塑料管道系统-机械连接的聚烯烃压力管及配件检测
聚烯烃压力管(如PE、PP材料)及其配件凭借优异的耐腐蚀性、柔韧性及长寿命,被广泛应用于供水、燃气输送、工业流体传输等领域。为确保管道系统的安全性和可靠性,机械连接作为关键安装方式,其质量直接影响系统的密封性和承压能力。因此,针对机械连接的聚烯烃压力管及配件开展系统性检测至关重要。检测内容需覆盖材料性能、连接强度、耐压能力、环境适应性等核心指标,同时严格遵循ISO 4427、ASTM D3035等国际及行业标准,以保障管道系统在复杂工况下的长期稳定运行。
1. 材料性能检测
对聚烯烃管材及配件的原材料进行基础物性分析是检测的第一步。重点包括:密度、熔融指数(MFI)、氧化诱导时间(OIT)等指标测试,以验证材料是否符合规定牌号要求。此外,需通过差示扫描量热法(DSC)评估材料的热稳定性,避免因加工或使用温度异常导致性能劣化。
2. 尺寸与几何精度检测
管道及配件的尺寸公差直接影响机械连接的密封效果。检测项目涵盖:管材外径、壁厚均匀性、椭圆度,以及配件承插口的直径、深度、倒角角度等参数。对于带螺纹的机械连接件,还需使用螺纹规检测螺距和齿形精度,确保配合严密性。
3. 连接强度与密封性测试
机械连接的可靠性是核心检测内容,主要包括:
- **拉伸试验**:模拟管道轴向受力,检测连接部位在特定拉力下的位移量和破坏模式;
- **弯曲试验**:评估连接件在弯曲应力下是否发生泄漏或结构失效;
