石墨球检测的核心内容与应用领域
石墨球检测是冶金、铸造、材料科学等领域中一项重要的质量控制技术,尤其在球墨铸铁生产过程中具有关键意义。石墨的形态、分布和尺寸直接决定了材料的力学性能(如抗拉强度、延伸率)和加工特性。通过系统化的石墨球检测,能够评估铸铁件的微观结构是否符合工艺设计要求,避免因石墨形态异常(如片状、蠕虫状)导致的产品失效。近年来,随着汽车工业、工程机械对轻量化与高强材料需求增长,石墨球检测的精度与技术手段也在不断升级,覆盖从实验室分析到工业现场快速检测的多场景应用。
石墨球检测的主要项目及技术方法
1. 石墨球尺寸分布分析
通过金相显微镜或扫描电镜(SEM)观察样品截面,测量石墨球直径并统计分布范围。通常要求球径在5-50μm之间,且75%以上石墨球达到6级以上球化率(依据GB/T 9441标准)。自动化图像分析系统可快速计算平均粒径、面积占比等参数。
2. 石墨球形态评估
采用球化率分级法(Ⅰ-Ⅵ级)或形状因子计算(如圆度、长宽比)量化球形度。完整球形(Ⅵ级)对应圆度>0.8,而蠕虫状石墨圆度通常低于0.6。ASTM A247标准提供了典型的石墨形态比对图谱。
