钢制焊接常压容器检测项目及技术要求
钢制焊接常压容器作为工业领域广泛使用的储存设备,其安全性直接关系到生产系统的稳定运行和人员安全。根据GB/T 16508《钢制焊接常压容器》及NB/T 47003.1《常压容器》等相关标准,常压容器的检测需覆盖材料、制造工艺、焊接质量及功能性验证等多个维度。检测应贯穿设计、制造、安装及使用全生命周期,确保容器在非压力工况下满足强度、密封性和耐久性要求。
一、外观与几何尺寸检测
外观检测需通过目视或放大镜检查容器表面是否存在裂纹、凹陷、变形等缺陷,重点关注焊缝区域及应力集中部位。几何尺寸检测包括:
1. 筒体圆度偏差≤1%公称直径;
2. 焊缝错边量≤10%板厚且≤2mm;
3. 法兰密封面平面度≤0.3mm/m。
需使用激光测距仪、超声波测厚仪等设备进行数据采集,确保符合图纸及标准公差要求。
二、焊缝质量无损检测
焊接接头的检测是质量控制核心环节,常采用以下方法:
1. 渗透检测(PT):用于表面开口缺陷检测,灵敏度需达到ASME V级标准;
2. 磁粉检测(MT):适用于铁磁性材料表面及近表面缺陷探查;
3. 超声波检测(UT):针对对接焊缝内部缺陷(如未熔合、夹渣等),检测范围应覆盖焊缝全长10%以上;
4. 射线检测(RT):对重要角焊缝进行抽检,底片质量不低于AB级,缺陷评级按JB/T 4730执行。
三、材料性能验证
材料复验项目包括:
