一、外观及基础结构检测
-
- 检查控制箱外壳是否存在变形、锈蚀、裂纹等机械损伤
- 验证防爆标识、铭牌参数(压力等级、型号等)是否清晰可辨
- 确认各操作手柄、按钮无卡阻,标识清晰
-
- 检查液压管线接头、法兰连接处是否紧固,无渗漏痕迹
- 检测管线固定支架是否牢固,避免振动导致松动
- 观察管汇内部通道是否存在异物堵塞或腐蚀沉积
二、液压系统专项检测
-
- 油位检查:使用油标尺确认液压油量在标准范围内(通常为油箱容积的80%)
- 油质分析:取样检测油液粘度、含水量(需≤0.1%)、污染度(NAS等级≤8级)
- 油温监控:运行状态下油温应≤60℃,异常升温需排查泵组或阀件故障
-
- 测试液压泵输出压力是否达到设计值(常规范围14-21MPa)
- 验证节流阀开度与液压缸行程的同步精度(误差≤±5%)
- 检测蓄能器预充压力(通常为系统压力的70%)
三、仪表与传感器校验
-
- 对比主控压力表与标准表的读数偏差(允许误差≤±2.5%)
- 检测压力变送器输出信号(4-20mA)与实时压力的线性关系
-
- 模拟液位变化验证传感器响应灵敏度
- 使用恒温槽校准温度传感器的测量精度(误差≤±1.5℃)
四、控制系统功能测试
-
- 模拟井涌工况,测试节流阀自动开启/关闭响应时间(≤3秒)
- 验证PID调节器对压力波动的控制稳定性(超调量≤5%)
-
- 切断电源后,手动操作液压先导阀是否可正常切换节流状态
- 检测备用手动泵的建压能力(30秒内达到10MPa)
五、密封性与耐压试验
-
