轧制结构钢板材、型材和薄板桩检测的重要性与关键项目
轧制结构钢作为建筑工程、桥梁施工、港口设施及工业设备的核心材料,其性能和质量直接影响结构安全和使用寿命。板材、型材(如H型钢、角钢)和薄板桩(如U型、Z型板桩)在加工、运输及安装过程中可能因工艺偏差、环境因素或材料缺陷导致性能下降。因此,系统化的检测流程是确保材料符合国家标准(如GB/T 1591、ASTM A572)和工程需求的关键环节。通过科学的检测手段,可有效评估材料的力学性能、尺寸精度、表面完整性及耐腐蚀能力,从而避免因材料问题引发的工程事故。
1. 机械性能检测
机械性能是评价结构钢承载能力的基础指标,主要包含以下项目:
· 拉伸试验:测定屈服强度(Rp0.2)、抗拉强度(Rm)、断后伸长率(A%)和断面收缩率(Z%),验证材料是否符合设计要求的力学等级(如Q355B、S355JR)。
· 弯曲试验:通过180°或指定角度的冷弯测试,评估材料在塑性变形时的抗开裂能力,尤其针对弯折部位的应用场景。
· 冲击韧性试验:采用夏比V型缺口试样,在-20℃、0℃等低温条件下测试冲击吸收能量(KV2),确保材料在寒冷环境中的抗脆断性能。
2. 化学成分分析
通过光谱分析仪或化学滴定法检测碳(C)、锰(Mn)、硅(Si)、磷(P)、硫(S)等元素的含量,重点控制以下参数:
· 碳当量(Ceq):计算Ceq= C+Mn/6+(Cr+Mo+V)/5+(Ni+Cu)/15,评估焊接冷裂倾向,要求Ceq≤0.45%(以EN 10025为例)。
· 有害元素限制:硫、磷含量需分别低于0.035%(普通级)或0.025%(优质级),避免热脆性和冷脆性风险。
3. 尺寸与几何公差检测
