裂缝深度检测:技术与应用解析
在现代工程检测领域,裂缝深度检测是评估结构安全性的核心环节。随着建筑、桥梁、压力容器等设施的老化,以及航空航天、轨道交通等精密设备的长期使用,准确测量裂缝深度对于预防突发性事故、延长构件寿命具有重要意义。根据国际标准ISO 16810:2018,裂缝深度超过材料厚度20%即被视为严重缺陷,需采取紧急修复措施。当前主流的检测技术已从传统目视检查发展为集超声波、电磁感应、激光扫描于一体的系统化解决方案,检测精度可达±0.1mm级别,为工程决策提供了可靠依据。
主流检测方法对比
1. 超声波脉冲反射法:通过发射高频声波测量回波时间差,适合混凝土、金属等均质材料,检测深度范围1-300mm。配备相控阵探头时可实现三维成像,但对表面粗糙度敏感。
2. 电磁涡流检测:利用导体材料中的涡流畸变特征,专用于金属构件,可穿透涂层检测,检测深度约0-10mm,需配合专用校准试块。
3. 激光散斑干涉法:通过加载微小应力后捕捉表面形变,特别适合复合材料层间裂纹检测,分辨率可达微米级,需严格的环境振动控制。
智能检测设备新趋势
新型DCR-9000型数字裂缝测深仪集成AI算法,能自动识别裂缝走向并计算最大深度值,配备的5G模块支持实时上传检测数据至云平台。磁致伸缩导波检测系统采用低频横波技术,单次检测可覆盖50米管道范围,特别适用于油气输送管道的长距离检测。
现场检测关键注意事项
检测前需使用工业内窥镜确认裂缝形态,清除表面锈蚀层至Sa2.5级清洁度。对倾斜裂缝应沿法线方向布置测点,复杂结构建议采用交叉验证法:如混凝土梁可结合超声表面波法与钻孔取芯法,钢结构宜同步使用磁粉检测与TOFD(衍射时差法)技术。
行业应用案例分析
在港珠澳大桥年度检测中,采用相控阵超声技术检测出钢箱梁焊缝内3.2mm深的隐蔽裂纹;某核电站运用红外热像法发现反应堆压力容器0.8mm深的应力腐蚀裂纹,避免了重大安全事故。风电行业推广使用无人机搭载激光雷达,实现叶片表面裂纹深度的大规模快速筛查。
随着MEMS传感器和机器学习技术的融合,裂缝深度检测正朝着智能化、自动化的方向发展。2023年发布的ASTM E2867-23标准新增了数字孪生技术在裂缝评估中的应用规范,标志着该领域正式进入数字化诊断新纪元。
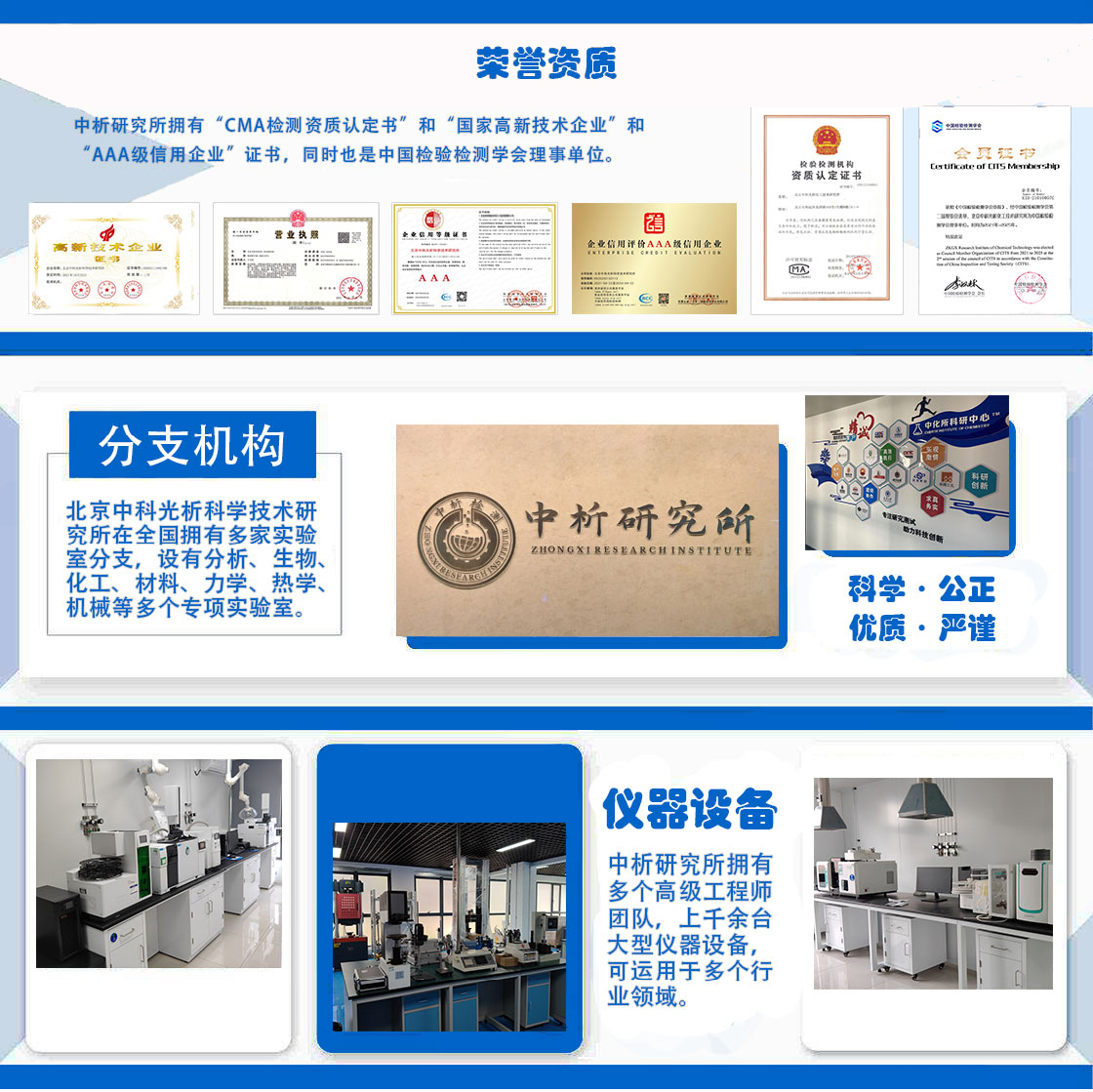
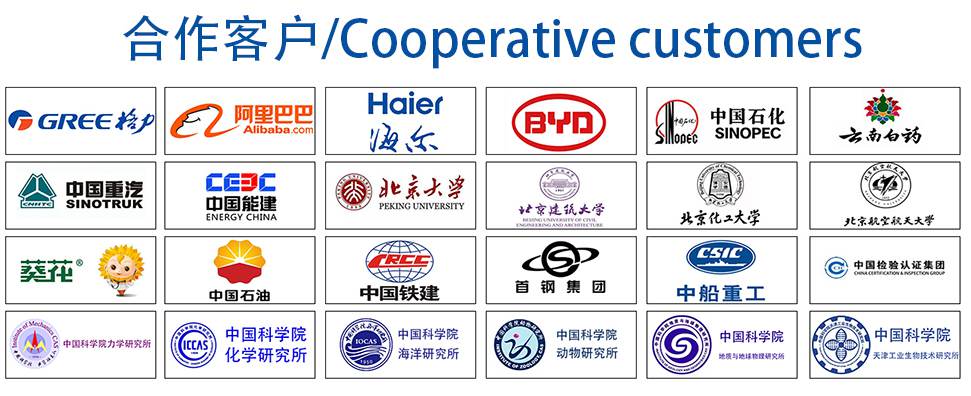