固体氧化剂检测的重要性与技术要点
固体氧化剂是化工、冶金、航天等领域中不可或缺的化学品,其通过释放活性氧促进其他物质氧化反应。然而,由于氧化剂的强氧化性和潜在危险性,对其物理化学性质、纯度及安全性能的精准检测至关重要。近年来,因氧化剂储存不当或质量不达标引发的事故屡见不鲜,例如运输过程中的自燃爆炸、生产环节的意外反应等。因此,建立科学规范的检测体系已成为保障安全生产和合规应用的核心环节。
主要检测项目及技术方法
1. 物理性质检测
通过激光粒度仪测定固体氧化剂的粒径分布,使用振实密度仪分析堆积密度,同时结合SEM扫描电镜观察微观形貌。这些参数直接影响氧化剂的反应速率和储存稳定性,例如高比表面积的粉体更易发生吸湿结块。
2. 化学成分分析
采用X射线荧光光谱(XRF)测定主成分含量,结合ICP-OES检测重金属杂质。对于高氯酸盐类氧化剂,需重点监测氯酸盐/亚氯酸盐的残留量,避免分解风险。红外光谱(FTIR)可有效鉴别晶型结构差异。
3. 氧化性能测试
通过氧弹量热法测定有效氧含量,利用DSC差示扫描量热仪分析热分解特性。特殊场景下需模拟实际工况,例如在密闭容器中开展燃烧速度测试,评估其作为推进剂的能量释放效率。
4. 安全性能评估
包含撞击感度测试(采用BAM落锤仪)、摩擦感度测试(使用Julius Peters装置)及热稳定性试验(80℃热储存观察)。依据UN标准开展自反应性物质分类测试,包括时间/压力试验和自加速分解温度(SADT)测定。
质量控制与标准体系
检测过程需严格遵循GB/T 23942-2009《固体氧化剂分类试验方法》、联合国《关于危险货物运输的建议书》等标准。针对军工、民用等不同应用场景,需分别满足GJB 5891-2006航天推进剂要求或HG/T 4068工业级过氧化物规范。
检测技术发展趋势
智能化检测设备的应用显著提升效率,如基于机器视觉的晶型识别系统可实现快速分选。微反应量热技术(μRC)的引入使热危险性评估更加精准。未来将加强原位检测技术开发,实现生产过程中的实时质量监控。
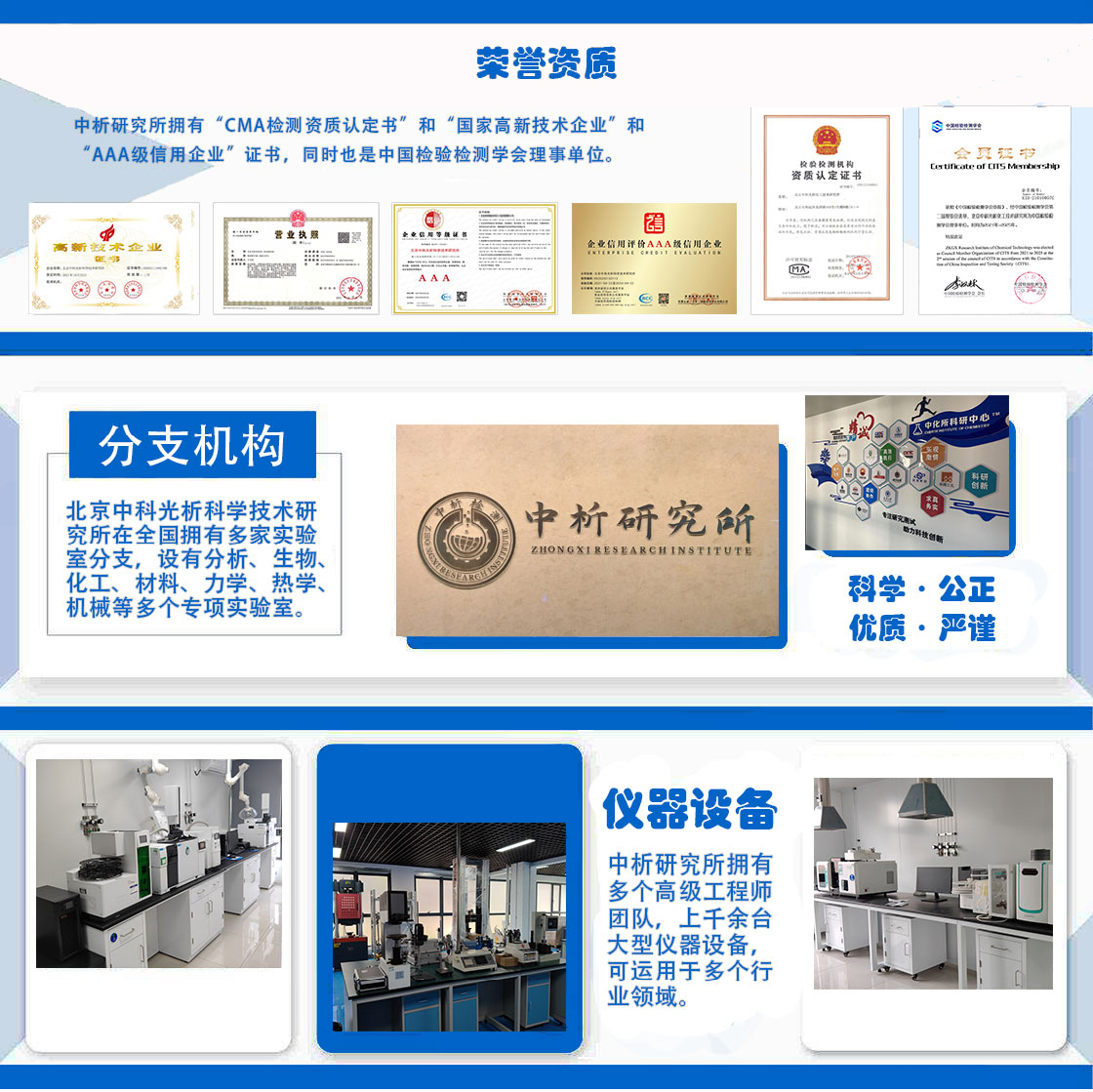
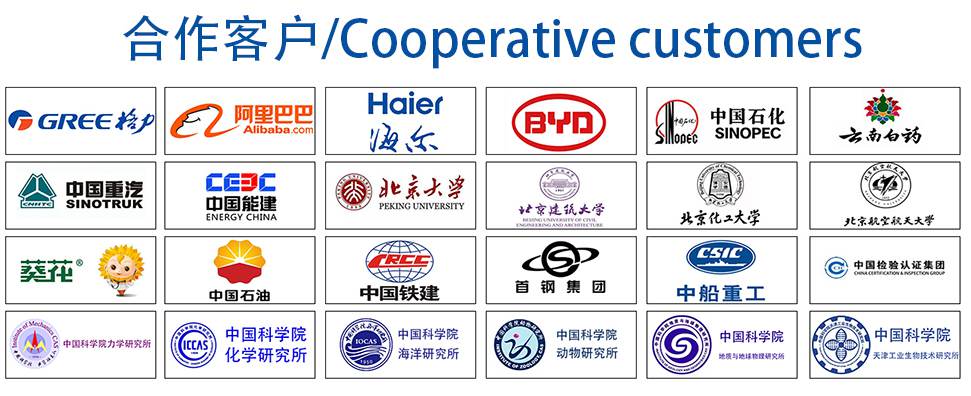