天然气过滤器滤芯检测的重要性与核心内容
在天然气输送与处理系统中,过滤器滤芯是保障燃气纯度、防止杂质损坏下游设备的核心组件。其功能在于拦截颗粒物、液态水、油污及其他污染物,确保燃气符合工艺要求。然而,随着使用时间的增加,滤芯可能因杂质堆积、材料老化或机械损伤导致性能下降,轻则降低过滤效率,重则引发系统压差过大甚至破裂风险。因此,定期开展滤芯检测是保障天然气设备安全运行、延长滤芯使用寿命的关键环节。
滤芯检测的主要项目及实施方法
1. 外观完整性检测
通过目视检查或电子成像设备(如工业内窥镜)观测滤芯表面是否存在破损、变形、划痕或焊接点开裂。重点检查折叠层结构是否均匀,支撑网架有无腐蚀,并记录污染物附着分布情况。对于金属烧结滤芯,需额外确认孔隙连通性是否正常。
2. 过滤精度测试
采用粒子计数法或重量法验证滤芯的截留能力。通过向滤芯上游注入特定粒径的标准测试粉尘(如ISO 12103-A3),下游取样分析残留颗粒物浓度,判断其是否达到标称精度(如5μm、10μm)。此项目需结合流量参数模拟实际工况。
3. 压差性能评估
