动车组用铝及铝合金型材检测的重要性
动车组作为高速铁路的核心装备,其轻量化、安全性及耐久性直接关系列车的运行效率和乘客安全。铝及铝合金型材凭借其高比强度、耐腐蚀性和易加工性,成为动车组车体、转向架和内部结构的关键材料。然而,材料性能的微小偏差可能导致严重的安全隐患,因此对铝及铝合金型材进行系统化检测是生产制造和质量控制中不可或缺的环节。本文将从化学成分、力学性能、表面质量等多个维度,详细阐述动车组用铝及铝合金型材的检测项目及技术要求。
关键检测项目及方法
1. 化学成分分析
通过光谱分析法(如OES)精准测定铝材中镁、硅、铜、锌等元素的含量,确保符合GB/T 3190-2020《变形铝及铝合金化学成分》标准。重点关注杂质元素(如铁)的限量,以避免影响材料的焊接性能和耐蚀性。
2. 力学性能测试
包括拉伸试验(检测抗拉强度、屈服强度、延伸率)、硬度测试(布氏/维氏硬度)及冲击韧性试验。依据TB/T 3267-2019《动车组用铝合金挤压型材》要求,型材纵向抗拉强度需≥240MPa,延伸率≥8%。
3. 尺寸与形位公差检测
使用三坐标测量仪、激光扫描仪等设备对型材截面尺寸、直线度、平面度进行全尺寸检验。重点控制壁厚均匀性,偏差需≤±0.2mm,避免装配应力集中。
4. 表面质量评估
