铝合金覆盖层检测的重要性与技术要求
铝合金因其轻量化、耐腐蚀和优异的机械性能,被广泛应用于航空航天、汽车制造、建筑装饰及电子设备等领域。为提升铝合金零件的表面性能,常通过阳极氧化、电镀、喷涂等工艺形成功能性覆盖层。这些覆盖层的质量直接影响产品的使用寿命和可靠性,因此需通过系统性检测确保其符合技术标准。铝合金覆盖层检测涵盖物理性能、化学成分、耐环境性等多个维度,是产品质量控制的核心环节。
关键检测项目及方法
1. 覆盖层厚度检测
采用涡流测厚仪、X射线荧光光谱仪或金相显微镜法,依据ISO 2360、ASTM B244等标准,测量阳极氧化膜或涂层厚度。厚度不足可能导致耐蚀性下降,过厚则可能影响装配精度。
2. 附着力测试
通过划格法(ASTM D3359)、拉开法(ISO 4624)评估涂层与基体的结合强度。采用胶带剥离后观察脱落面积,或使用液压装置测量剥离力,确保覆盖层在机械应力下不脱落。
3. 耐腐蚀性能检测
执行盐雾试验(ASTM B117)、湿热试验(GB/T 2423.3)等加速老化实验,评估覆盖层在模拟恶劣环境中的防护能力。配合电化学阻抗谱(EIS)分析可量化耐蚀性指标。
4. 成分分析与均匀性检测
利用能谱仪(EDS)、X射线光电子能谱(XPS)分析覆盖层元素组成,验证工艺参数是否符合设计要求。通过显微硬度计(HV)多点测试,确认膜层成分分布均匀性。