1. 钢材化学成分分析(光谱仪检测);
2. 力学性能试验(拉伸、弯曲、冲击);
3. 焊接试板工艺评定;
4. 材料硬度测试(HBW≤200)。
需核查材料质保书与实物标记的一致性,Q345R等常用板材的屈服强度应≥345MPa。
四、密封性及功能试验
常压容器需完成以下功能性验证:
1. 盛水试漏:注水至设计液位,保压24小时无渗漏;
2. 气密性试验:采用0.03-0.05MPa压缩空气,涂刷发泡剂检查泄漏点;
3. 沉降试验:安装后监测基础沉降量,72小时内沉降差≤5mm;
4. 附件功能测试:包括人孔密封性、呼吸阀启闭压力校验等。
五、防腐及安全附件检测
针对使用环境进行专项检查:
1. 涂层厚度测量(干膜厚度≥200μm);
2. 阴极保护系统电位检测(-0.85~-1.1V vs CSE);
3. 衬里完整性检查(电火花检测电压≥5kV);
4. 安全阀、液位计等附件需提供校验证书且在有效期内。
检测过程中发现的不合格项应按ASME PCC-2或GB 50236要求进行返修,并重新进行局部或整体检测。定期检验周期不得超过5年,腐蚀严重区域应缩短至2年。检测数据需形成完整报告并存档至少10年,为容器全寿命周期管理提供依据。
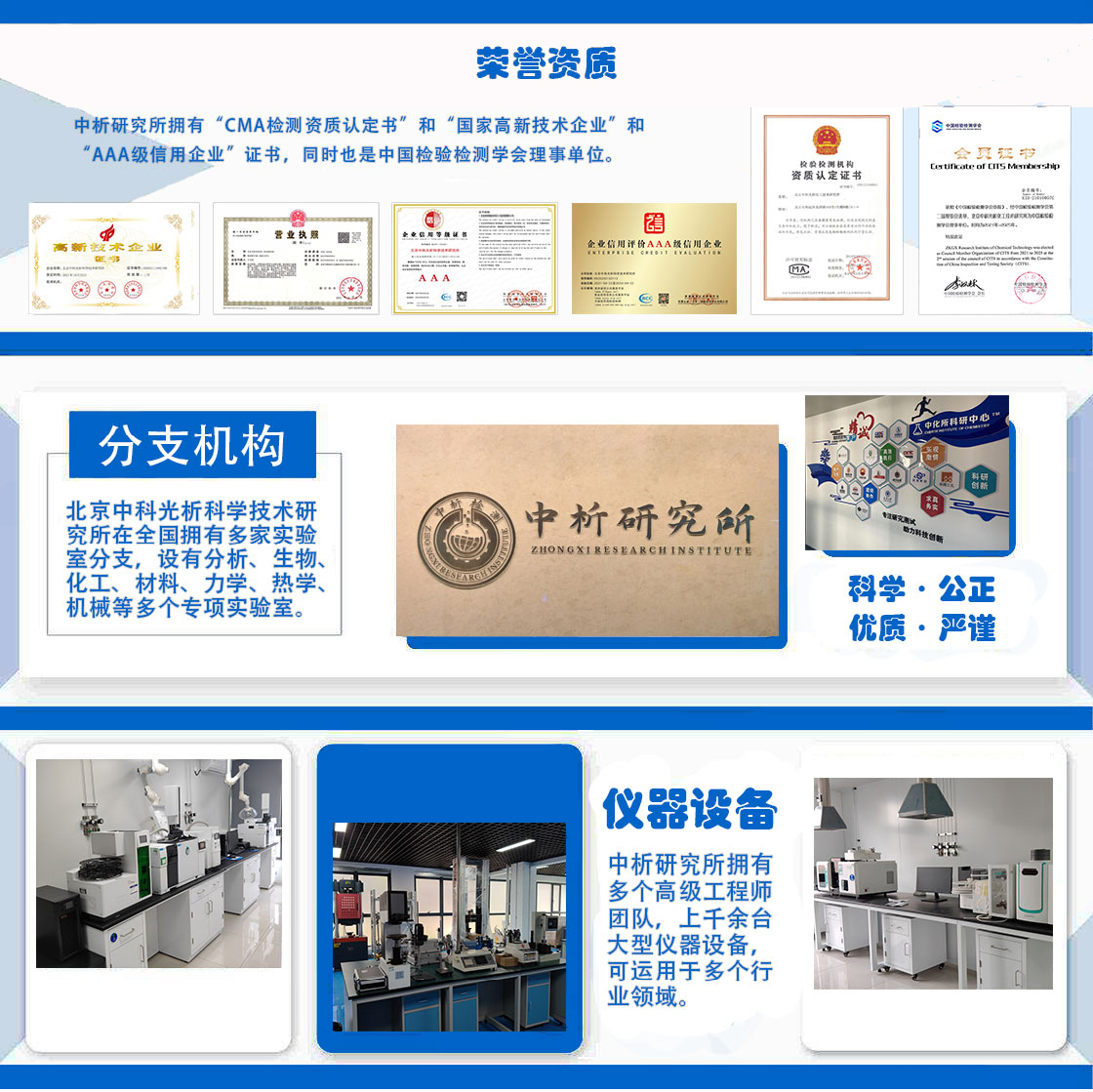
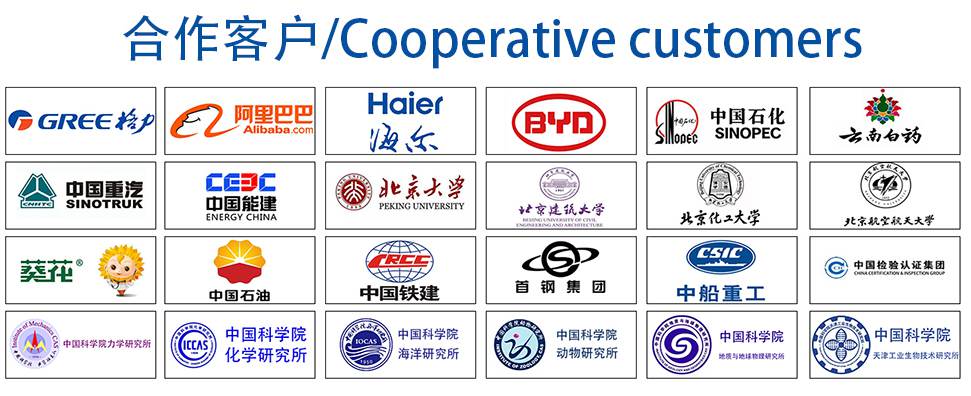