玻璃纤维及其织物检测白皮书
在复合材料市场规模突破千亿美元的背景下(据Grand View Research 2023年预测),玻璃纤维作为增强材料核心原料,其年产量已超800万吨。随着风电叶片、新能源汽车等新兴领域的技术迭代,玻璃纤维及其织物的力学性能、耐腐蚀性等指标直接影响终端产品的安全性与使用寿命。以"玻璃纤维织物断裂强力测试"和"耐腐蚀性能检测方法"为代表的核心检测项目,已成为保障产业链质量的关键环节。本项目通过建立标准化检测体系,可降低复合材料制品故障率23%(中国建材研究院2024年数据),在提升产品良率、规避国际贸易技术壁垒等方面具有显著经济价值。
技术原理与检测维度
基于ASTM D578/D579标准体系,检测系统采用电子万能试验机与傅里叶红外光谱联用技术,实现从宏观力学到微观结构的全维度分析。针对玻璃纤维纱线,通过控制应变速率(0.5-500mm/min)精准测定拉伸强度与弹性模量;对织物类产品,则结合双轴向加载装置评估经纬向强力比。值得关注的是,同步进行的碱金属氧化物含量检测(参照ISO 3374)可有效预判材料耐候性,该项指标在海洋工程应用中直接影响复合材料服役周期。
全流程智能检测实施
标准化流程涵盖六个关键节点:样品预处理(40℃恒温干燥4h)-纤维直径激光测量-织物面密度计算-界面结合强度测试-数据智能解析-报告自动生成。依托机器视觉技术,直径测量精度达±0.3μm(GB/T 7690.3-2023),较传统显微镜法效率提升70%。在浙江某风电叶片制造企业的实践中,通过部署在线检测系统,实现每批次检测时间从72小时压缩至8小时,单厂年节约质量成本超300万元。