在额定流量下测量滤芯的初始压差与饱和压差。通过对比新滤芯基准值,判断污染物堵塞程度及结构是否异常。若运行压差超过设计值的1.5倍,则需立即更换。测试时需使用经过校准的差压表,并记录温度、流量等环境参数。
4. 材料耐腐蚀性分析
对滤芯金属部件(如不锈钢骨架)进行化学成分检测与金相观察,评估硫化氢、二氧化碳等介质引起的点蚀、晶间腐蚀风险。非金属材料(如聚酯纤维)需进行溶胀试验与抗老化测试,确保其在高压、温变环境中的稳定性。
5. 清洁度与污染物分析
通过超声波清洗、溶剂萃取等方式收集滤芯截留的污染物,采用光谱仪(如ICP-OES)分析重金属含量,显微镜观察颗粒物形态,判断污染物来源(如管道锈蚀、压缩机润滑油残留等),为优化过滤系统提供数据支持。
检测周期与结果应用
建议根据天然气气质报告、设备运行时长(通常500-2000小时)及压差变化趋势制定检测计划。检测结果应形成包含缺陷图谱、性能曲线、材料退化评级的综合报告,作为滤芯更换、维修或系统改进的依据。对于多次检测数据异常的滤芯批次,需追溯供应商生产工艺质量。
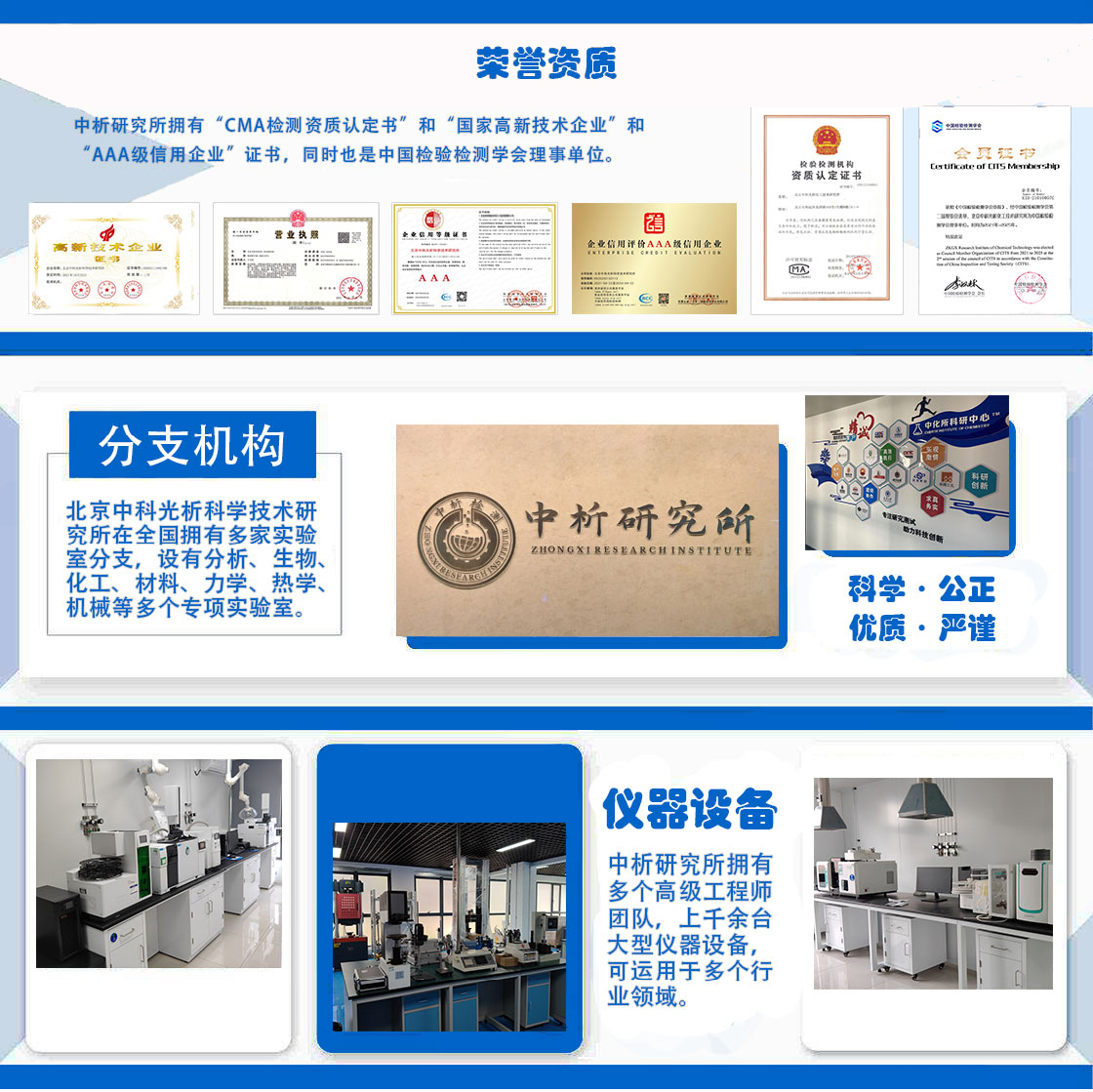
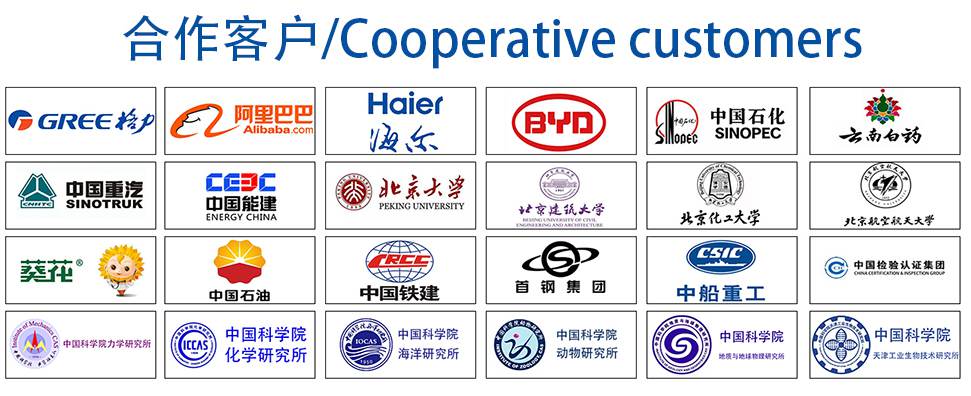