燃气输送用不锈钢管检测的重要性
燃气输送用不锈钢管作为城市燃气系统、工业燃气传输的关键组成部分,其质量直接关系到能源输送的安全性和稳定性。不锈钢管因其耐腐蚀性、高强度及长寿命等特性被广泛应用,然而在复杂工况下(如高压、高温、化学腐蚀等),任何材料缺陷或加工工艺问题都可能引发泄漏甚至爆炸事故。因此,对不锈钢管进行严格的检测是确保燃气输送安全的必要环节。检测项目需覆盖原材料性能、加工工艺、成品质量以及长期使用可靠性等多个维度,以满足国家标准(如GB/T 12771、GB/T 14976)和行业规范要求。
核心检测项目及技术要点
1. 化学成分分析
不锈钢管的耐腐蚀性和力学性能与其化学成分密切相关。检测需通过光谱分析仪或化学滴定法,验证材料中铬(Cr)、镍(Ni)、钼(Mo)、碳(C)等元素的含量是否符合标准(如304、316L等牌号要求)。例如,铬含量需≥16%以保证抗氧化能力,镍含量影响抗酸腐蚀性能。若成分偏离标准,可能导致管道在潮湿或酸性环境中加速腐蚀。
2. 力学性能测试
包括拉伸试验、硬度测试和冲击试验: - 拉伸试验:测定抗拉强度、屈服强度和延伸率,确保管道在高压下不发生塑性变形或断裂。 - 硬度测试:通过布氏或洛氏硬度计评估材料加工硬化程度,避免因硬度过高导致脆性增加。 - 冲击试验:模拟低温环境下材料的韧性,防止管道在寒冷地区发生脆性断裂。
3. 尺寸与外观检查