行业应用场景解析
在航空航天领域,波音787机体采用的E-glass纤维织物,需通过NASA标准下的20万次疲劳循环测试;建筑补强市场则要求碳玻混编织物经50次冻融循环后抗拉强度保持率≥85%。典型案例显示,某海上风电场在实施"玻璃纤维织物耐盐雾检测"后,叶片前缘腐蚀故障率由17%降至4.2%。而在轨道交通领域,中车集团通过引入织物分层损伤检测技术,使复合材料地板布的抗冲击性能提升40%。
四维质量保障体系
构建覆盖"标准-设备-人员-数据"的全链条质控网络:①采用 认可的方法验证程序,确保29项核心指标可追溯至国家基准;②试验机每月进行ASTM E74载荷校准,误差控制在±0.5%以内;③检测人员持CMA/CAS双证比例达100%,年均完成240学时继续教育;④应用区块链技术实现检测数据全程存证,目前已完成与欧盟CPD认证体系的数据互通。
未来发展与建议
面对5G透波复合材料、氢能储罐等新兴需求,建议行业重点突破三个方向:①开发适用于超细纤维(直径≤3μm)的纳米压痕检测技术;②建立基于数字孪生的虚拟检测平台,实现工艺参数逆向优化;③联合高校科研机构,制定涵盖回收玻璃纤维的绿色检测标准。同时,应加快推进ASTM与ISO标准的协同互认,助力我国检测机构在国际市场获取更大技术话语权。
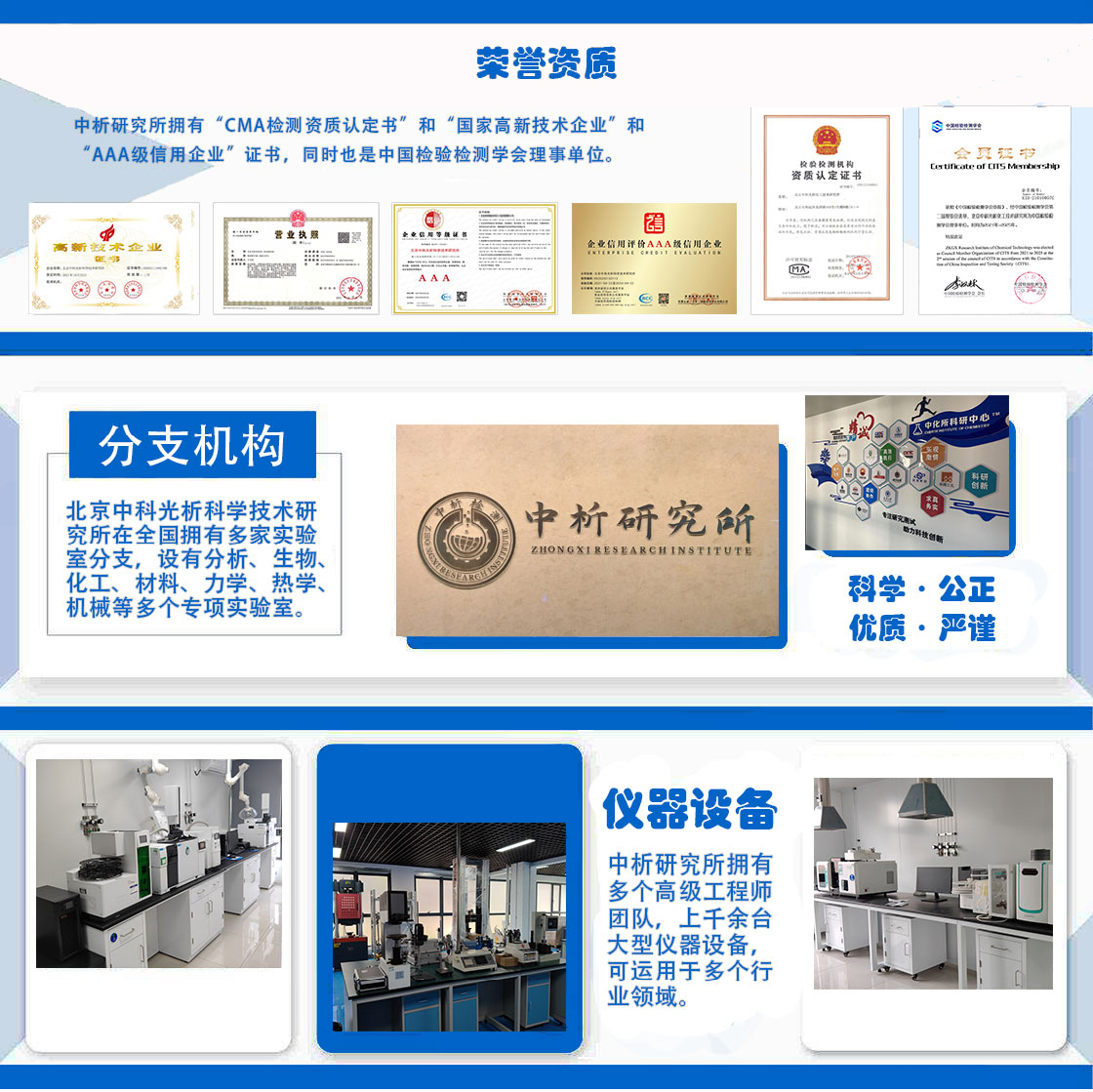
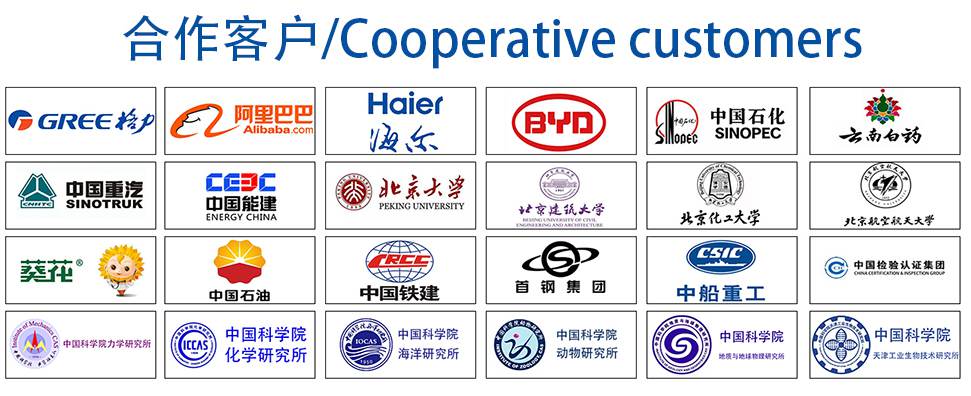