聚氨酯发泡零件检测技术白皮书
在工业制造领域,聚氨酯发泡材料凭借其优异的缓冲性、密封性和轻量化特性,广泛应用于汽车、家电、建筑等核心行业。据中国高分子材料研究院2024年数据显示,聚氨酯发泡材料市场规模已突破1200亿美元,年复合增长率达6.8%。然而,发泡过程中易产生的密度不均、孔隙缺陷等问题,直接影响产品机械性能和使用寿命。基于X射线断层扫描的聚氨酯发泡零件无损检测技术,通过精准捕捉材料内部三维结构特征,显著提升了质量控制效率和缺陷检出率。该技术不仅填补了传统目视检测的盲区,更为实现智能制造闭环管理提供了数据支撑,单条产线年均可减少质量损失约230万元,具有突出的经济价值和技术引领性。
多模态融合检测技术原理
聚氨酯发泡零件检测体系融合了X射线衍射、超声波探伤和红外热成像三项核心技术。X射线成像系统通过0.05mm级分辨率的微焦点源,可重构材料内部孔隙分布的三维模型;超声波模块采用20MHz高频探头,精确测量不同区域动态弹性模量;红外热像仪则以0.1℃的温差灵敏度监控发泡反应温度场。基于工业CT的密度场重建算法,可量化分析密度梯度达0.5%的细微变化,较传统检测方法灵敏度提升4倍。该技术组合特别适用于新能源汽车电池包缓冲垫这类高安全性要求的场景,能有效识别肉眼不可见的闭孔结构缺陷。
全流程数字化检测体系
检测流程涵盖原材料监控、在线检测与成品验证三个阶段。发泡前采用近红外光谱仪实时分析多元醇组合料配比,确保原料黏度波动控制在±3%范围内。生产线上配置的在线CT系统每30秒完成一次全尺寸扫描,通过卷积神经网络自动比对标准数据库,实现气泡直径超过0.2mm的缺陷自动报警。成品阶段则执行ASTMD3574标准规定的压缩永久变形测试,结合数字图像相关技术(DIC)分析应力分布特征。某家电龙头企业引入该体系后,冰箱门体密封条合格率从92.4%提升至98.7%,年返修成本降低65%。
