高温联箱检测的重要性及核心项目
在火力发电、石油化工、冶金等工业领域,高温联箱作为连接锅炉、压力容器等设备的关键部件,长期承受高温、高压及复杂介质的冲击。其结构完整性和运行可靠性直接关系到设备安全与生产效率。若联箱出现裂纹、腐蚀或变形等问题,可能导致泄漏甚至爆炸事故,造成严重经济损失和安全隐患。因此,定期开展高温联箱检测是工业设备维护中不可或缺的环节。
高温联箱核心检测项目解析
1. 材质劣化检测
通过光谱分析、硬度测试和金相检验,评估联箱材料在高温环境下的组织变化(如珠光体球化、碳化物析出等),判断材料强度退化程度。同时需检测氧化皮厚度,避免因氧化导致壁厚减薄。
2. 焊缝无损检测(NDT)
采用超声波检测(UT)探伤技术扫描焊缝内部缺陷,配合磁粉检测(MT)或渗透检测(PT)定位表面裂纹。重点关注管座角焊缝、对接焊缝等应力集中区域,发现未熔合、气孔等隐患。
3. 几何尺寸测量
使用激光扫描或3D建模技术获取联箱本体及法兰的变形量数据,检测椭圆度、同心度偏差是否超标。同时测量壁厚减薄率,通过多点测厚验证设计余量是否满足安全运行要求。
4. 热应力分布分析
采用红外热像仪监测运行状态下的温度场分布,结合有限元模拟计算热应力集中区域。重点关注温度梯度突变部位,预防因热疲劳导致的蠕变损伤。
5. 内窥镜检查
针对无法拆卸的联箱内部结构,使用柔性内窥镜观测集箱内壁腐蚀状况、沉积物堆积情况,评估介质冲刷对管孔边缘的影响,同时检查内部支撑件完整性。
检测标准与周期规划
检测需遵循ASME B31.1、GB/T 16507等标准规范,结合设备运行参数制定检测策略。常规检测周期为3-5年,对于超临界参数机组或频繁启停设备,应缩短至1-2年。检测数据需与历史记录对比分析,建立全生命周期健康档案。
结语
高温联箱检测需融合多学科技术手段,结合智能诊断系统实现精准评估。通过科学的检测体系,可有效延长设备使用寿命,为工业装置的安全经济运行提供保障。
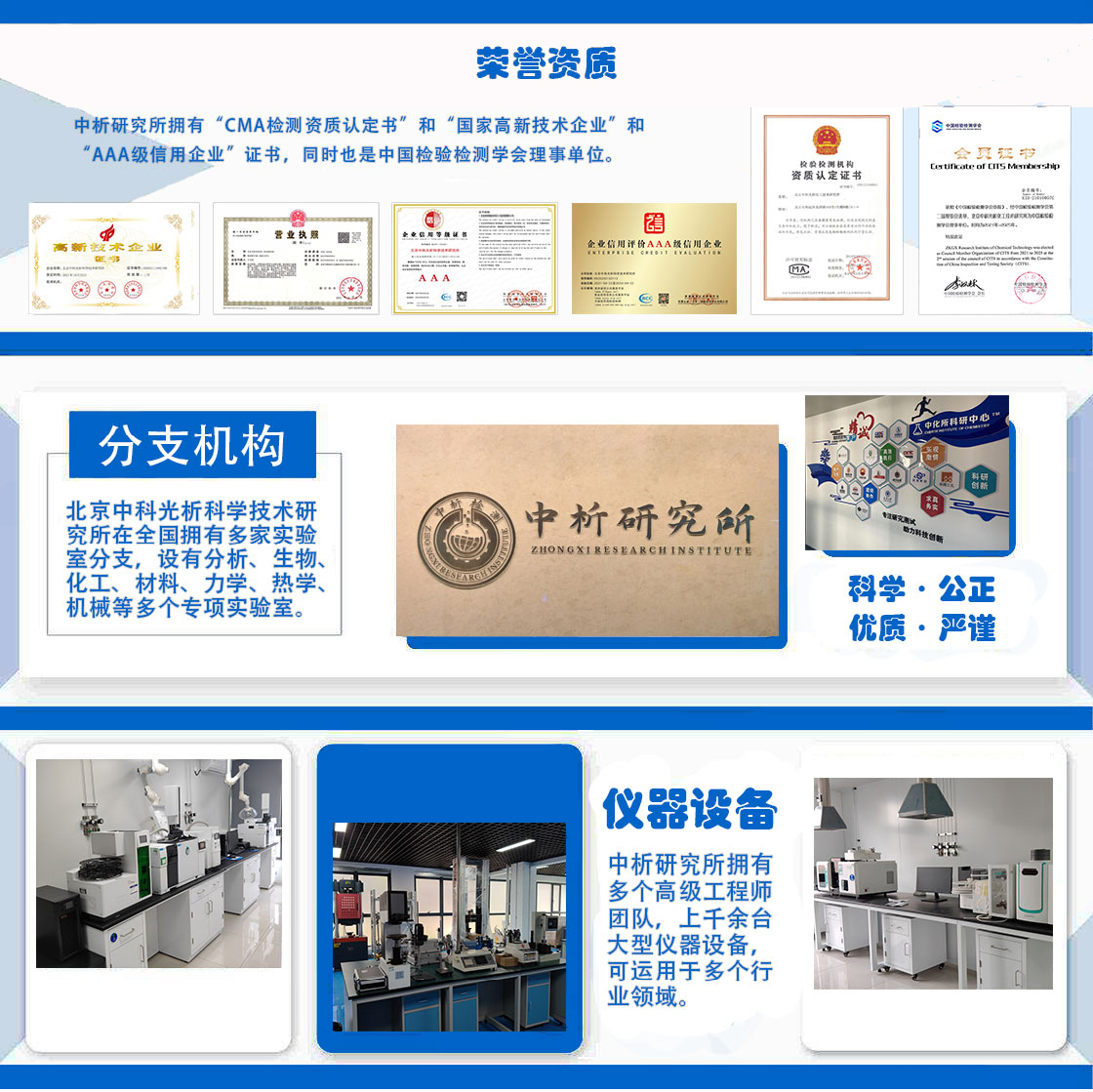
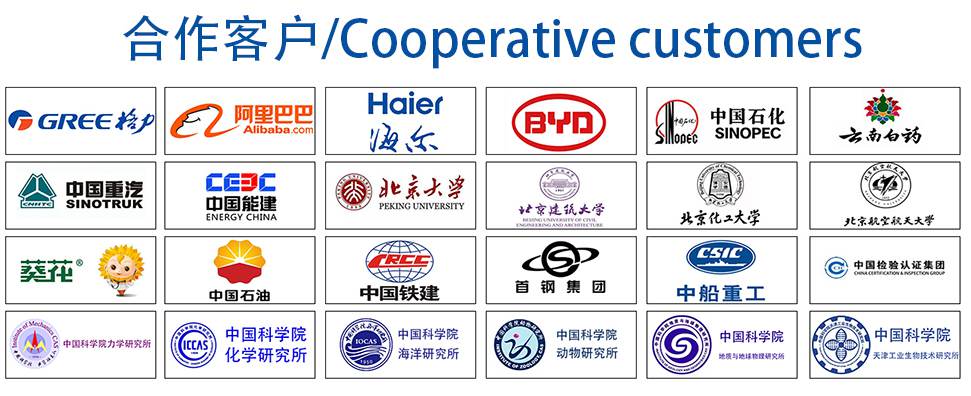