5. 表面形貌与孔隙率检测
采用扫描电镜(SEM)观察覆盖层微观结构,识别裂纹、孔洞等缺陷。使用铁氰化钾点滴法(ISO 2932)测定阳极氧化膜的封孔质量,孔隙率需控制在0.5%以下。
6. 耐磨性与硬度测试
依据Taber磨耗试验(ASTM D4060)评估涂层抗磨损能力,显微硬度计测量膜层硬度(通常要求阳极氧化膜HV≥300)。高硬度可有效防止表面划伤和机械磨损。
7. 颜色与光泽度检测
使用分光光度计(ASTM E308)量化色差(ΔE≤1.5为合格),光泽度仪测量60°入射角反射率。对于装饰性涂层,需确保批次间外观一致性。
综合检测方案的意义
完整的铝合金覆盖层检测需结合具体应用场景制定方案。例如汽车部件侧重耐盐雾和耐磨性,电子散热器则需保证导热性与绝缘涂层完整性。通过多维度检测数据,可优化工艺参数、降低失效风险,同时满足ISO 9001、IATF 16949等质量管理体系要求。定期检测与大数据分析还能为产品寿命预测提供科学依据,推动铝合金表面处理技术的持续改进。
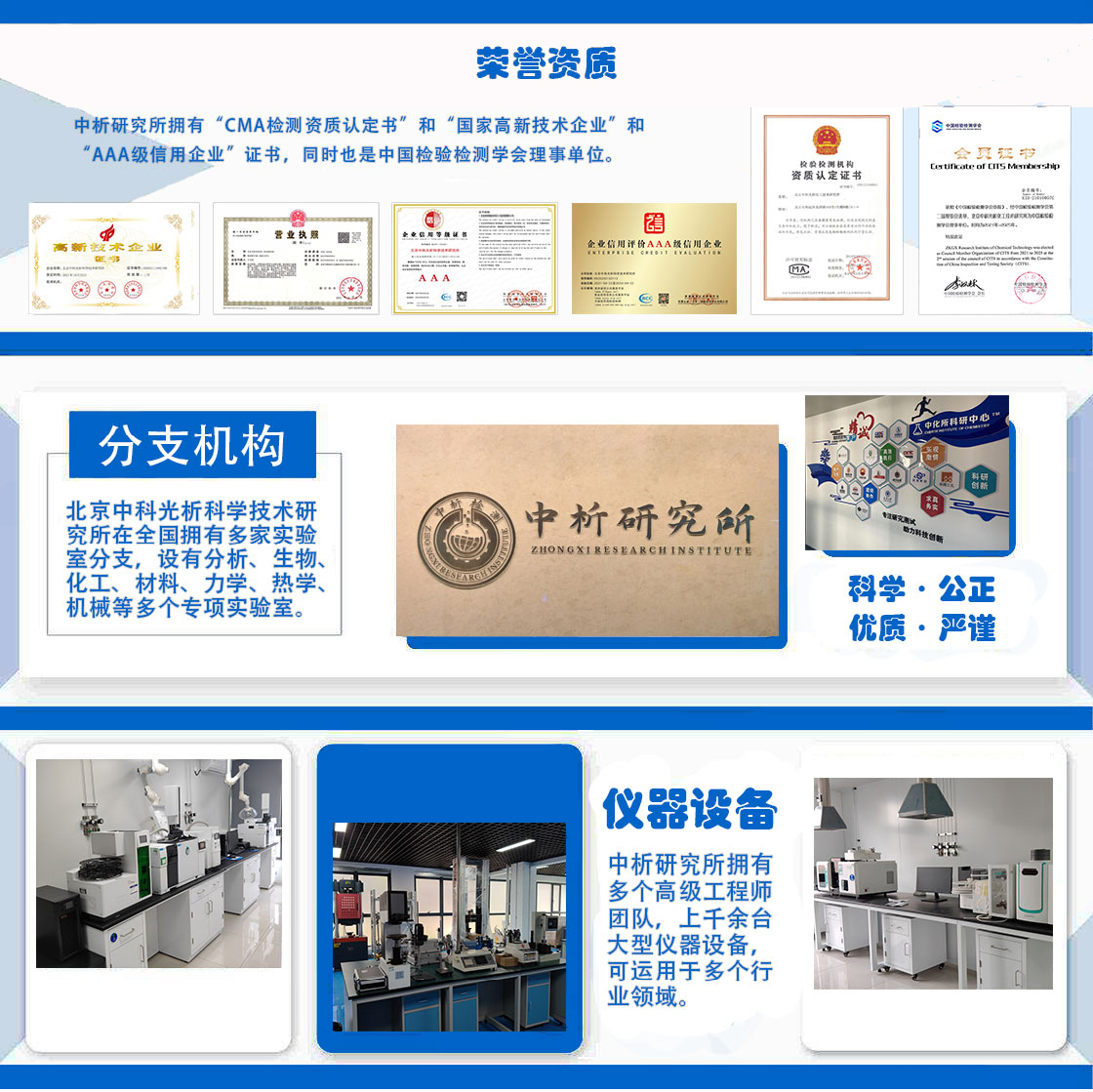
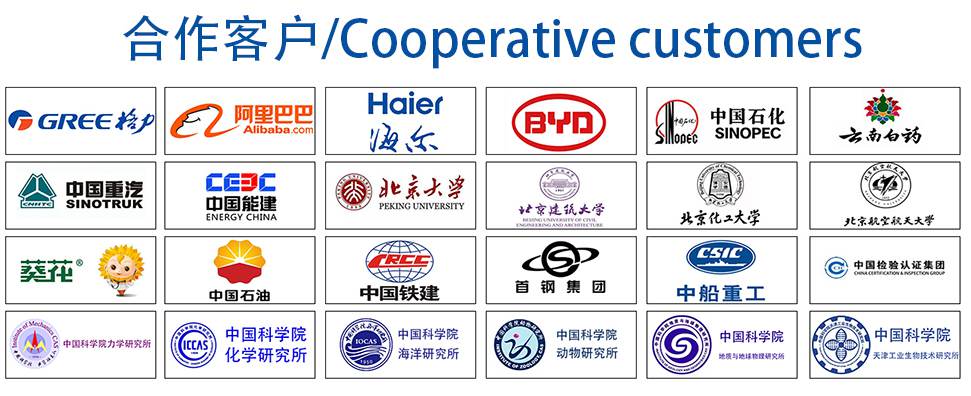