通过目视检测结合电子显微镜观察,检查氧化膜厚度(≥10μm)、表面划痕、气泡等缺陷。采用涡流探伤技术检测皮下裂纹,确保表面粗糙度Ra≤1.6μm。
5. 耐腐蚀性能试验
进行盐雾试验(按GB/T 10125标准)、晶间腐蚀试验(硝酸法)和应力腐蚀开裂测试,评估材料在复杂环境下的抗腐蚀能力。要求盐雾试验480小时后无红锈,腐蚀深度≤0.1mm。
6. 无损检测
采用超声波探伤(UT)检测内部裂纹、夹杂等缺陷,渗透检测(PT)辅助验证表面开口缺陷。根据EN 12223标准,缺陷当量直径需≤1mm且间距≥50mm。
7. 金相组织分析
通过金相显微镜观察晶粒度(需达到5-8级)、第二相分布及热处理均匀性,确保材料微观组织符合TB/T 3267规定的等轴细晶要求。
8. 疲劳性能测试
模拟动车组实际运行载荷(频率5-30Hz),进行轴向疲劳试验。要求型材在2×10^6次循环载荷下无裂纹萌生,安全系数不低于1.5。
结语
动车组用铝及铝合金型材的检测体系需贯穿原材料入厂、生产过程及成品验收全过程。通过建立多维度的检测数据档案,结合数字化质量管理系统,可有效保障材料性能的稳定性和可追溯性,为高速列车的安全运营提供坚实的材料基础。
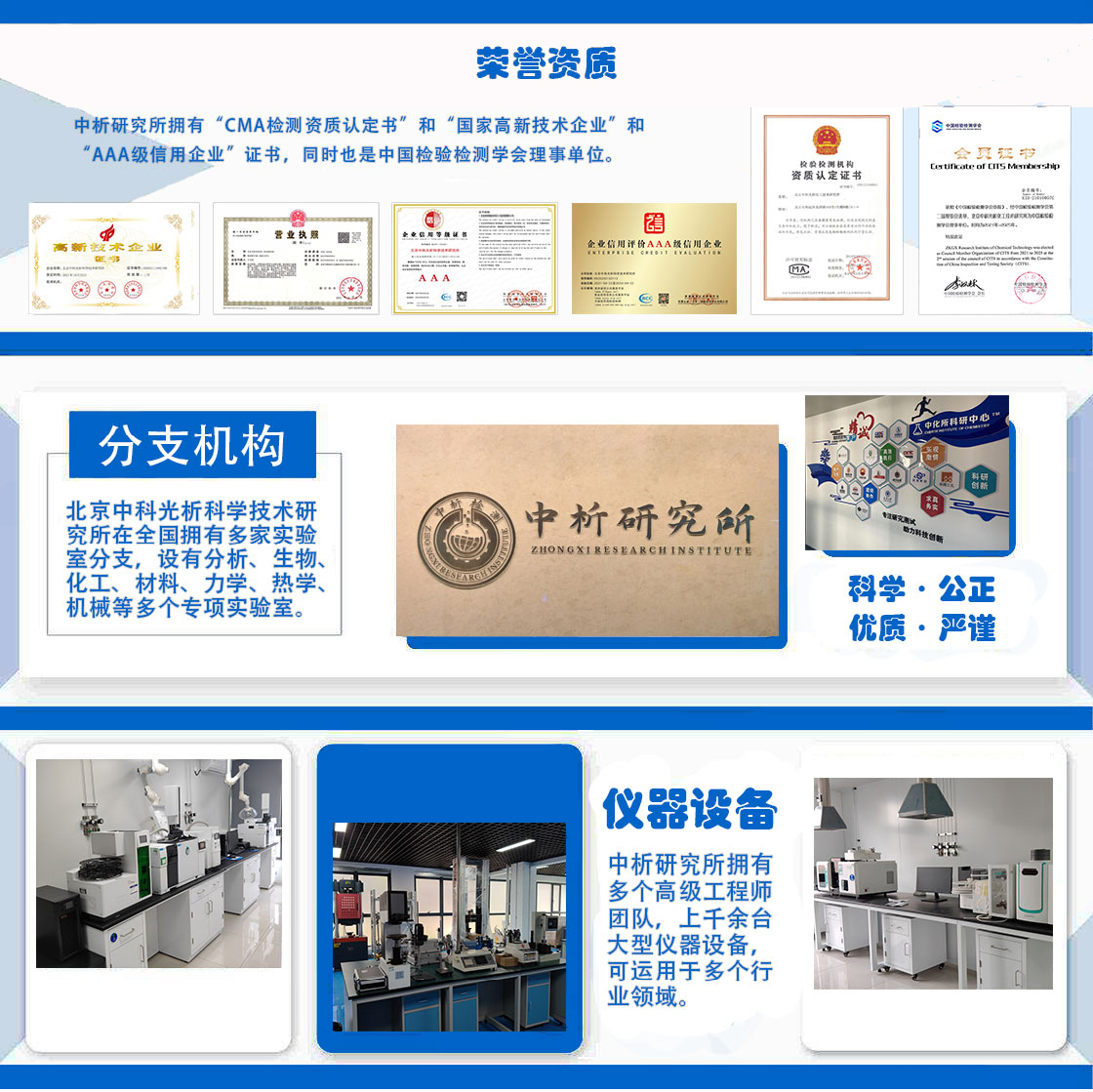
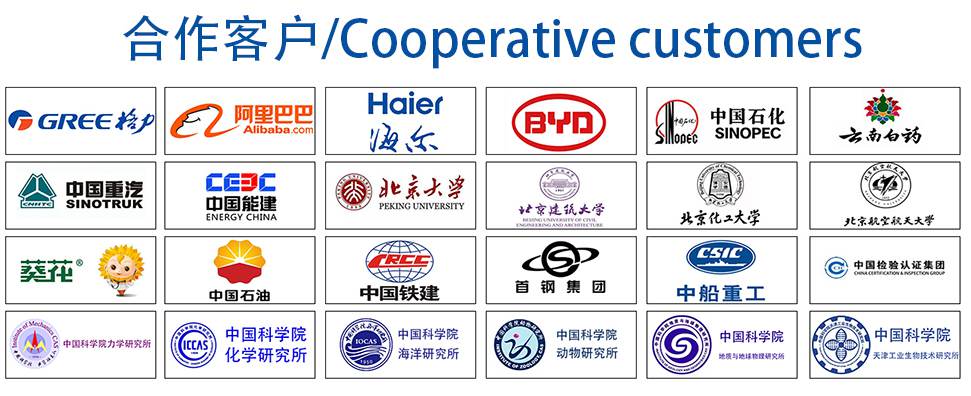