内燃机连杆检测的重要性与核心内容
在内燃机的核心部件中,连杆作为连接活塞与曲轴的关键传动组件,承担着将活塞的往复运动转化为曲轴旋转运动的重要任务。由于其长期承受高频率的冲击载荷、高温高压环境以及复杂的交变应力作用,连杆的结构完整性和性能稳定性直接关系到发动机的整体效率、使用寿命和安全性。因此,连杆检测是发动机制造、维修和质量管理中不可或缺的环节。通过科学系统的检测手段,能够有效发现材料缺陷、加工误差或疲劳损伤等问题,从而避免因连杆失效导致的发动机故障甚至安全事故。
内燃机连杆检测的核心项目
1. 外观与表面质量检测
通过目视检查或光学仪器对连杆表面进行扫描,重点检测裂纹、凹坑、锈蚀等缺陷。特别关注连杆大头和小头过渡区域的应力集中部位,以及螺栓孔、油道等关键位置的表面完整性。
2. 尺寸与形位公差检测
使用三坐标测量仪或专用检具对连杆的关键尺寸进行精密测量,包括:
- 连杆总长度及大小头中心距
- 大端轴承孔和小端衬套孔的直径、圆度、圆柱度
- 两孔轴线平行度与扭曲度
- 螺栓孔位置度与垂直度
确保所有尺寸符合设计图纸的公差要求。
3. 材料性能检测
通过金相分析、硬度测试和拉伸试验等方法验证材料性能:
