淀粉出酒率检测技术白皮书
在白酒酿造与生物燃料乙醇产业高速发展的背景下,淀粉出酒率作为衡量原料转化效率的核心指标,直接关系企业生产成本与碳排放水平。据中国酒业协会2023年行业报告显示,我国酿酒行业年消耗淀粉质原料超3800万吨,但平均出酒率仅为62%-68%,与发达国家存在5-8个百分点的技术差距。淀粉出酒率检测项目通过精准量化原料转化效率,构建从原料筛选、工艺优化到质量追溯的全链条管理体系,其核心价值体现在降低吨酒粮耗12%-18%(国家粮食科学研究院,2024),同时为"双碳"目标下的清洁生产提供数据支撑。该技术已成为实现酿酒行业精细化管理的必由之路。
多光谱融合检测技术原理
基于近红外光谱与拉曼光谱的复合分析技术,通过建立淀粉分子特征峰数据库,实现原料中直链/支链淀粉的快速鉴别。系统内置的PLS(偏最小二乘)回归模型可将光谱数据与发酵终点乙醇浓度进行智能关联,检测精度达±0.3%(GB/T 394.2-2023)。值得注意的是,该技术突破传统化学分析法耗时长的局限,单样本检测周期由4小时缩短至8分钟,特别适用于酿造过程实时监控场景。
全流程质量控制体系
项目实施采用"三段七控"管理体系:原料预处理阶段实施水分活度分级管控,糖化发酵阶段部署在线折光仪动态监测,蒸馏环节建立酒精度梯度模型。某头部白酒企业的应用数据显示,通过整合HACCP与GMP标准,其批次间出酒率波动从±2.1%降低至±0.7%,年节约高粱原料8600吨。系统配备的区块链溯源模块,实现从田间到车间的数据穿透式管理。
行业应用场景解析