通过激光测径仪、超声波测厚仪等设备,精确测量管道外径、壁厚及椭圆度,确保尺寸公差符合GB/T 21833标准。外观检查需关注表面是否存在裂纹、划痕、凹坑等缺陷,并使用内窥镜观察内壁光滑度,避免因粗糙表面增加流体阻力或引发局部腐蚀。
4. 耐腐蚀性测试
针对燃气中可能含有的硫化氢(H₂S)、二氧化碳(CO₂)等腐蚀性介质,需进行盐雾试验、晶间腐蚀试验或点蚀电位测试。例如,按ASTM G48标准进行点蚀检测,评估材料在Cl⁻环境中的抗局部腐蚀能力,防止微小蚀孔发展为穿透性缺陷。
5. 无损检测(NDT)
采用涡流检测(ECT)、超声波检测(UT)或射线检测(RT)技术,识别管道内部的气孔、夹渣、未焊透等隐蔽缺陷。例如,超声波检测可精准定位焊缝区域的裂纹深度,涡流检测适用于快速筛查表面及近表面缺陷。
6. 压力测试与气密性验证
通过水压试验或气压试验模拟实际工作压力(通常为设计压力的1.5倍),持续保压10-30分钟,观察是否出现渗漏或变形。气密性测试则使用氦质谱检漏仪或肥皂泡法,确保管道在长期运行中无微小泄漏风险。
结语
燃气输送用不锈钢管的检测是一个多学科交叉的系统工程,需结合材料科学、机械工程及检测技术的专业知识。仅通过全面、精准的检测流程,才能保障管道在全生命周期内安全可靠地运行,为燃气基础设施的稳定供应提供坚实支撑。
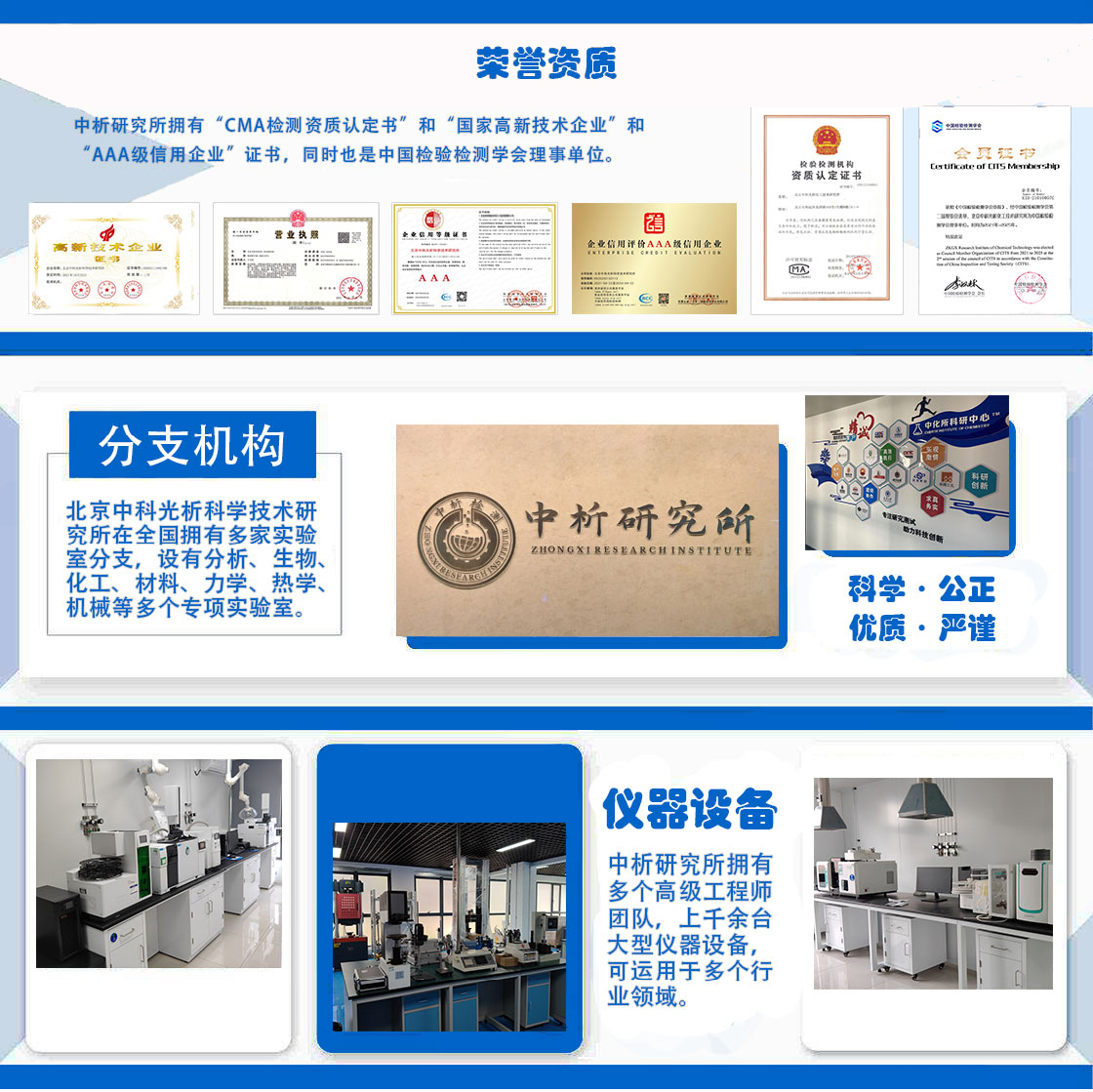
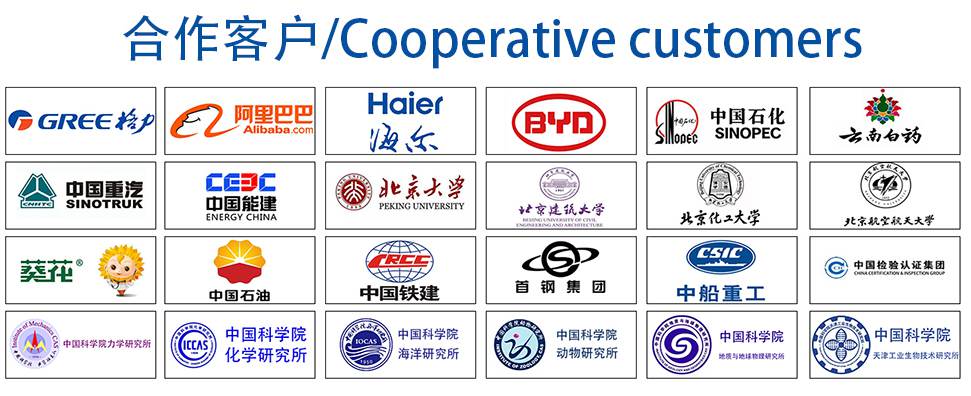