无缝钢管作为工业领域重要的基础材料,广泛应用于石油化工、机械制造、航空航天及能源输送等领域。其生产工艺通过热轧、冷拔或挤压成型,消除了焊缝带来的潜在缺陷风险,具有更高的承压能力和均匀性。然而,生产过程中仍可能因材料成分偏差、加工应力集中或表面处理不当产生质量问题。为确保无缝管子的安全性和可靠性,需通过系统化检测项目对物理性能、化学成分和结构完整性进行全面评估,这对预防设备失效、延长使用寿命具有关键意义。
1. 化学成分分析
采用光谱仪、直读光谱仪等设备检测碳(C)、锰(Mn)、硅(Si)、硫(S)、磷(P)等元素含量,确保符合GB/T 222-2006或ASTM A751标准要求。特殊用途钢管还需检测铬(Cr)、钼(Mo)、镍(Ni)等合金元素比例。
2. 尺寸精度测量
使用激光扫描仪、超声波测厚仪及精密卡尺检测外径、壁厚、椭圆度等参数,依据GB/T 17395-2008标准进行公差判定,其中高压锅炉管壁厚公差需控制在±5%以内。
3. 力学性能测试
通过万能试验机进行拉伸试验(测定抗拉强度Rm、屈服强度ReL),按GB/T 228.1-2021标准执行;采用布氏/洛氏硬度计检测硬度值,确保符合ASTM E18标准要求。
4. 无损检测
• 超声波检测(UT):按GB/T 5777-2019标准探测内部裂纹、夹杂等缺陷
• 涡流检测(ET):依据ISO 9304检测表面及近表面缺陷
• 磁粉检测(MT):用于铁磁性材料表面裂纹检查
