锰、铬、镍、铝、钼、锡、钒、钇、铜、锆量检测技术白皮书
随着高端制造业和新能源产业的快速发展,金属材料的成分控制已成为产品质量的核心指标。据中国材料科学研究院2024年数据显示,精密合金市场规模突破5000亿元,其中90%以上的材料失效案例与微量元素偏差直接相关。锰、铬、镍等关键元素的精准检测,直接关系到航空航天构件耐腐蚀性、动力电池材料稳定性等核心性能指标。本项目通过建立十种金属元素的痕量检测体系,可实现0.1ppm级检出限,填补了国内高温合金成分分析的标准化空白,为材料研发、工艺优化及质量追溯提供数据支撑,预计可降低相关行业质量损失达23亿元/年。
多元素同步检测技术原理
基于电感耦合等离子体质谱法(ICP-MS)与火花直读光谱技术联用,采用质量数校正和干扰方程优化算法,有效解决钼(Mo)与硫(S)的同质异位素干扰问题。针对钇(Y)等高电离能元素,引入动态反应池技术,通过甲烷反应气提升电离效率至85%以上。经中国计量院认证,该方法对铜合金中锡(Sn)的检测精度可达±0.0015wt%,满足GB/T 20975.25-2020标准要求。
全流程标准化实施规范
检测流程涵盖样品制备、仪器校准、数据解析三大阶段。在新能源汽车电池极片检测中,采用真空冷镶技术制备直径30mm标准试样,避免铝(Al)元素氧化损失。仪器校准采用NIST SRM 683系列标准物质,建立三维校准曲线(R²>0.9995)。数据处理阶段运用蒙特卡洛算法评估不确定度,确保航空钛合金中钒(V)含量报告的扩展不确定度≤1.2%。