3. 石墨球数量密度检测
单位面积内石墨球数量反映凝固过程的形核条件,直接影响材料韧性。检测时需选取典型视场(至少5个),统计每平方毫米石墨球数量,通常控制在100-500个/mm²范围。
4. 基体与界面结合分析
利用显微硬度计测试石墨/金属界面过渡区性能,同时观察是否存在缩松、夹杂等缺陷。电子探针(EPMA)可进一步分析界面处的元素偏析情况。
5. 化学成分关联性检测
通过光谱仪测定C、Si、Mg、RE(稀土)等关键元素含量,结合热分析仪监控冷却曲线,建立成分-球化效果的定量关系模型。例如镁残留量需控制在0.03%-0.06%以确保球化稳定性。
齐全检测技术发展趋势
随着人工智能技术的渗透,基于深度学习的石墨球自动识别系统已实现秒级完成形态分类与统计。同步辐射CT技术可三维重建石墨空间分布,而激光诱导击穿光谱(LIBS)支持原位成分快速检测。这些技术的集成应用显著提升了检测效率与数据可靠性,推动球墨铸铁工艺向智能化方向发展。
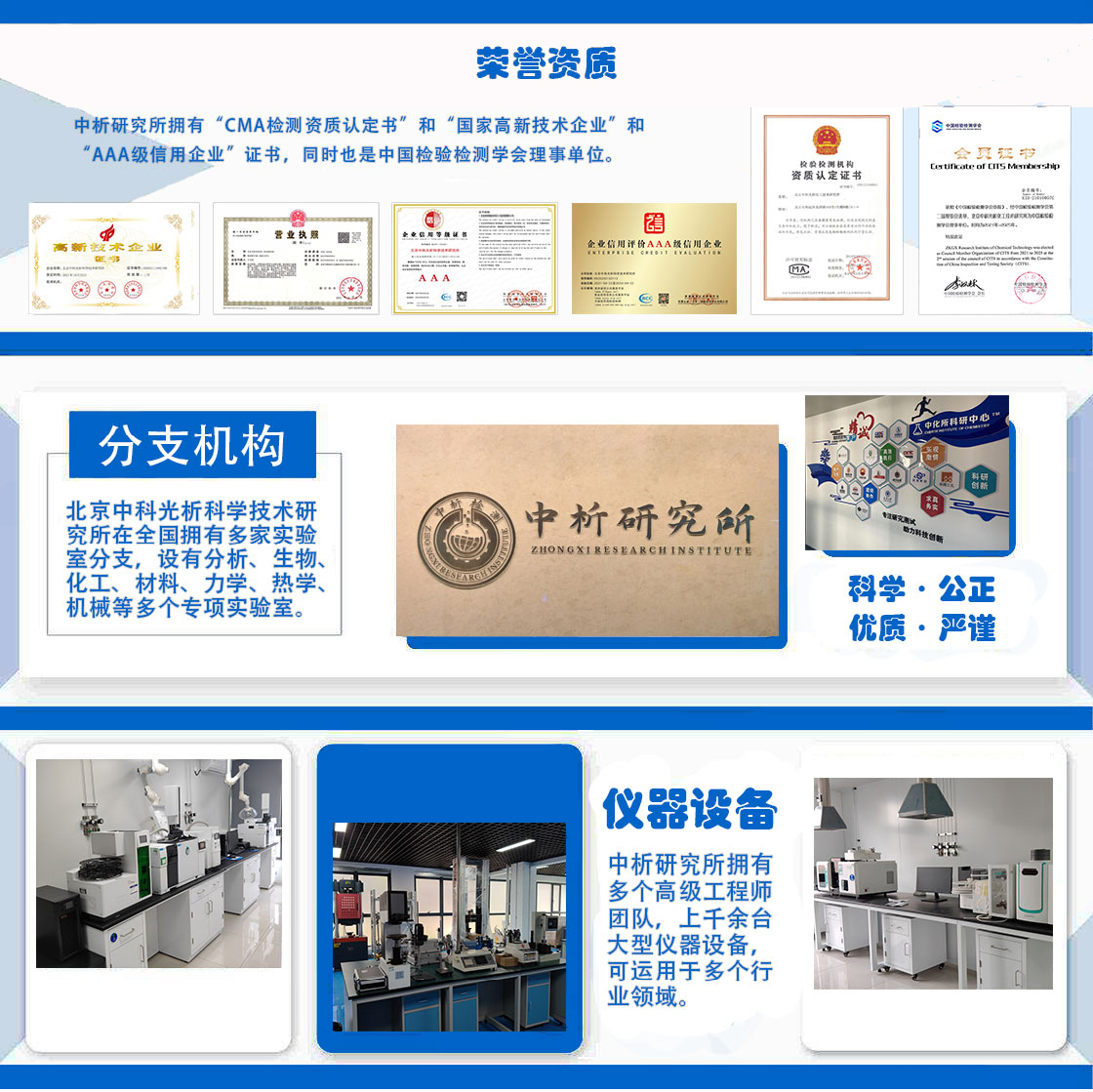
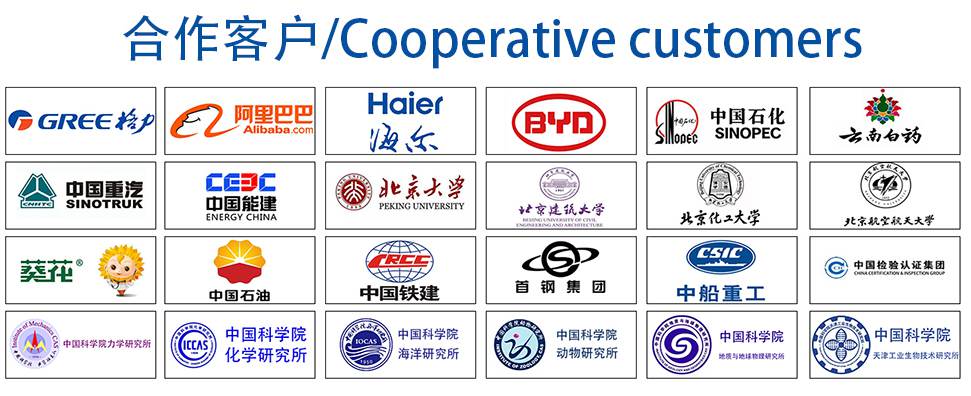