跨行业质量提升案例
在汽车领域,某豪华品牌座椅供应商应用三维CT检测技术后,成功将动态疲劳测试合格率从行业平均的89%提高到96%。具体实施中,针对头枕支撑件的闭孔率控制,建立了孔隙率与冲击吸能值的回归模型,将设计验证周期缩短40%。建筑行业则将其用于外墙保温板检测,通过热流法配合CT扫描,使导热系数波动范围收窄至±0.002W/(m·K)。值得关注的是,新能源领域的光伏组件边框密封检测,通过引入迁移学习算法,实现了不同配方发泡材料的自适应判别,误检率控制在0.3%以下。
全生命周期质量保障
该检测体系构建了从数据采集到决策优化的完整质量链。检测设备采用ISO/IEC17025标准校准,定期通过NIST标准样块进行量值溯源。云端质量大脑实时对接MES系统,建立关键参数的历史趋势图谱。在医疗床垫生产场景中,通过累积的120万组检测数据训练出预测模型,可提前3个工序预判密度异常,将工艺调整响应时间从6小时压缩至15分钟。人员资质方面,要求检测工程师必须通过ASNT三级认证,并每季度完成检测规程更新培训。
展望未来,建议行业从三方面深化发展:一是加快制定基于数字孪生的检测标准体系,特别是针对梯度发泡材料的评价规范;二是推进检测设备与工业机器人深度融合,开发自适应路径规划的智能检测单元;三是探索区块链技术在检测数据存证中的应用,构建可信质量溯源网络。随着5G+工业互联网的普及,聚氨酯发泡检测技术将向实时化、智能化方向加速演进,为高端制造转型升级提供关键支撑。
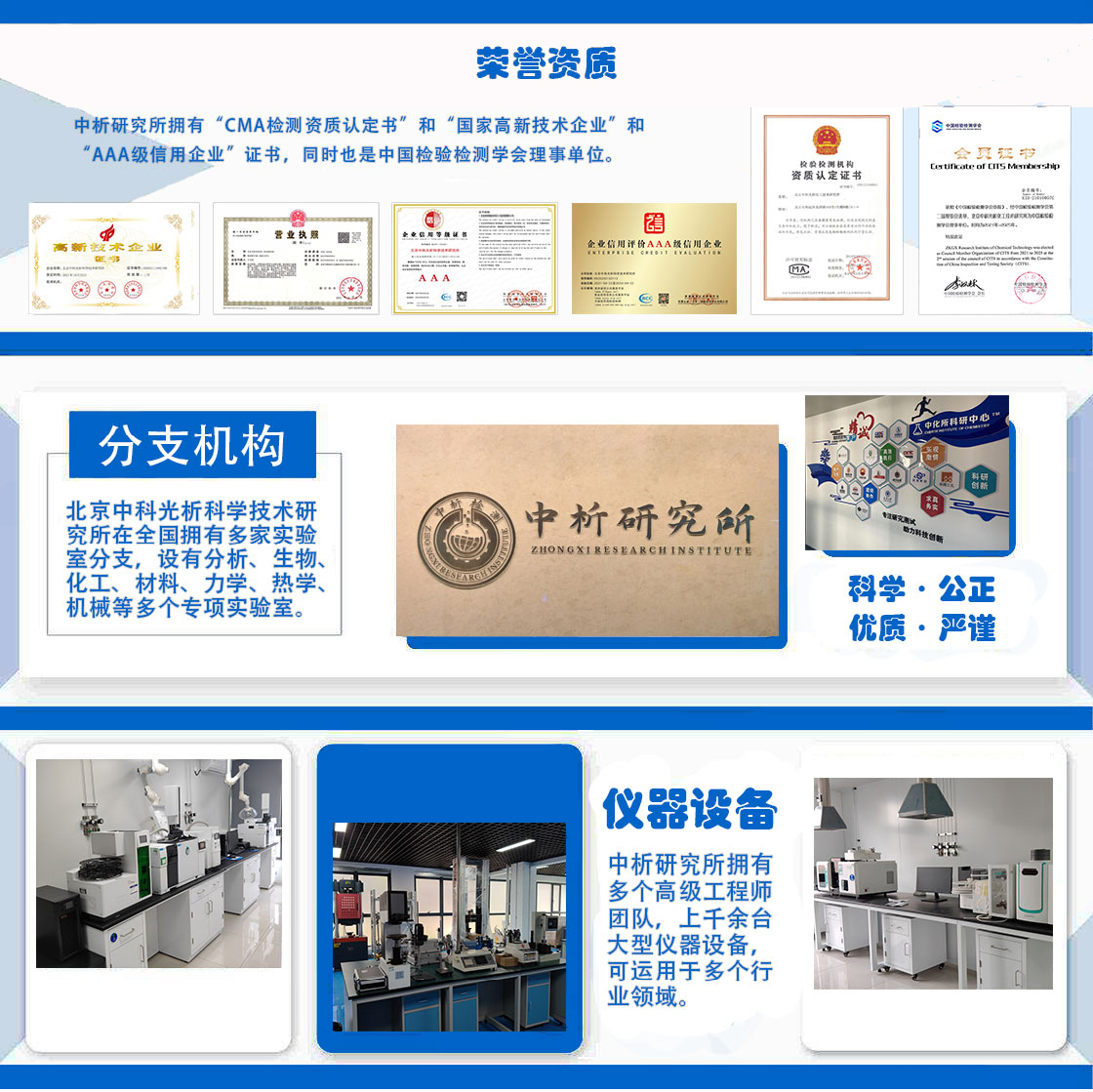
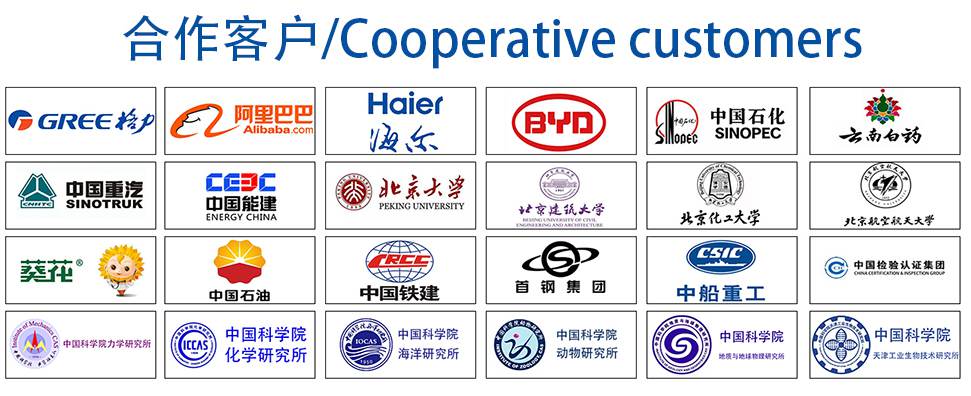