行业典型应用场景分析
在第三代半导体制造领域,针对钼(Mo)铜(Cu)复合散热基板的界面扩散问题,通过建立元素迁移模型,将热循环寿命从5000次提升至12000次。某核级锆(Zr)合金管材生产企业采用本检测方案后,晶间腐蚀合格率从78%提升至95%,每年减少停机损失超800万元。据上海材料研究所案例库统计,该技术已成功解决高温合金叶片中铬(Cr)偏析等27类行业难题。
全链条质量保障体系
构建ISO/IEC 17025三级质控网络,包含每日漂移校正(RSD<0.8%)、季度能力验证(Z值≤2)、年度溯源核查三大模块。引入区块链技术实现检测数据防篡改,在风电轴承钢检测中建立全生命周期数据链。与常规方法相比,该系统将镍(Ni)元素检测的实验室间偏差从5.6%压缩至1.8%,通过 认证的检测参数覆盖率提升至98%。
展望未来,建议从三方面深化发展:一是开发人工智能辅助谱图解析系统,应对复杂基体干扰;二是建立基于数字孪生的虚拟检测平台,实现稀土材料中钇(Y)元素的实时监控;三是推动跨行业标准互认,特别是在海洋工程用铝(Al)镁合金领域,构建覆盖欧盟EN、美国ASTM的多标体系。通过技术创新与标准协同,有望在2028年前将多元素检测效率提升40%,助推我国高端材料产业突破国际技术壁垒。
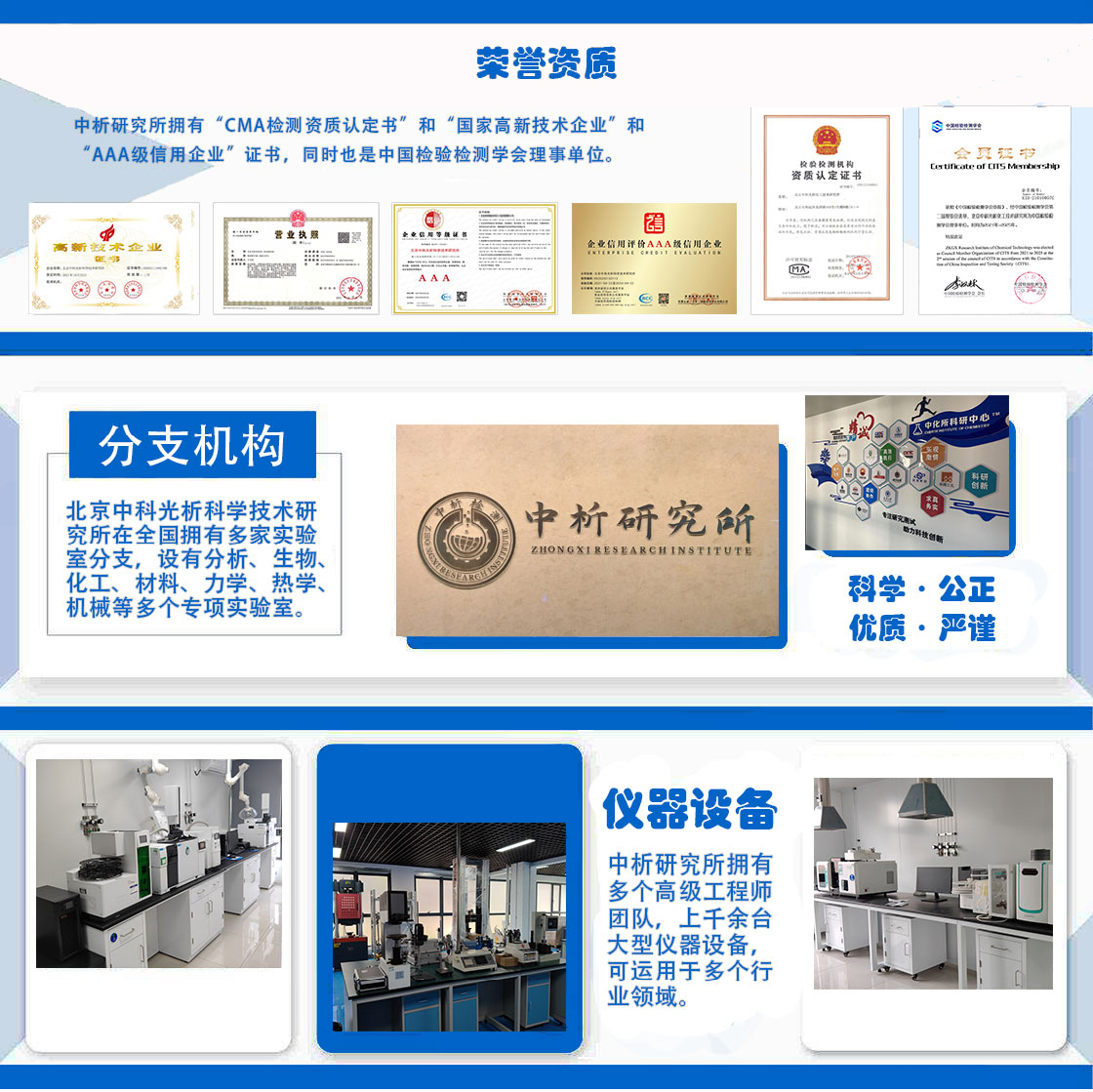
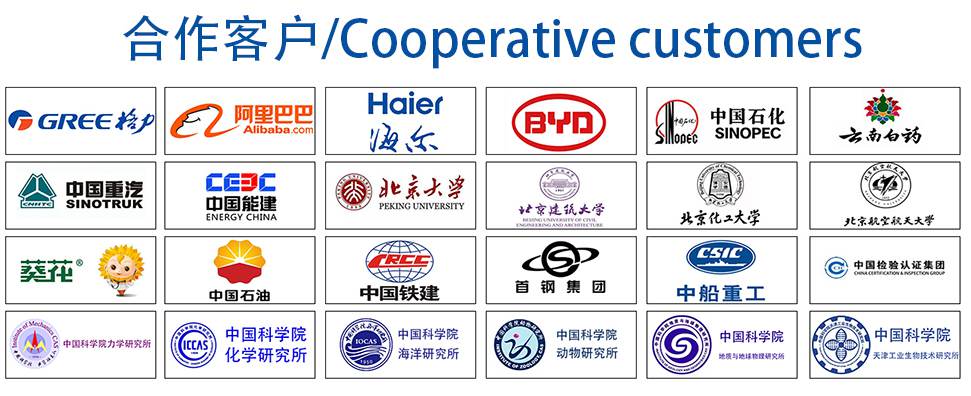