汽车发动机配件检测的重要性
作为汽车的核心动力单元,发动机的性能直接影响车辆的安全性、燃油经济性和使用寿命。随着车辆使用时间的增长,发动机配件的磨损、老化以及装配误差等问题会逐渐显现,导致动力下降、油耗升高甚至故障频发。因此,定期对发动机核心配件进行系统性检测,是保障车辆运行稳定性和延长发动机寿命的关键环节。专业检测不仅能发现潜在隐患,还能通过数据量化评估配件状态,为维修或更换提供科学依据。
主要检测项目及方法
1. 曲轴与连杆机构检测
通过三坐标测量仪检测曲轴的同轴度、圆度及轴颈磨损量,使用磁粉探伤法检查表面裂纹;对连杆进行垂直度检测和弯曲变形分析,确保其在高温高压环境下的结构完整性。
2. 气缸与活塞组件检测
采用内径千分尺测量气缸内壁的椭圆度和锥度,使用气缸压力表测试压缩比;通过活塞环间隙规检测环槽间隙,并利用电子显微镜观察活塞顶部的积碳分布情况,评估燃烧室工作状态。
3. 润滑系统配件检测
通过油压测试仪验证机油泵输出压力,检查油道是否堵塞;对机油滤清器进行压差试验,评估过滤效率;使用光谱分析仪检测机油金属颗粒含量,判断发动机内部磨损程度。
4. 冷却系统配件检测
