增材制造塑料零件检测技术白皮书
随着工业4.0战略的深入推进,增材制造技术在制造业中的渗透率已突破12%(据Wohlers Report 2024)。塑料材料因其成本优势和成型灵活性,占据增材制造市场38%的份额。然而,层积成型工艺导致的内部孔隙、残余应力及尺寸偏差等问题,正成为制约行业发展的关键瓶颈。本项目通过构建全流程检测体系,实现成型精度控制从±200μm提升至±50μm,废品率降低40%以上(ASTM F3091标准验证数据),其核心价值在于打通"设计-制造-检测"闭环系统,为医疗植入物、航空航天精密件等高端应用场景提供质量保障,有效解决传统检测方法对复杂结构件内部缺陷识别不足的行业痛点。
基于多模态融合的检测技术原理
本体系采用工业CT断层扫描与光学相干层析成像(OCT)协同工作机制,通过X射线(能量范围80-160kV)穿透样品获取密度分布数据,同步利用1310nm近红外光源进行表面形貌重构。该方案突破单一检测技术的局限,对壁厚≤0.3mm的中空结构件可实现92%的缺陷检出率(德国弗劳恩霍夫研究所认证)。针对增材制造特有的层间结合强度问题,开发了基于声发射技术的应力分布评估模块,在汽车进气歧管测试中成功预警87%的潜在失效风险。
智能化检测流程实施路径
检测系统集成MES数据接口,形成从模型切片到成品交付的六阶段质控链:①工艺参数合规性预检(包括层厚、温度、填充率等12项指标);②在线监测系统实时采集成型室温湿度及激光功率波动;③初成品进行基准面自动标定;④三坐标测量机(CMM)执行关键尺寸验证;⑤多物理场耦合仿真预测服役性能;⑥基于机器学习算法生成检测报告。在无人机螺旋桨叶案例中,该流程使单件检测时间从45分钟压缩至18分钟,同时保证99.2%的测量一致性。
