单转子反击式破碎机检测项目详解
单转子反击式破碎机作为中碎和细碎领域的关键设备,广泛应用于矿山、建材、化工等行业。其核心工作原理是通过高速旋转的转子带动板锤冲击物料,结合反击板的碰撞与反击作用实现破碎。由于设备长期处于高负荷、强冲击的工况下,定期开展系统性检测是保障生产效率、延长设备寿命、预防突发故障的必要措施。检测内容需覆盖机械结构、动力系统、磨损部件及安全防护等多个维度,具体检测项目如下:
一、转子系统检测
转子是单转子反击式破碎机的核心动力部件。检测重点包括: 1. 转子动平衡测试:通过振动分析仪监测转子高速旋转时的振动幅度,确保动平衡误差在允许范围内(通常≤0.2mm/s),避免因不平衡引发轴承磨损或整机共振。 2. 主轴弯曲度检测:使用百分表测量主轴径向跳动量,标准值应小于0.05mm/m,超差需校直或更换。 3. 板锤固定装置状态检查:确认螺栓预紧力是否符合设计值(通常使用扭矩扳手校准),防止板锤松动引发飞锤事故。
二、板锤与反击板磨损检测
磨损部件的状态直接影响破碎效率和能耗: 1. 板锤厚度测量:采用卡尺或激光测厚仪定期检测,当单侧磨损量超过原始尺寸的30%时需更换或调面使用。 2. 反击板间隙校准:通过调整螺栓控制反击板与转子间距,确保初级破碎腔间隙在30-50mm,二次破碎腔15-30mm,并检查反击板衬板的裂纹情况。 3. 耐磨材料硬度抽检:对高铬铸铁材质的板锤进行洛氏硬度测试(HRC≥58),避免因材质不达标导致异常磨损。