- 以1.5倍额定工作压力(如35MPa)保压30分钟,压降≤1%
- 使用泡沫剂或氦质谱仪检测阀座、阀杆等动密封点泄漏率
-
- 模拟实际工况进行500次以上启闭循环,监测密封件磨损情况
- 记录每次循环后的压力保持曲线,评估系统疲劳性能
六、环境适应性检测
-
- 在-20℃至+60℃环境箱中测试液压油流动性及密封件弹性
- 验证仪表显示在极端温度下的数据稳定性
-
- 检查隔爆面间隙是否符合GB 3836标准(≤0.15mm)
- 检测本安电路与非本安电路的隔离有效性
七、检测周期与标准依据
- 常规检测:每6个月进行功能性检测,每年开展全面检测
- 大修检测:累计工作3000小时或经历重大工况后强制检测
- 执行标准:API 16C、SY/T 5323-2016《节流压井管汇》
注意事项
- 检测前需彻底泄压,执行能量隔离程序(LOTO)
- 更换密封件时必须使用原厂指定材质(如氟橡胶、聚四氟乙烯)
- 检测数据需录入设备健康管理系统,建立全生命周期档案
上一篇:压裂酸化用粘土稳定剂检测下一篇:油管转换接头检测
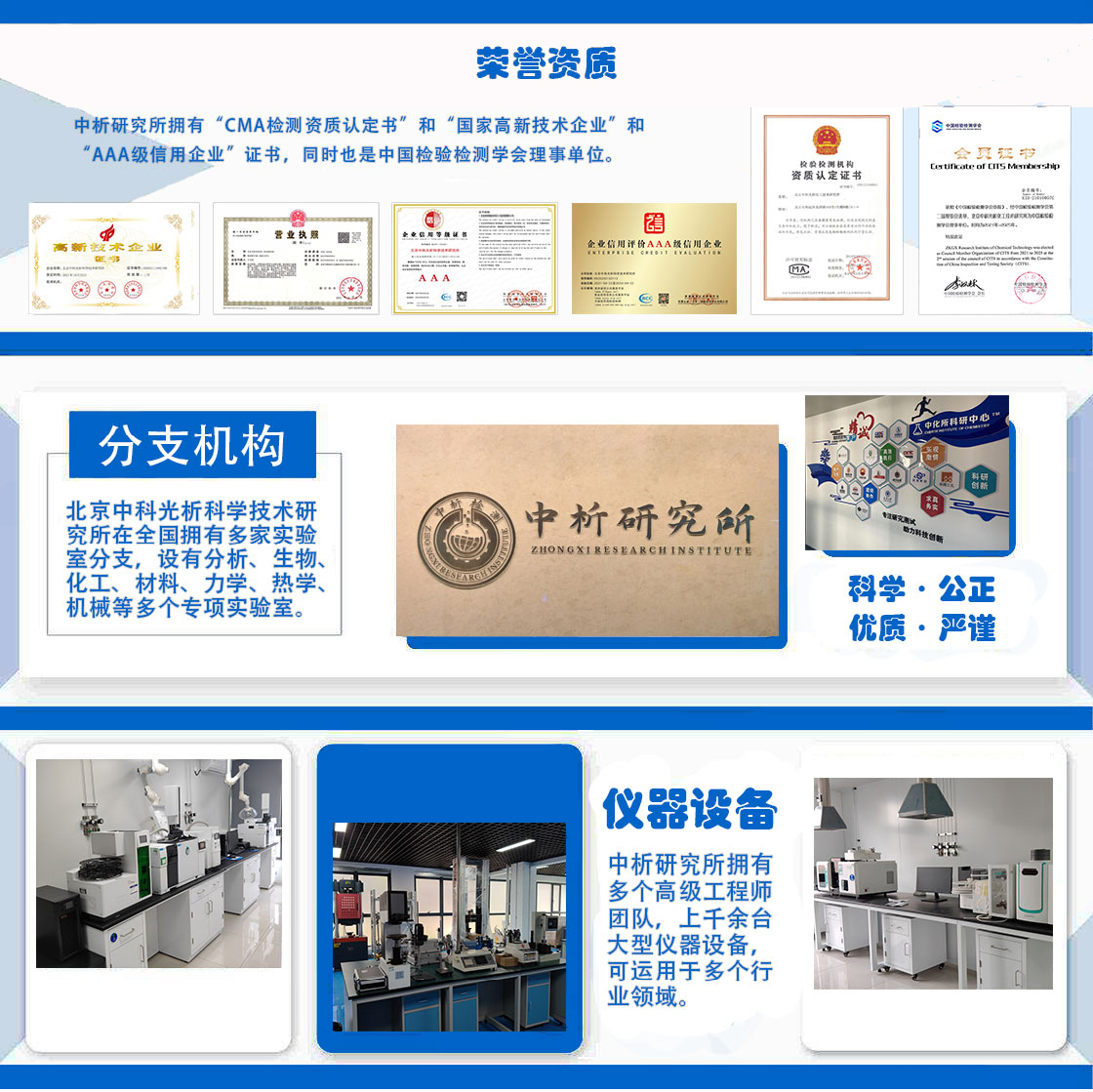
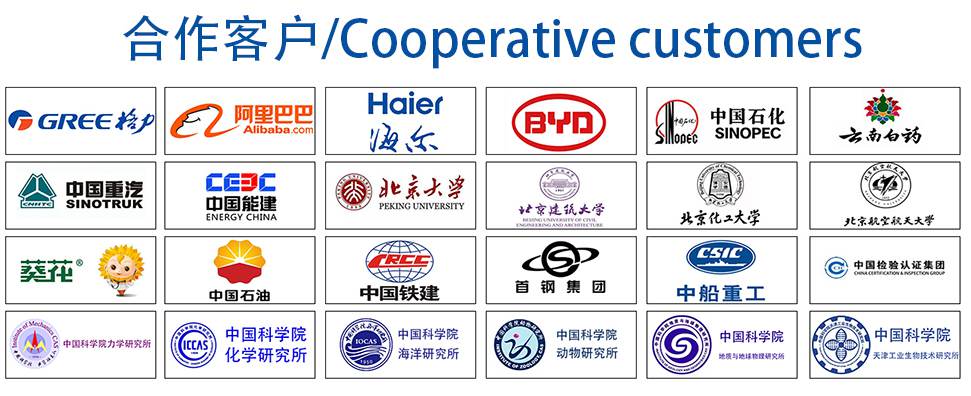
材料实验室
热门检测
271
228
202
211
210
215
225
218
228
229
215
214
219
216
210
205
222
207
220
214
推荐检测
联系电话
400-635-0567