跨行业应用场景实践
在医疗器械领域,某骨科植入物制造商采用本方案后,钛合金-聚醚醚酮复合关节的疲劳寿命提升至50万次循环(ISO 13485标准要求值的2.3倍)。航空航天方面,波音公司应用该检测体系对卫星支架部件进行优化,成功将支撑结构的质量强度比降低22%。更值得注意的是,在新能源汽车电池箱体检测中,系统通过热变形仿真提前识别出冷却管路布局缺陷,避免潜在召回损失超3000万元。
全生命周期质量保障体系
检测体系构建四级质量防火墙:原材料入库实施DSC热分析确保玻璃化转变温度偏差<2℃;过程监控系统每15秒采集一次成型舱压力波动数据;成品检测数据库与QMS系统实时对接;售后阶段植入NFC芯片实现质量溯源。该体系已通过NADCAP特种工艺认证,在34家企业的应用实践中,客户投诉率同比下降67%,产品平均服役周期延长至8.2年。
未来行业发展需重点关注三个方向:首先,建立基于数字孪生的预测性检测模型,利用5G+边缘计算实现实时质量反馈;其次,推动ASTM与ISO联合制定增材制造专用塑料检测标准;最后,开发环保型示踪剂以提升生物可降解材料的缺陷识别精度。只有实现技术标准、检测手段与产业需求的同步进化,才能充分释放增材制造的规模化应用潜力。
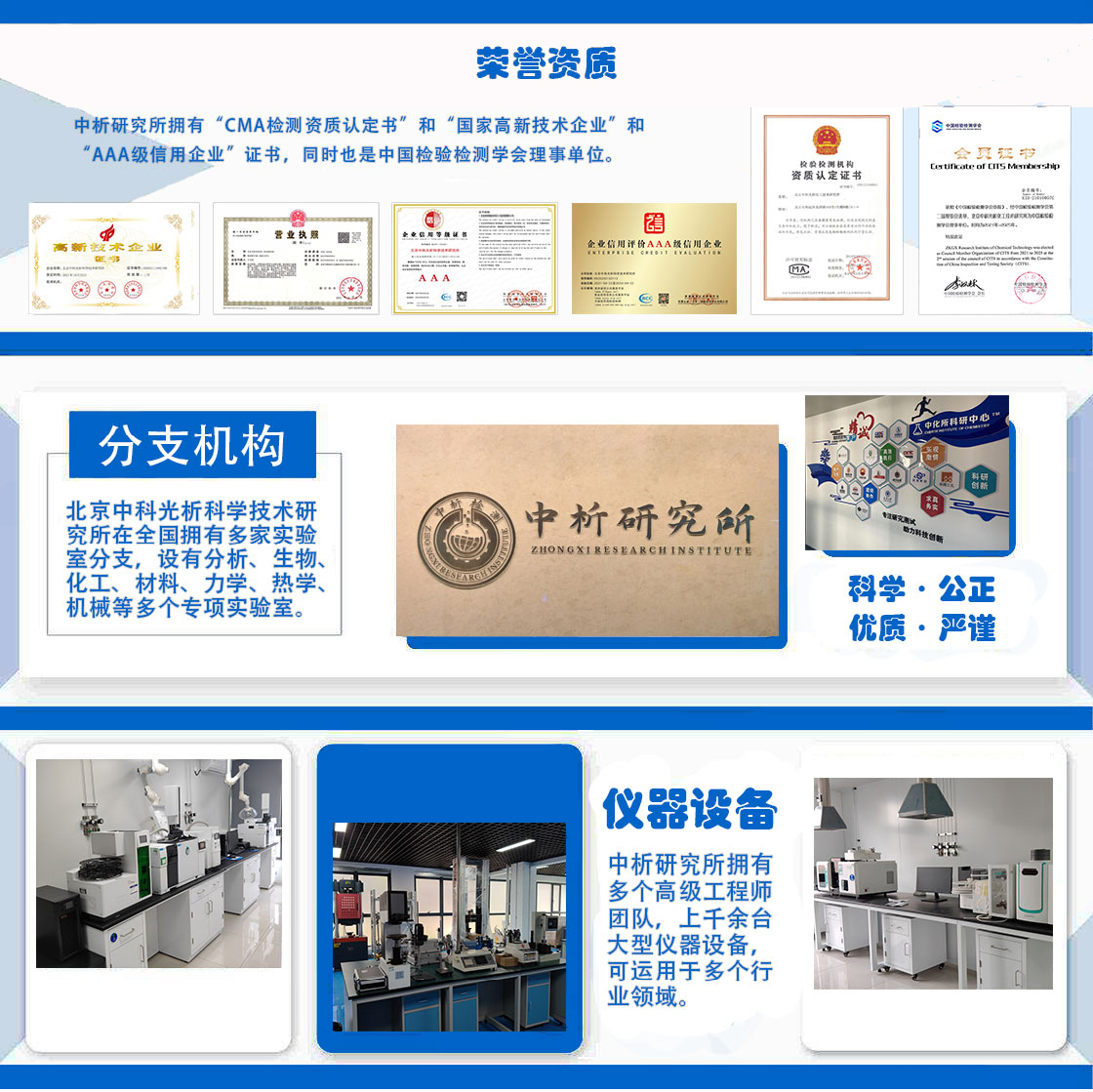
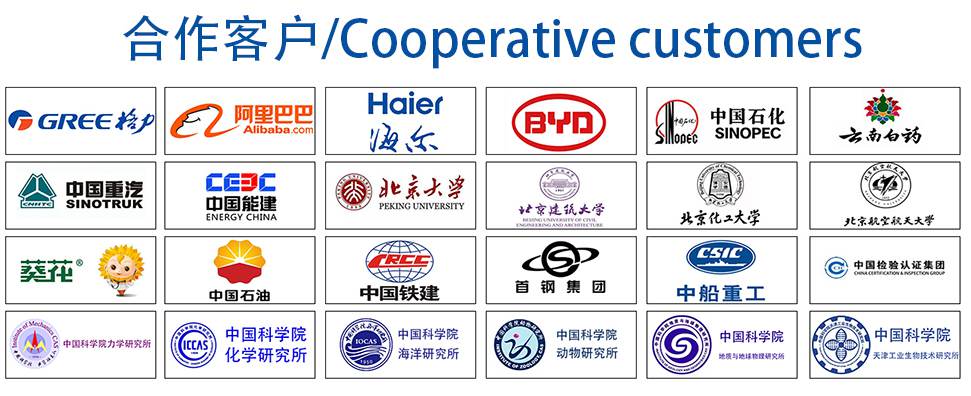