- **水压密封试验**:在1.5倍额定压力下保持一定时间,观察是否有渗漏现象;
- **扭转试验**:针对旋转式机械连接件,测试其抗扭强度与耐久性。
4. 耐压与爆破压力测试
通过分级加压方式测定管材及连接件的短期爆破压力,同时结合静液压试验(如ISO 1167标准)评估长期承压性能。测试需在20℃、60℃等不同温度条件下进行,以模拟实际使用环境对材料强度的影响。
5. 环境适应性评估
针对管道可能接触的化学介质(如酸碱溶液、油脂)进行耐腐蚀性测试,并开展温度循环试验(-20℃至+40℃交替变化),验证连接部位在热胀冷缩条件下的密封保持能力。对于户外应用场景,还需模拟紫外线老化、冻融循环等极端环境的影响。
6. 长期性能验证
通过蠕变试验、应力松弛试验预测连接结构在长期负载下的形变趋势,并结合加速老化试验(如高温高压水环境)推估系统使用寿命。部分检测项目需持续数千小时,以获取可靠的耐久性数据。
检测意义与行业规范
严格的检测流程可有效避免因连接失效导致的泄漏、爆管等事故,同时延长系统使用寿命。生产企业需依据GB/T 13663、EN 1555等标准建立质量控制体系,第三方检测机构应通过CMA/ 认证,确保检测数据的权威性。随着智能化检测技术的发展,内窥镜成像、超声波探伤等无损检测手段正逐步应用于连接界面的微观缺陷诊断。
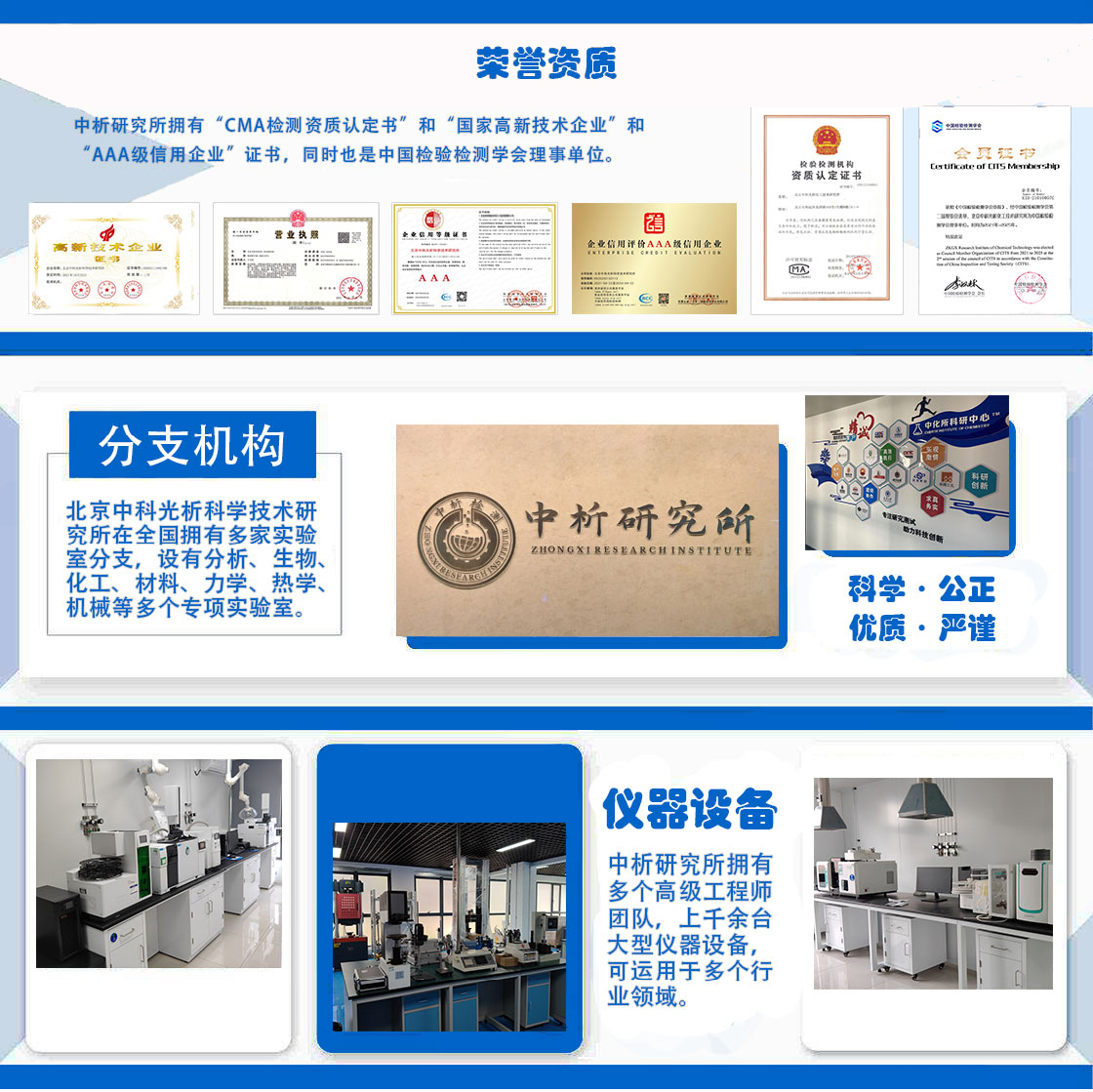
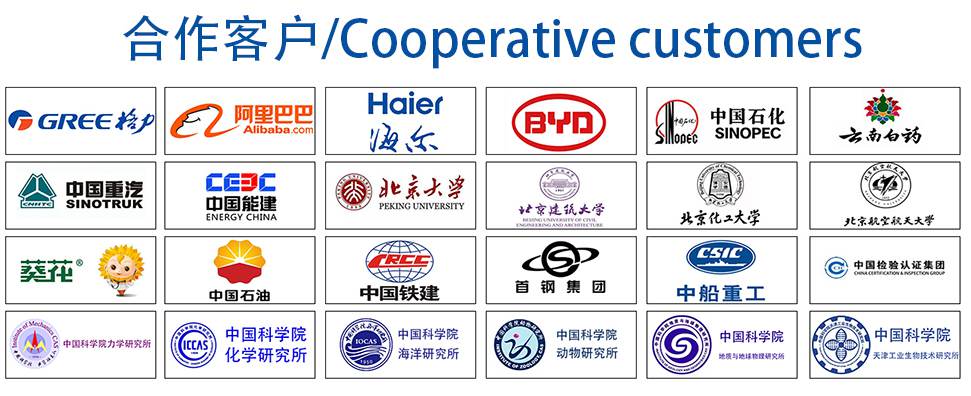