三、轴承与润滑系统检测
轴承故障是设备停机的主要原因之一,需重点关注: 1. 轴承温度监测:红外测温仪连续监测运行温度,正常工作温度应≤75℃,异常升温需立即停机排查。 2. 润滑油状态分析:定期取样检测润滑油的粘度、水分含量及金属微粒浓度,及时更换变质油品(建议每500小时过滤一次,2000小时全面更换)。 3. 轴承游隙测量:使用塞尺检测圆柱滚子轴承的径向游隙,标准值为0.05-0.15mm,超差需调整预紧力或更换轴承。
四、结构与安全防护检测
整机结构完整性直接影响生产安全: 1. 机壳裂纹检查:通过渗透探伤法检测焊接部位及应力集中区的微裂纹,特别关注进料口周边区域的疲劳损伤。 2. 液压开启装置测试:模拟检修工况操作液压系统,确认反击板开启角度是否达到120°以上,液压缸保压时间应≥30分钟无泄漏。 3. 安全联锁功能验证:检查门盖开启时设备能否自动断电,并测试过铁保护装置的反应灵敏度(金属探测器报警后设备应在0.5秒内停机)。
通过上述检测项目的系统实施,可有效提升单转子反击式破碎机的运行可靠性。建议结合设备使用手册制定周期性检测计划,并建立完整的检测档案,为预防性维护提供数据支撑。特别是在连续高负荷运行后,应增加振动频谱分析和润滑油铁谱检测等深度诊断项目,以实现从“事后维修”到“预测性维护”的升级。
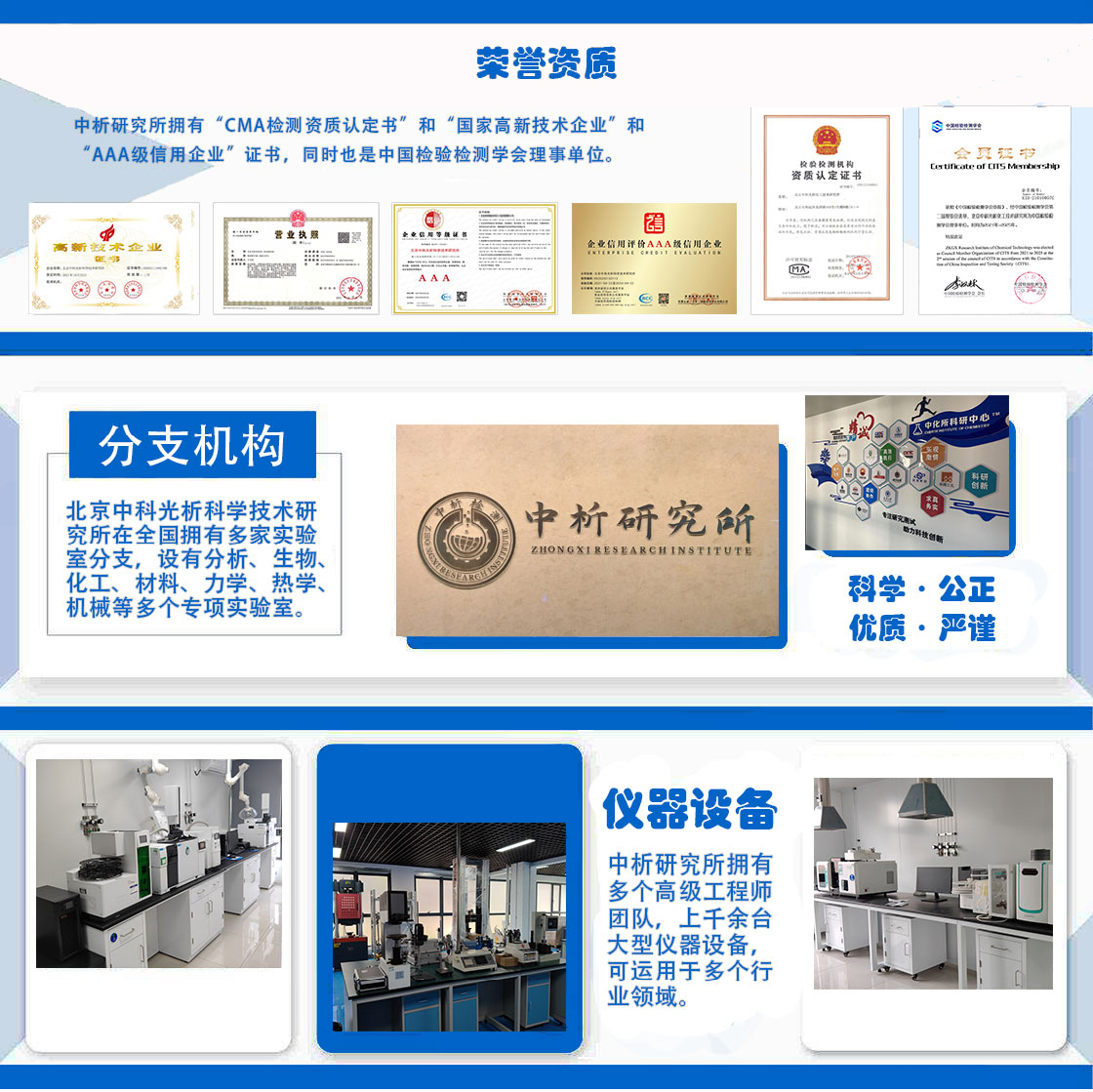
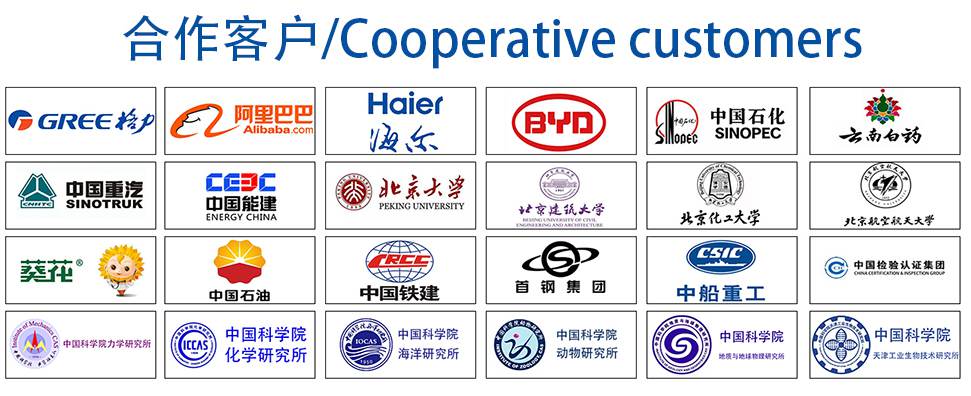