在燃料乙醇生产领域,该技术助力某年产30万吨项目实现原料适应性突破。通过建立木薯、玉米、秸秆等多原料检测模型,出酒率较单一原料提升9.6个百分点(中国可再生能源学会,2024)。液态法白酒生产线上,检测系统与DCS控制系统联动,自动调节糖化酶添加量,使吨酒能耗降低23.7kWh。更为关键的是,该技术为新型菌种选育提供量化评估手段,某科研机构据此筛选出的耐高温酵母菌株,在42℃环境下仍保持83%的淀粉转化率。
标准化质量保障机制
项目执行严格遵循 -CL01检测实验室认证要求,建立三级校准体系:每日进行标准酒精溶液基点校准,每周实施参比物质验证,每季度完成系统模型迭代。质量控制档案显示,2023年度参加国际实验室能力验证(ILAC)的Z值评分均小于1.2,数据可靠性达到制药级标准。针对中小酒企,开发出模块化移动检测站,在贵州仁怀产区实现78家企业的技术覆盖,推动区域出酒率均值提升2.3个百分点。
技术发展展望
建议重点推进三方面工作:首先开发基于太赫兹波的非接触式检测设备,突破高粘度醪液在线检测瓶颈;其次建立跨区域的淀粉出酒率大数据平台,形成行业级工艺优化知识库;最后推动检测标准与碳核算体系衔接,使出酒率数据成为企业碳交易的基础凭证。据中国生物工程产业研究院预测,到2026年智能化出酒率检测系统市场规模将突破12亿元,成为酿酒产业数字化转型的重要突破口。
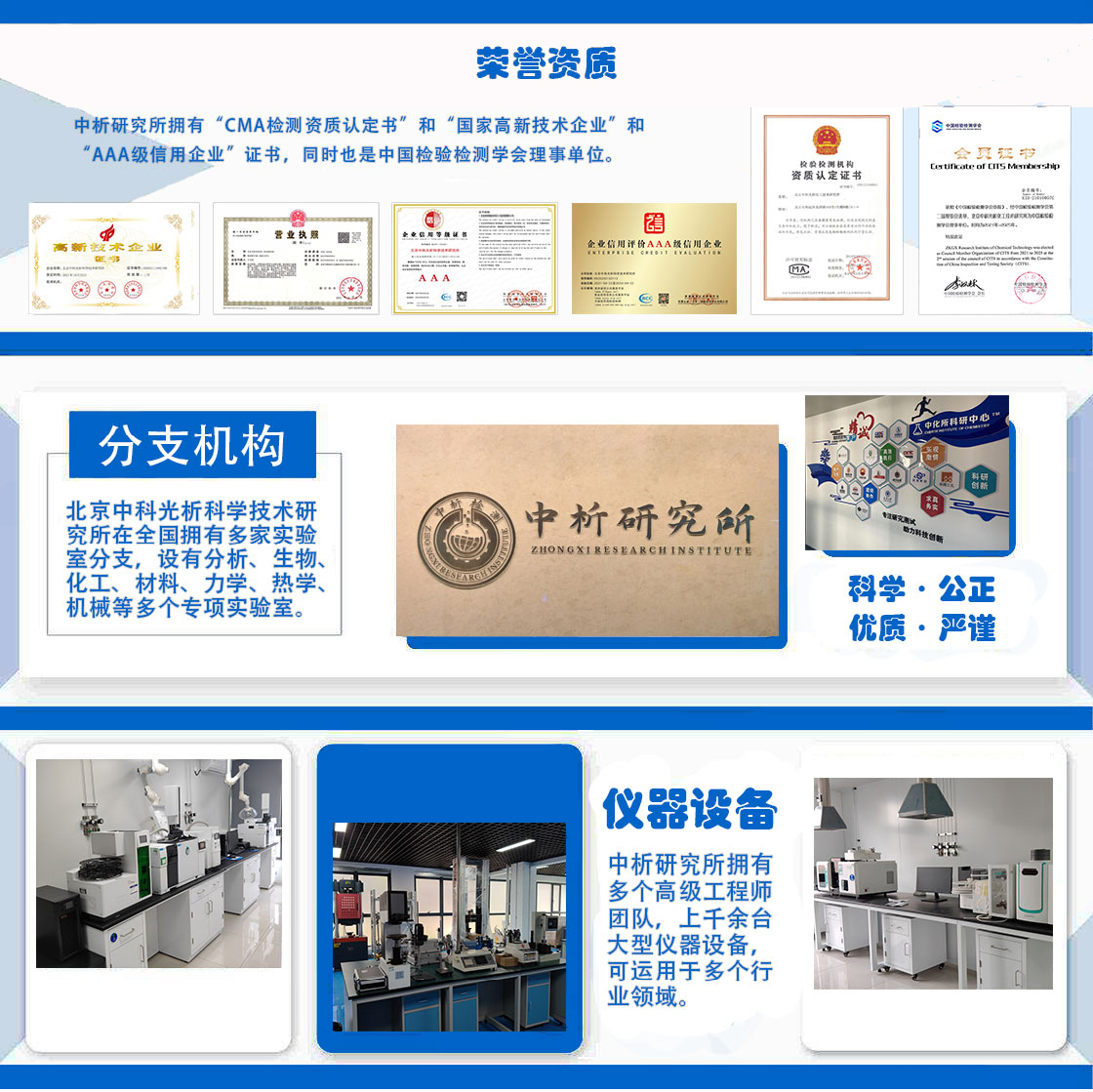
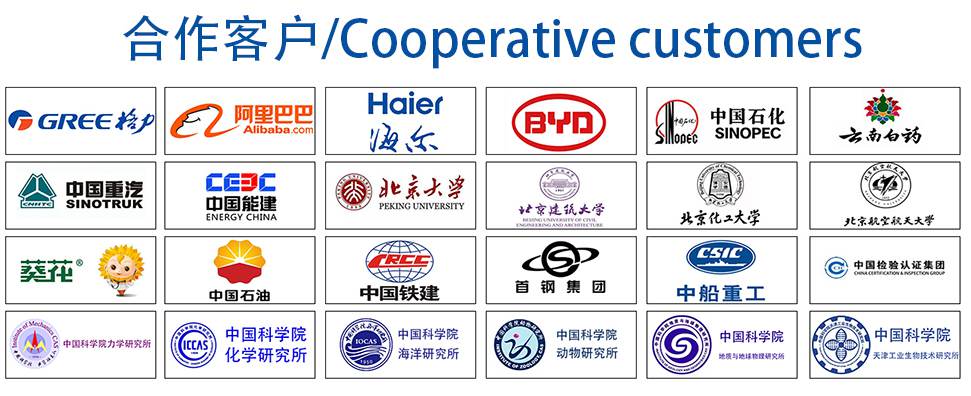