- 微观组织观察(晶粒度、夹杂物含量)
- 表面与芯部硬度梯度检测
- 抗拉强度、屈服强度及延伸率测试
确保材料满足高强度、抗疲劳和耐磨性的设计要求。
4. 无损探伤检测
采用多技术组合的检测方案:
- 磁粉检测:表面及近表面裂纹检测
- 超声波检测:内部缺陷(气孔、夹杂)定位
- 渗透检测:微裂纹的显像化检查
- X射线检测:复杂结构内部缺陷分析
5. 动平衡与疲劳试验
在专用试验台上进行动态性能测试:
- 动平衡检测:修正质量分布偏差
- 高频疲劳试验:模拟实际工况下的循环载荷
- 极限载荷试验:验证安全系数
通过数据采集系统记录应变、位移等参数变化。
检测技术的发展趋势
随着工业4.0技术的应用,连杆检测正朝着智能化方向发展。三维光学扫描技术可实现全尺寸数字化比对,人工智能算法可自动识别缺陷特征,而在线监测系统则能实时追踪生产过程中的质量波动。这些技术革新显著提升了检测效率和可靠性,为高性能发动机的研发提供了坚实保障。
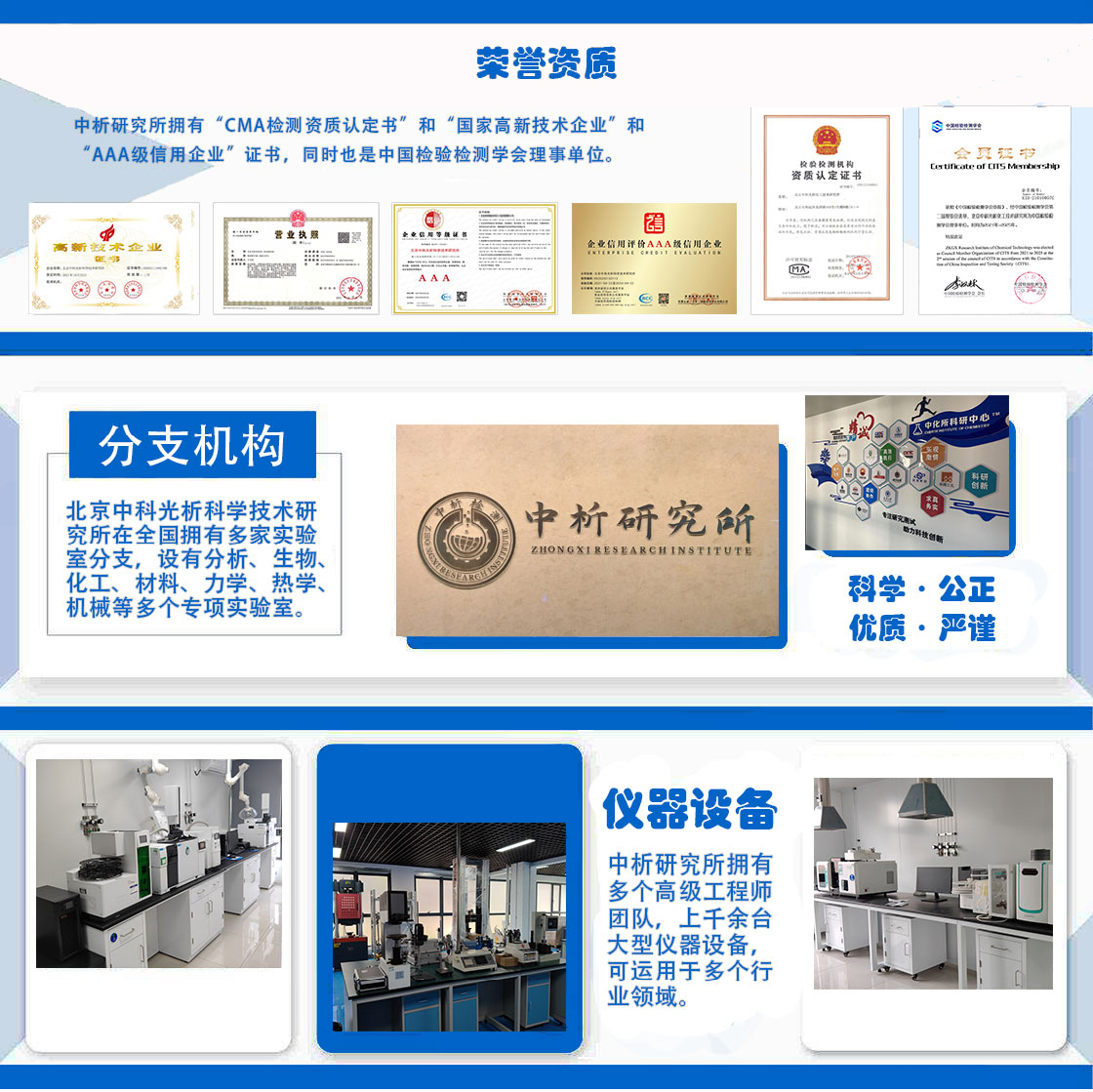
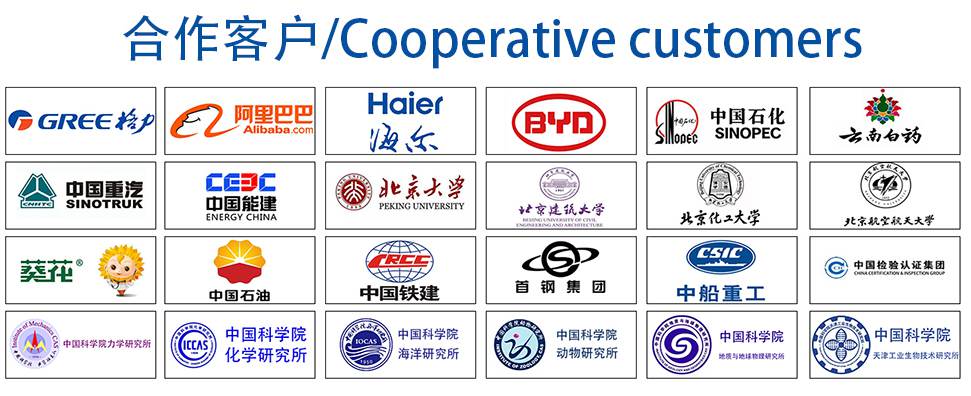