• 射线检测(RT):按ASME Section V进行焊缝替代区域检测
5. 表面质量检测
采用目视检查、表面粗糙度仪及三维轮廓仪评估划痕、麻点、氧化皮等缺陷,参照EN 10246-14标准进行表面光洁度分级,精密液压管表面粗糙度Ra值需≤0.8μm。
6. 耐压试验
按照GB/T 241-2007标准实施水压试验,试验压力一般为公称压力的1.5-2倍,保压时间不少于10秒,检测管体渗漏或变形情况。超临界锅炉管需进行400MPa以上超高压测试。
7. 金相组织分析
通过金相显微镜观察晶粒度、非金属夹杂物分布及脱碳层厚度,依据GB/T 13298-2015评定组织类型,确保珠光体含量、铁素体形态符合API 5L等规范要求。
8. 特殊环境测试
对于腐蚀性工况用管,需进行盐雾试验(ASTM B117)、晶间腐蚀试验(GB/T 4334)等;低温服役管道需实施-196℃冲击试验(ASTM E23);高温蠕变试验则用于评估长期服役性能。
通过上述多维度检测体系,可有效识别无缝钢管的潜在缺陷,确保产品满足不同工况需求。现代检测技术如工业CT扫描、数字射线成像(DR)的应用,更提升了检测精度与效率,为高端装备制造提供可靠材料保障。生产企业与第三方检测机构的协同配合,已成为行业质量控制的重要模式。
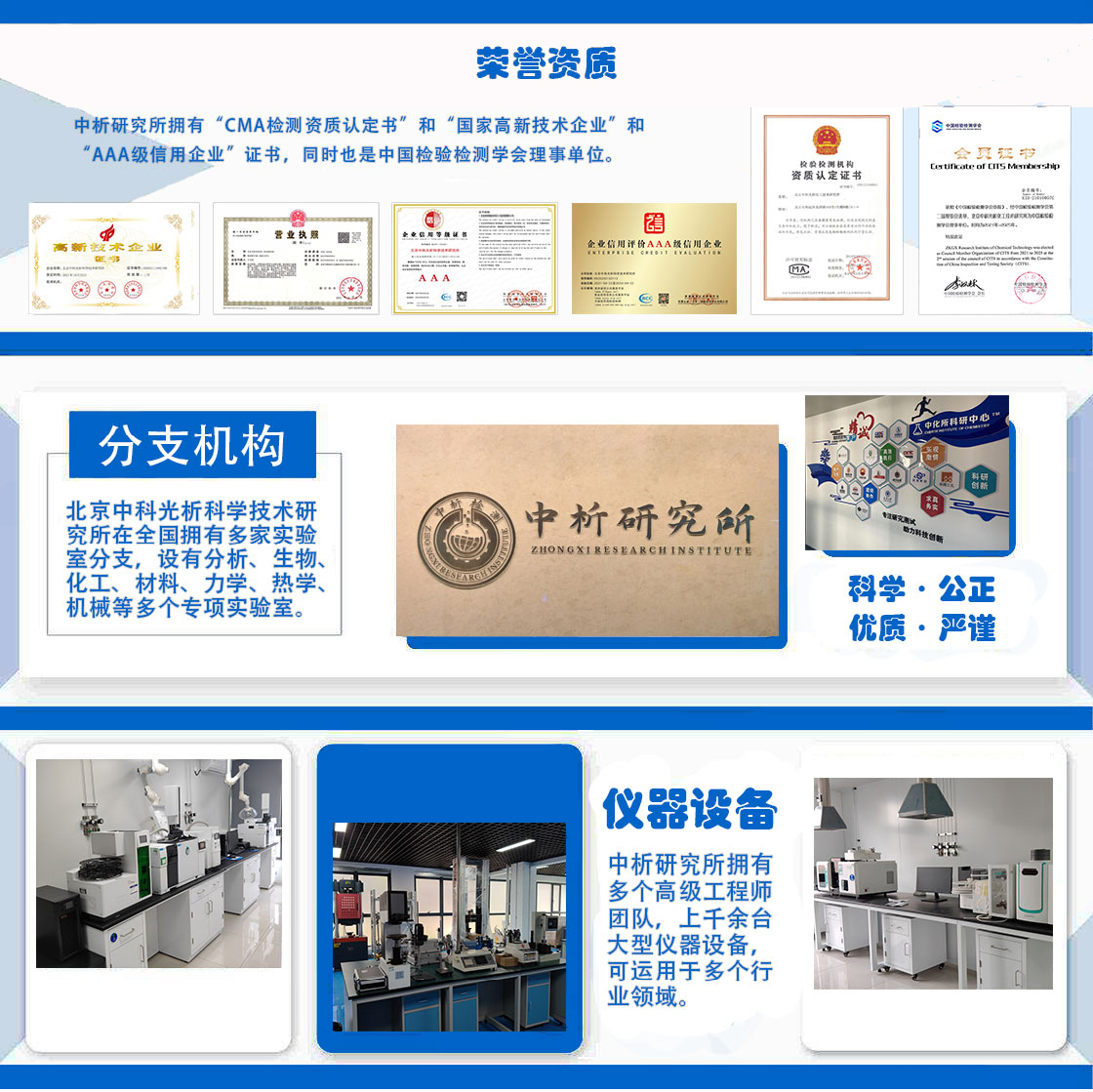
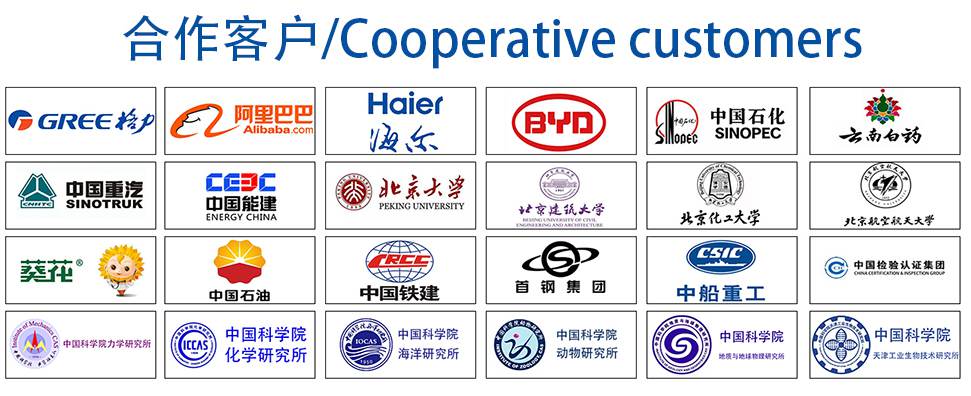