使用激光测距仪、卡尺、样板等工具对以下参数进行验证:
· 板材:厚度偏差(±0.3mm)、宽度平直度(≤1mm/m)、对角线误差(≤3mm/10m)。
· 型材:腹板高度、翼缘宽度公差(±2mm)、截面不对称度(≤1.5%)、直线度(≤L/1000且≤5mm)。
· 薄板桩:锁口配合精度(间隙≤0.5mm)、单桩长度误差(-0/+30mm)、桩身扭转度(≤1°)。
4. 表面质量与缺陷检测
通过目视检查、磁粉探伤(MT)或渗透探伤(PT)识别以下缺陷:
· 轧制缺陷:氧化皮剥落、折叠、划痕深度超过0.2mm。
· 裂纹与分层:表面裂纹长度>5mm或深度>1%壁厚需判废,内部分层需通过超声波检测(UT)定位。
· 腐蚀痕迹:针对库存超6个月的钢材,检测点蚀深度是否超过公称厚度的5%。
5. 特殊性能专项检测
根据应用场景增加针对性测试:
· 焊接性能评估:对焊材与母材进行斜Y型坡口试验,检测热影响区裂纹率。
· 涂层附着力测试:对镀锌层(≥275g/m²)或环氧涂层进行划格试验(ISO 2409),要求达到1级附着力。
· 耐候性验证:对耐候钢(如09CuPCrNi-A)进行周期浸润腐蚀试验,评估锈层稳定化能力。
结语
轧制结构钢的检测需贯穿原材料入场、加工过程及成品验收全阶段,通过多维度检测数据的交叉验证,可精准识别材料缺陷并量化性能参数。企业应建立涵盖ISO 9001和ISO/IEC 17025标准的检测体系,结合数字化的数据管理平台,实现质量风险的系统化防控,为重大工程的安全运营提供可靠保障。
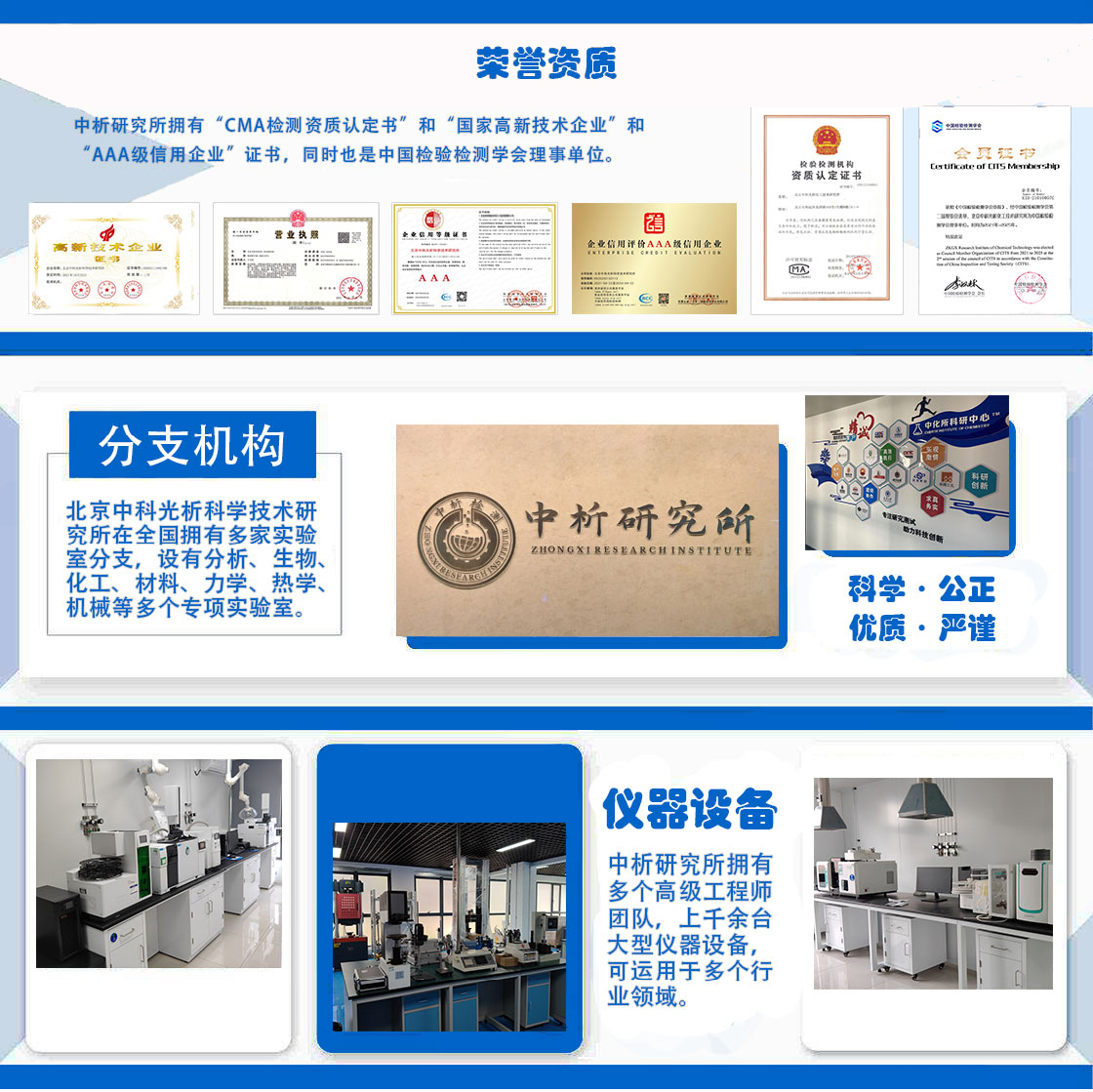
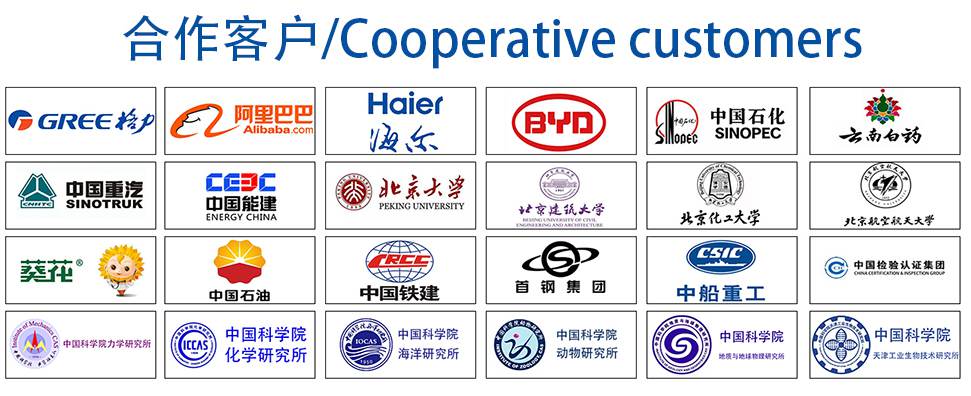