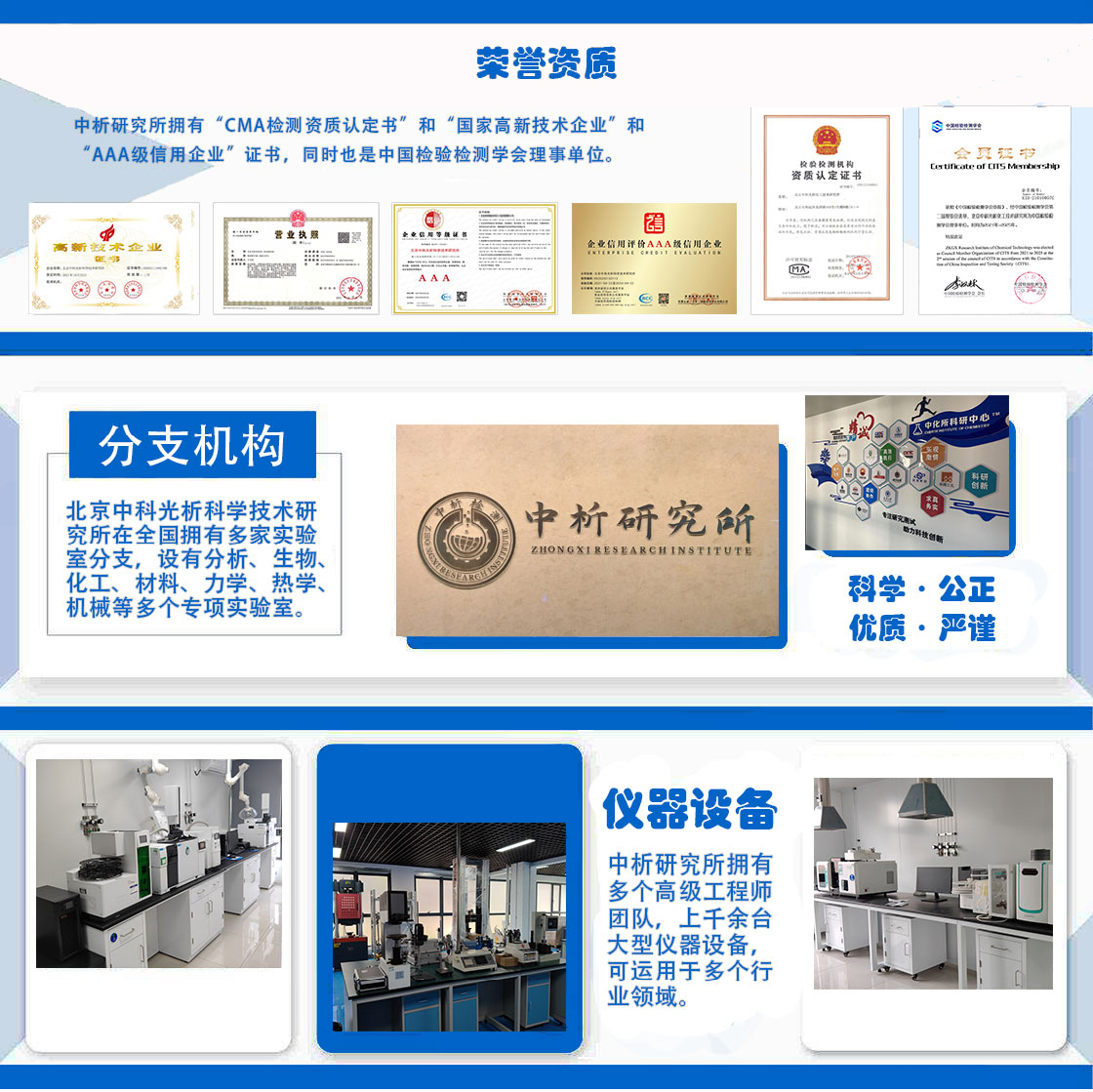
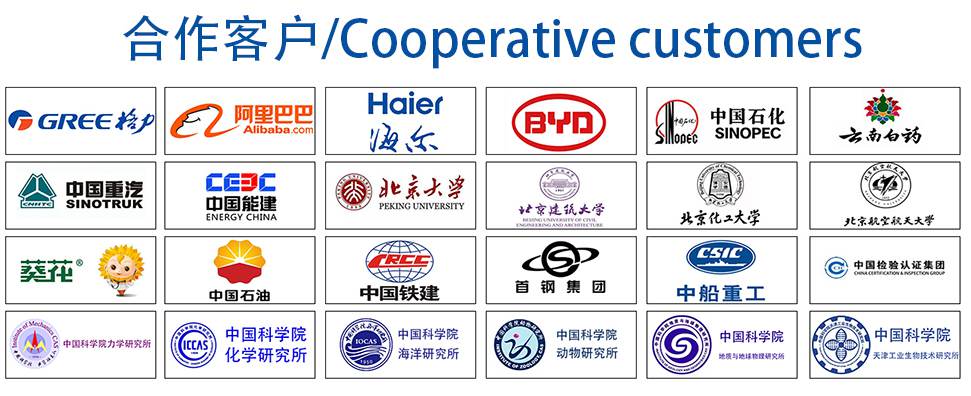
材料实验室
热门检测
13
17
15
14
18
15
22
14
20
23
22
16
21
15
18
13
17
22
19
19
推荐检测
联系电话
400-635-0567