利用超声波测厚仪检查水泵叶轮腐蚀情况,使用流量计测试散热器管路流通效率;通过压力扫描阀检测节温器开启温度,并采用红外热成像仪分析水套温度分布的均匀性。
5. 燃油喷射系统检测
使用喷油器试验台验证喷油嘴雾化效果和喷射量精度,通过示波器分析高压油泵压力波形;对ECU控制信号进行动态测试,确保喷油正时与发动机工况精准匹配。
智能化检测技术应用
随着AI和物联网技术的发展,发动机配件检测已逐步实现数字化升级。例如采用工业CT扫描构建三维模型分析内部缺陷,通过振动频谱分析预判轴承磨损趋势,以及基于大数据建立配件寿命预测模型。这些技术大幅提高了检测效率和诊断准确性,为预防性维修提供了强有力的技术支持。
结语
科学系统的发动机配件检测不仅能降低突发故障风险,更能通过数据驱动实现精准维保。建议车主每2万公里或按厂商要求进行专业检测,尤其对于涡轮增压器、正时链条等关键部件需重点关注。通过结合传统检测手段与新兴智能技术,可有效延长发动机使用寿命,保障行车安全与环保合规性。
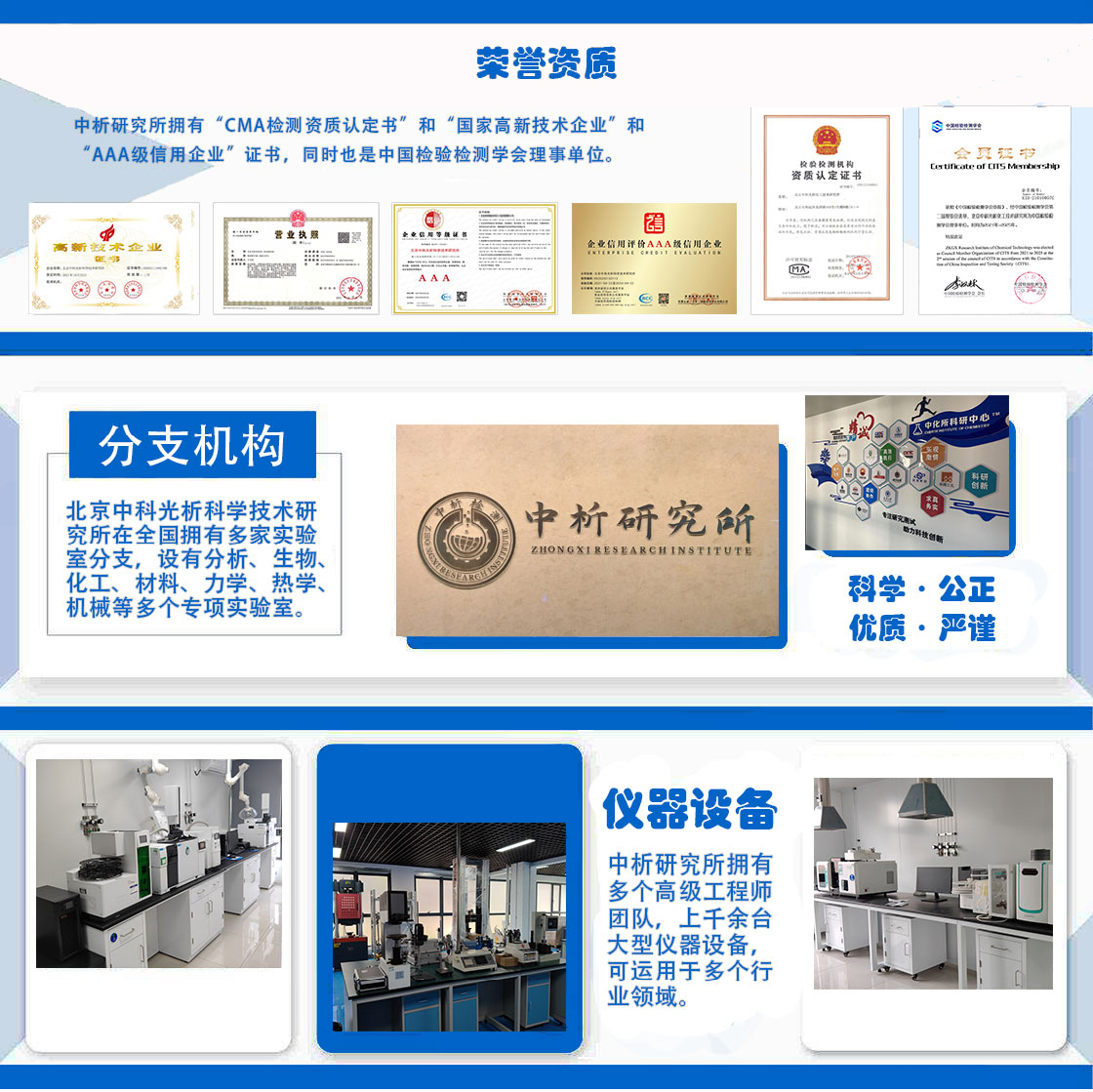
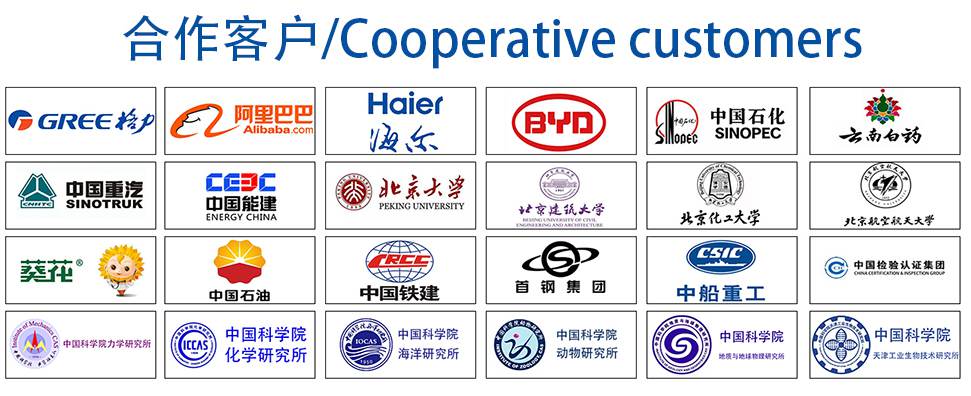